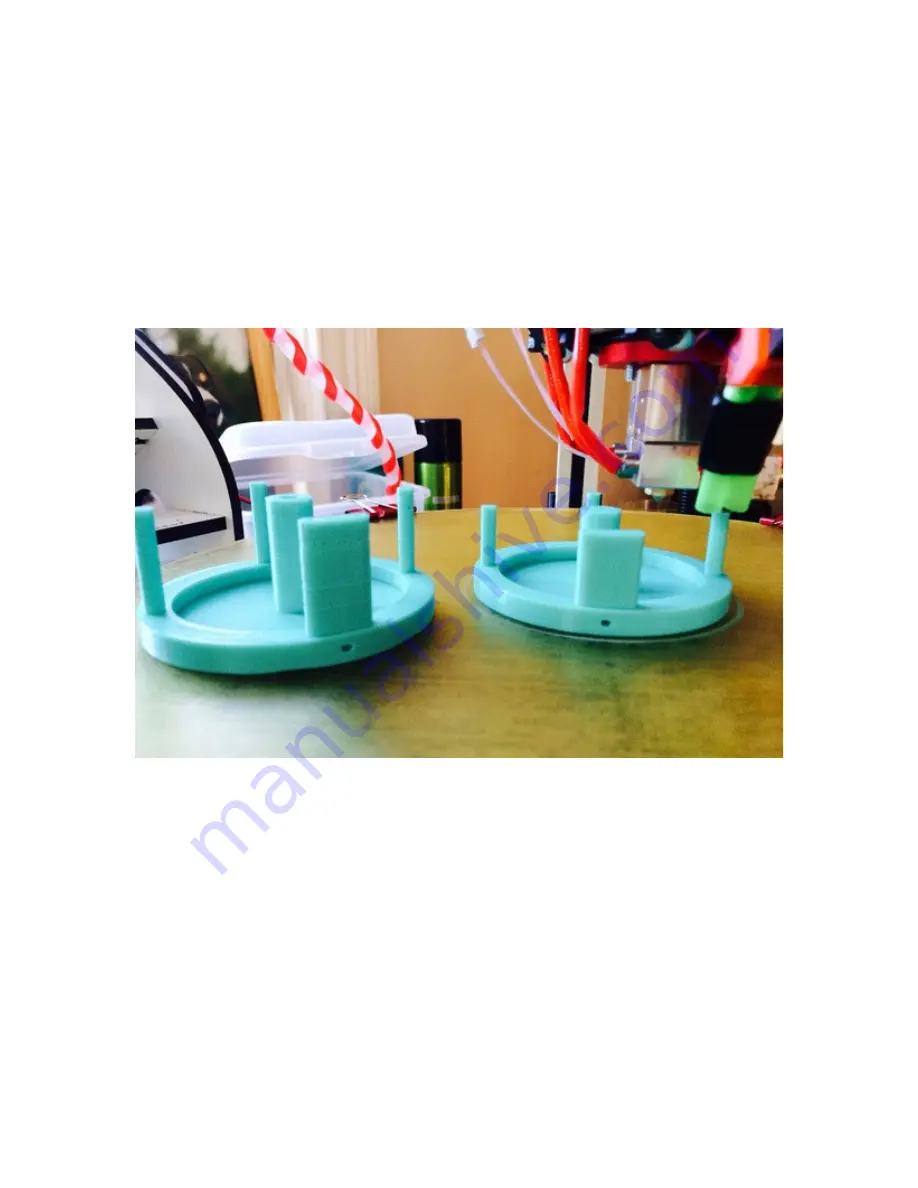
When you do determine you have a problem that only a fan can solve, start
conservatively. I also seriously recommend using a duct of some sort to focus the air flow where
you need it. Ideally, the fan would have the ability to follow the print nozzle and direct a small
stream of air to the filament right after it is laid down. That is a difficult problem to solve, so most
of us direct the air to area around and under the nozzle. But, by directing the air (duct) you can
reduce the air flow significantly since it is now focused where you need it. Here is an example of
some of my fan research. The part on the left failed (in a previous run) as you can see due to
warping caused by an uneducated 25mm inducted fan blowing at 50%. The part being printed
on the right was my first attempt at using flexible soda straws (2 of them) to direct the air flow to
exactly where I needed it. I also ran the fan at 20%
The angle of the photo doesn't show it clearly but the "double barrels" are focused at the
tip of the nozzle. The "dead air" space between the tubes prevents air from flowing over the
nozzle. I know, it's terribly clever! It's a work in progress and I've almost got it perfected with a
printed double barrel nozzle.
I suggest doing your own experiments and observations but start conservatively. I don't
use a fan during the entire part. If you find you need to turn the fan on at full blast from no air
flow, do it in stages so the hot end can equilibrate properly. You can do this manually, some
slicers can support it, or it is easy enough to learn the simple "fan mcodes" to manually insert
them where you need them in the gcode file (this is what I do for tricky parts).
M107 is fan off
M106 S50 turns the fan on at 50% - the S parameter is the speed from 0 to 100
41