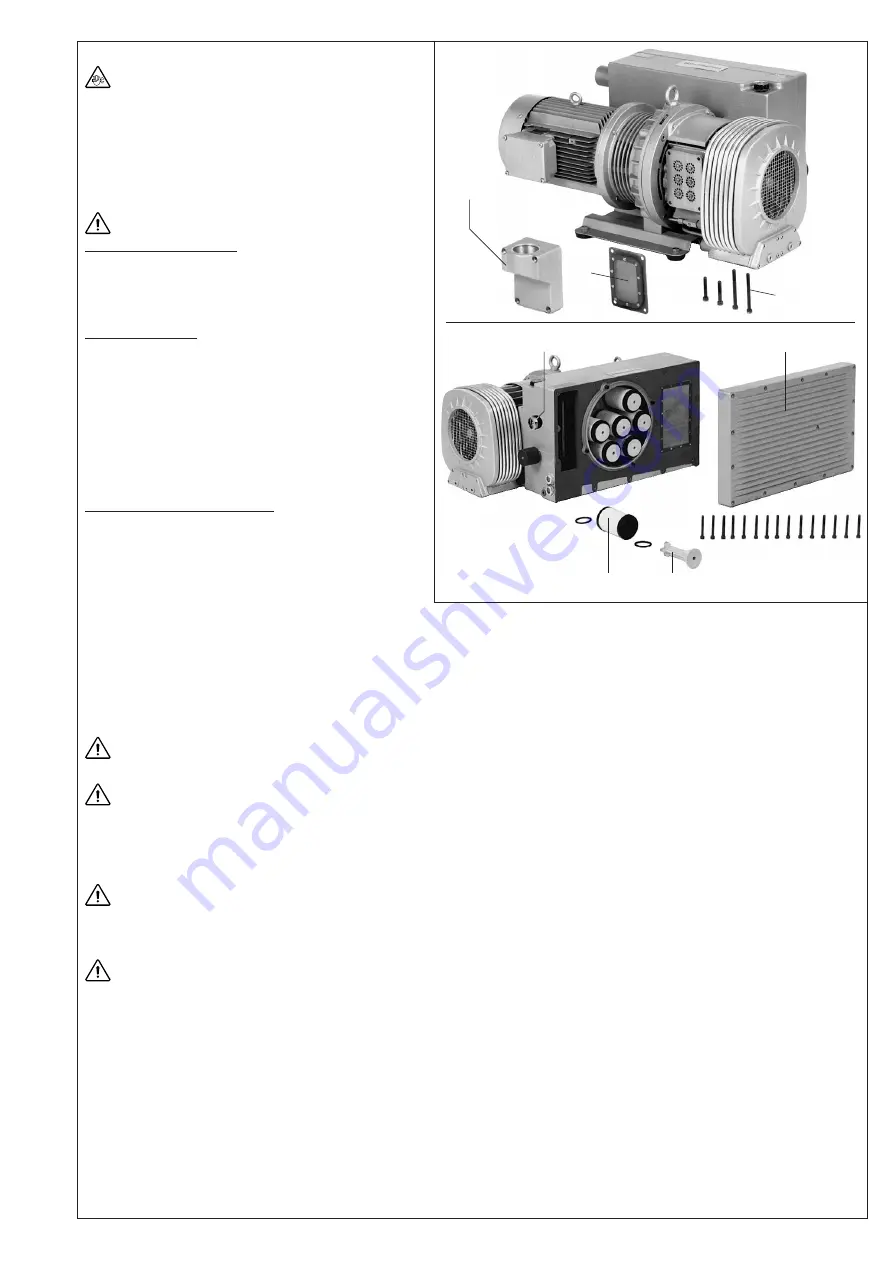
���
t
1
t
L
Y
���
D
s
1
f
1
Maintenance and Servicing
When maintaining these units and having such situa-
tions where personnel could be hurt by moving parts
or by live electrical parts the pump must be isolated by
totally disconnecting the electrical supply. It is imperative
that the unit cannot be re-started during the maintenance
operation.
Do not work on a pump that is at its normal operating
temperature as there is a danger from hot parts or hot
lubricant.
1. Air filtration
The capacity of the pump can become reduced if the
air inlet filters are not maintained correctly.
Filters on the suction side: Mesh filter (f
1
) must be cleaned
regularly depending upon the amount of contamination. Clean-
ing can be carried out by washing out or by blowing out with
compressed air. Replace filters if contaminated completely.
The mesh filter (f
1
) can be dismantled by removing screws (s
1
)
on the filter housing (D) (picture
���
).
Filter for Gas ballast: All pumps are equipped with a gas ballast
valve (U).
VCAH/VCEH 100: The built in disc (f
3
) and mesh discs (f
4
) must
be cleaned regularly depending upon the amount of contamina-
tion by blowing out with compressed air. By removing the
screw (g
1
) and plastic cap (h
1
) the filter elements can be re-
moved for cleaning. Re-assemble in reverse order (picture
���
).
VCAH/VCEH 160/250: The built in filter cartridge (f
5
) must be
cleaned regularly depending upon the amount of contamination
by blowing out with compressed air. By removing the screw (g
2
)
and plastic cap (h
2
) the filter elements can be removed for
cleaning. Re-assemble in reverse order (picture
���
).
Filter Cartridge (Optional Extras): The filter cartridge of the
vacuum tight suction filter (ZVF) or dust separator (ZFP) must
be cleaned regularly again depending upon the amount of
contamination. Cleaning can be achieved by washing or by
blowing out with compressed air. Replace the filter cartridge if
necessary. The cartridge can be removed completely by undo-
ing the relevant retaining clips.
2. Lubrication (picture
���
)
Check the oil level regularly depending upon the operating hours. First oil change after 500 operating hours (see oil drain plug (K)). Further changes
every 500 - 2000 operating hours. The oil change times should be shortened if the application is dusty. Drain the oil also from the oil cooler (R)
(see oil drain plug (K
1
)).
Only oils corresponding to DIN 51 506 group VC / VCL or a synthetic oil (obtainable from Rietschle) should be used. The viscosity must corre-
spond to ISO-VG 100 according to DIN 51 519.
The recommended Rietschle Oil types are: MULTI-LUBE 100 (mineral oil); SUPER-LUBE 100 (synthetic oil) (see oil type plate (M)).
When the oil is under a high thermal load, e.g. ambient or suction temperatures over 30°C, unfavourable cooling or operating with increased
speed etc., the oil change time can be extended by using the recommended synthetic oil.
Old and used oil must be disposed of corresponding with the relevant health, safety and environmental laws.
If the oil brand is changed, the old oil must be drained completely from oil separator housing and the oil cooler.
3. Oil separation (picture
���
)
Extremely blocked filter elements will result in an increased pump temperature and will cause discolouration of the lubricant.
The oil separator elements may become contaminated after a long period of operation which can result in high pump temperature and motor
overload. We therefore recommend to change the filter elements (L) every 2000 operating hours or when the filter back pressure is in excess of
0.7 bar (see back pressure gauge (Y)
➝
optional extra). It is not possible to clean these elements.
To change filters: Remove oil separator covers (t
1
). Remove plastic fixings (t) and exchange the elements (L). If possible re-use the o-ring for
reassembly. Re-assemble in reverse order.
When refitting the oil separator housing (size 5) check for correct orientation.
(as marked on the base on the housing)
4. Coupling (picture
���
)
The coupling rubbers (k) are wearing parts and should be checked regularly. When the coupling rubbers are worn this can be detected by a knocking
sound when the vacuum pump is started.
Defective coupling rubbers can cause extensive damage and even in some extreme cases break the rotor shaft.
To check the coupling, stop the motor (m) and isolate. Remove the screws (s
5
). Pull off the motor together with the motor side coupling half (q).
If the coupling rubbers (k) are damaged remove the circlips (l) from the coupling bolt (r) and exchange the coupling rubbers (k). Leave the spacer (p)
in place, check the coupling bolts (r) for any wear and replace if necessary. To replace remove fan cover (v
1
), remove the circlip (l
1
), pull off the
coupling and fan (v) complete from the pumpshaft, remove the nut (w) with washer (u) and exchange the coupling bolts.
Re-assemble in reverse order.