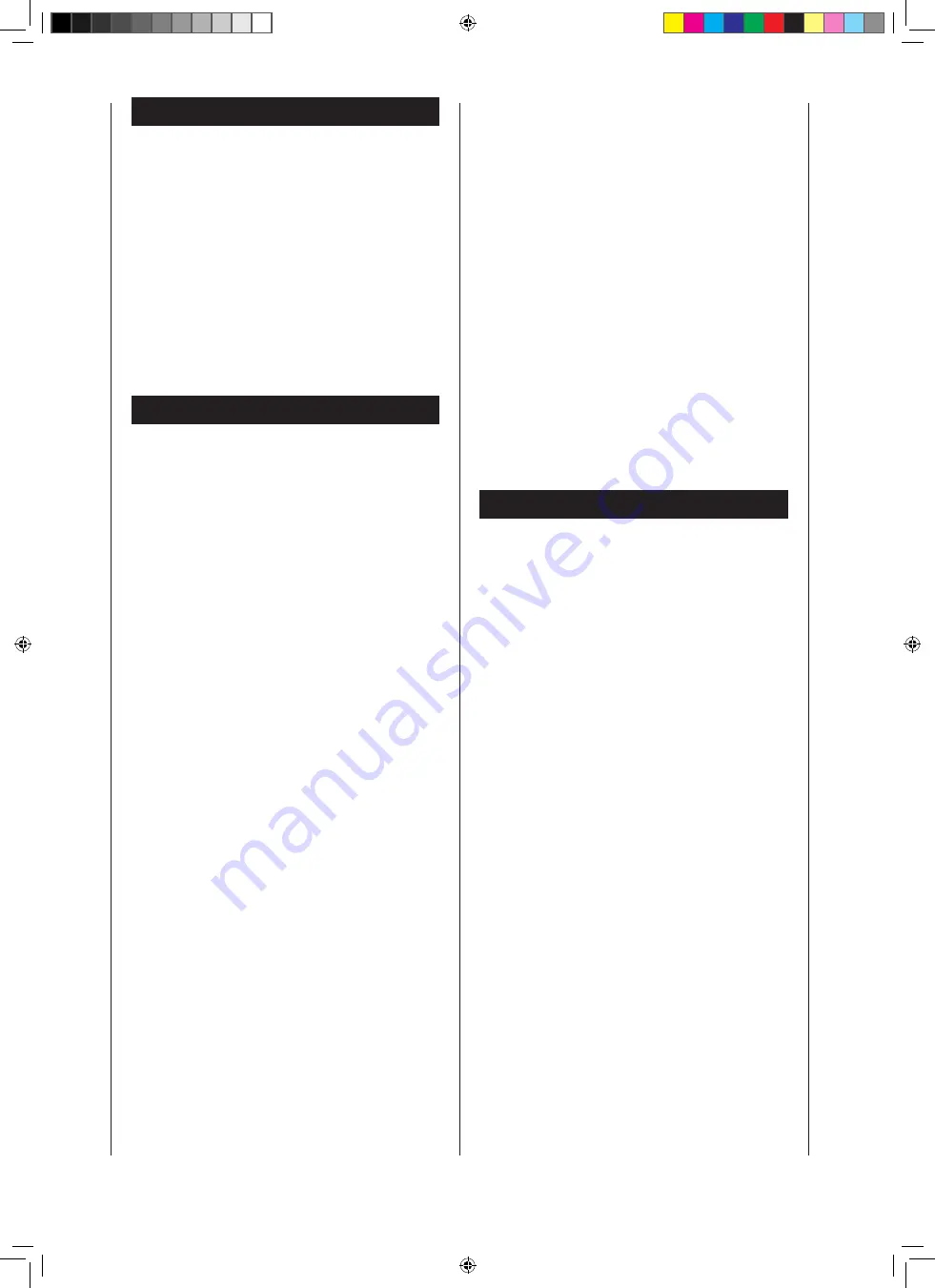
english 15
equipment
1 Base plate
2 Pillar
3 Drilling table
4 Machine head
5 Toothed rack
6 Guide ring of toothed rack
7 Crank
8 Keyless drill chuck
9 Grips
10 Drill chuck protection
11 Depth stop
12 Motor
13 On-Off switch
14 Belt protective hood
15 Belt clamping lever
16 Locking grip for belt tension
AssemBlY instructions
wArning:
For your own safety never connect plug to power source
outlet until all assembly steps are completed and you have
read and understood the safety and operational instruc-
tions
column to base, Fig.4
1 Position base {A) on floor or bench.
2 Place column assembly {B) on base and align holes in
column support with holes in base.
3 To attach and fasten the pillar unit, screw the three
(or 4) screws (a) into the base plate and tighten them
with a wrench.
table and pillar, Fig. 5.1 stb t13
1 Slide the drilling table (3) onto the pillar (2). Position
the table directly above the base plate.
2 Install the table bolting (b) in the table unit from the
left side and tighten it.
table and pillar, Fig. 5.2 – 5.3 stb t16 / stb s16
1 Slide the drilling table (3) with the toothed rack (5)
onto the pillar (2).
2 Install the table bolting (b) in the table unit from the
left side and tighten it.
3 Place the crank (7) onto the bolt and fasten the Allen
screw.
machine head and pillar, Fig. 6
1 Place the machine head (4) onto the pillar (2).
2 Put the spindle of the drilling machine with the table
and the base plate in the cover and fasten the 2 Allen
screws (c).
drill chuck protection with depth stop, Fig. 7.1 (only stb t13 )
Fit the chuck protection with depth stop (11) onto the
spindle pipe and tighten the slotted screw (d).
Caution! The depth stop must be fed through the drill-
ing (17) on the housing. Screw on the two nuts (e) and
place the indicator (g) onto the depth stop. The indicator
(g) must point at the scale.
drill chuck protection, Fig. 7.2
(only stb t16 and stb s16)
Fit the chuck protection (10) onto the spindle pipe and
fasten the slotted screw (d).
Feed handles to the shaft hub.
Screw the feed handles (A) tightly into the threaded holes
in the hub (B).
installing the chuck, Fig. 9
1 Clean the conical hole in the chuck (A) and the spindle
cone with a clean piece of fabric. Make sure there are
no foreign particles sticking to the surfaces. The slight-
est piece of dirt on any of these surfaces will prevent
the chuck from seating properly. This will cause the
drill bit to wobble“. If tapered hole in the chuck is
extremely dirty, use a cleaning solvent on the clean
cloth.
2 Push the chuck up on the spindle nose as far as it
wiII go.
3 Turn chuck sleeve anticlockwise (when viewed from
above) and open jaws in chuck completely.
4 Legen Sie ein Stück Holz auf den Maschinentisch
und senken Sie die Spindel bis auf das Holzstück ab.
Drücken Sie fest, damit das Futter genau sitzt.
Fastening radial drill press to supporting surface
For your own safety, it is highly recommended to install
the machine on a bench or similar.
AdJustments
wArning:
All the necessary adjustments for the good working of your
drill press have been done at the factory .Please do not
modify them.
However, because of a normal wear and tear of your tool,
some readjustments might be necessary .
wArning:
Always unplug our tool from power source before any ad-
justment“
Quill return spring, Fig. 10.1–10.2
It may be necessary to adjust your quill return spring if the
tension is such that the quill returns either too rapidIy or
too slowly
1 Lower table for additional clearance.
2 Work from left side of drill press.
3 Move the stop nuts (A) down to their lowest position
and lock in place with wrench to prevent quill dropping
while tensioning spring.
Place screwdriver in lower front notch (8) of spring cap
(C), and hold it in place while loosening and removing
jam (outer) nut (D) only.
4 With screwdriver remaining in notch, loosen large
standard (inner) nut (E) until notch disengages from
boss (F) on head. Do not remove this nut.
5 Carefully turn screwdriver anticlockwise and engage
next notch in boss. Do not remove screwdriver.
6 Tighten standard nut with wrench onIy enough to en-
gage boss. Do not over tighten as this will restrict quill
movement.
7 Move stop nuts and depth pointer to upper most posi-
tion and check tension while turning feed handles.
8 If there is not enough tension on spring, repeat steps
3-8 moving onIy one notch each time and checking ten-
sion after repetition. Proper tension is achieved when
quill returns gent I y to full up position when released
from 20 mm-3/4“ -depth.
9 When there is enough tension after checking, „ replace
jam nut and tighten to standard nut, but do not over
tighten again standard nut.
stb Bohrmaschinen 2012.indd 15
17.02.12 09:34
Содержание stb s16
Страница 94: ...94 SLO stb Bohrmaschinen 2012 indd 94 17 02 12 09 34...
Страница 95: ...international 95 stb t16 stb Bohrmaschinen 2012 indd 95 17 02 12 09 34...
Страница 96: ...96 international stb s16 stb Bohrmaschinen 2012 indd 96 17 02 12 09 34...
Страница 98: ...98 international stb Bohrmaschinen 2012 indd 98 17 02 12 09 34...