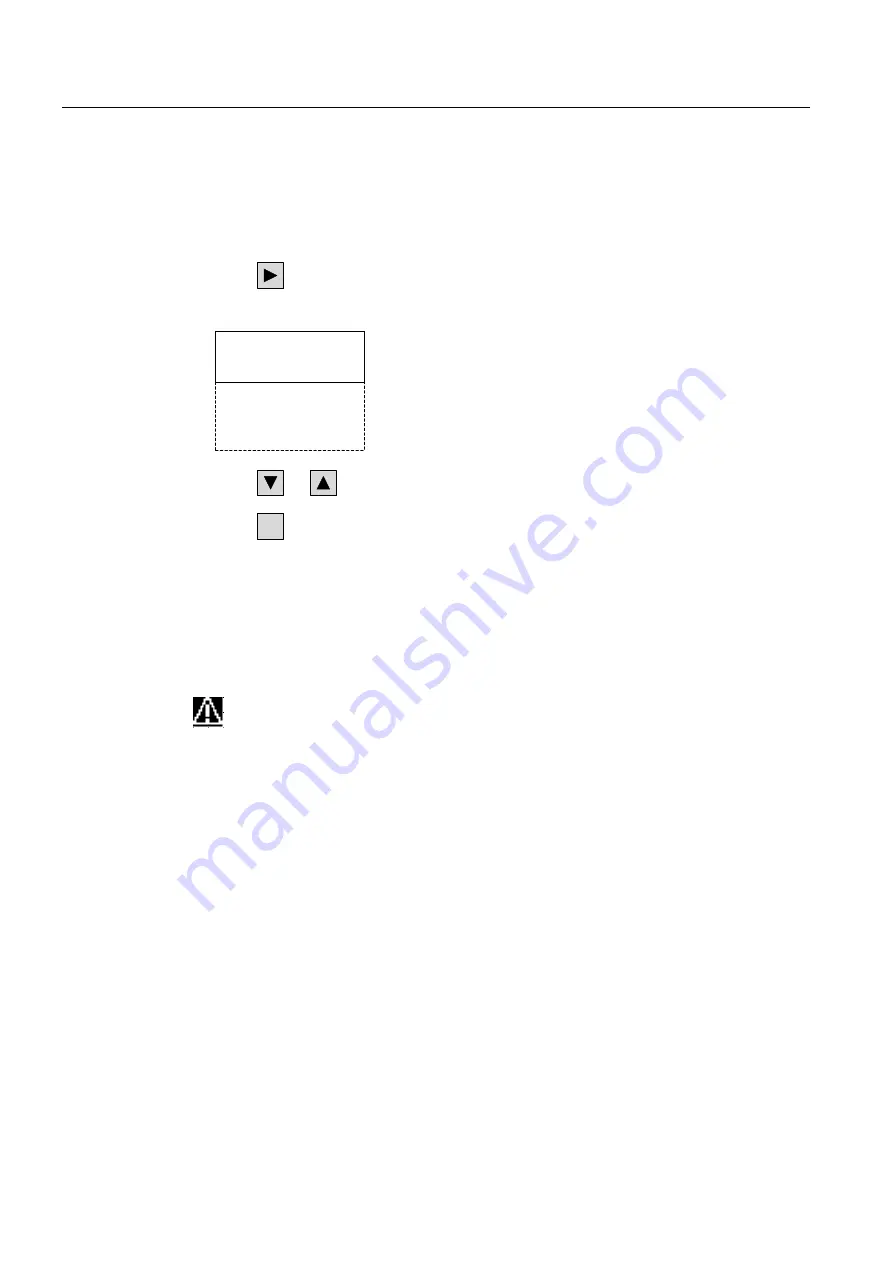
Operating alarms
9.2 Operating alarms on the OP 73micro
OP 73micro, TP 177micro (WinCC flexible)
130
Operating Instructions, 09/2007, 6AV6691-1DF01-0AB0
Viewing long alarm text
The alarm text window can be used to view infotexts which can not be output in full length in
the alarm view.
1.
Select the alarm using the cursor keys.
2.
Press
INS
.
This opens the alarm text window shown below.
502 15:05:49 Alarm
switch off unit 4,
close by-pass stop valve 2,
open pipes 12 and 53,
disconnect main linkage,
start cooling unit 23 and
acknowledge buttom ACK
3.
Press
+/–
or
TAB
to view the full alarm text.
4.
Press
ESC
HELP
.
This closes the alarm text window.
Alarm indicator
The alarm indicator is a graphic symbol that shows alarms to be acknowledged.
The following figure shows the alarm indicator:
The alarm indicator flashes as long as alarms are queued for acknowledgment. The alarm
indicator is displayed and does not flash as long as acknowledged alarms are still queued.
When no alarm is in the queue, the alarm indicator is hidden.