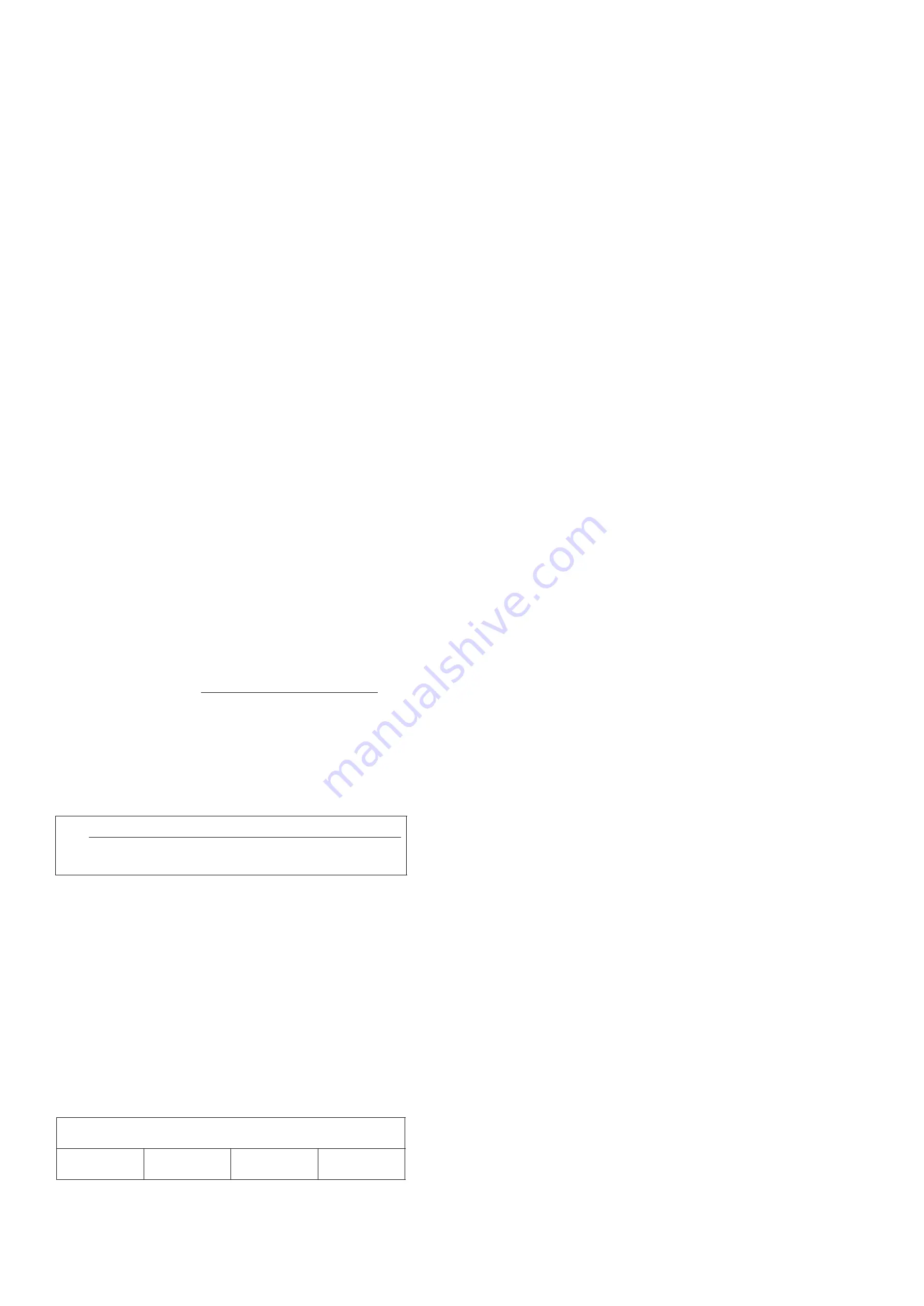
Rules for Failsafe Operation of an S5-95F
S5-95F
18.10.2 Depassivating I/Os
Faulty sensors and actuators are frequently the cause of I/O passivation. If the problem with sensors
and/or actuators can be eliminated while the PLC is at RUN, you can depassivate the I/Os with
FB255. The depassivated I/Os are then once again incorporated into the user program.
If possible, you should always depassivate only one signal group. We therefore recommend
assigning each signal group a separate depassivation bit. A detailed description on invoking and
initializing FB255 was presented in Chapter 9.
Note
Before reactivating the I/Os in a signal group with FB255, you must branch to a routine
in your user program in which all variables needed for depassivation are checked,
evaluated and, where necessary, updated or the process variables reinitialized.
Note that depassivation with FB255 resets the passivation bit in the system event DB. Actually, this
bit is reset even before depassivation has been completed (the I/Os are not yet ready and the
parameter assignment error byte (PAFE) shows "Test in progress").
Extending of the PLC Cycle Time and Multiple FB255 Calls
Each time FB255 is invoked, the S5-95F executes only part of the total I/O test. To shorten the test
run, it is therefore recommended that FB255 be invoked more than once in the cyclic program.
FB255 calls are allowed only when FB252 is not in the process of executing an I/O test (DI, DQ,
interrupt DI or counter test). You can evaluate FB252's PAFE byte to make sure that this is not the
case (PAFE = D0
H
).
Note that each FB255 call increases the cycle time by approximately 30 ms. The cycle time
watchdog timer remains unchanged (i.e. there is no automatic retriggering of the watchdog timer).
Example:
Depassivating I/Os
A boiler is heated by four burners. Each burner is independent of the others, so that control of each
burner is a separate subprocess. Signal groups 11 to 14 are assigned to the I/Os for these
subprocesses.
The control system as a whole is monitored by a preliminary interlock. Since the preliminary
interlock applies for all four burners and plays a central role as far as safety is concerned, the I/Os
needed for it are assigned signal group 0.
Figure 18-1.
Subdivision of the I/Os into Signal Groups
Preliminary Interlock for the Burner Control System
I/Os in signal group 0
Burner 1
I/Os in signal group 11
Burner 4
I/Os in signal group 14
Burner 3
I/Os in signal group 13
Burner 2
I/Os in signal group 12
18-18
EWA 4NEB 812 6210-02