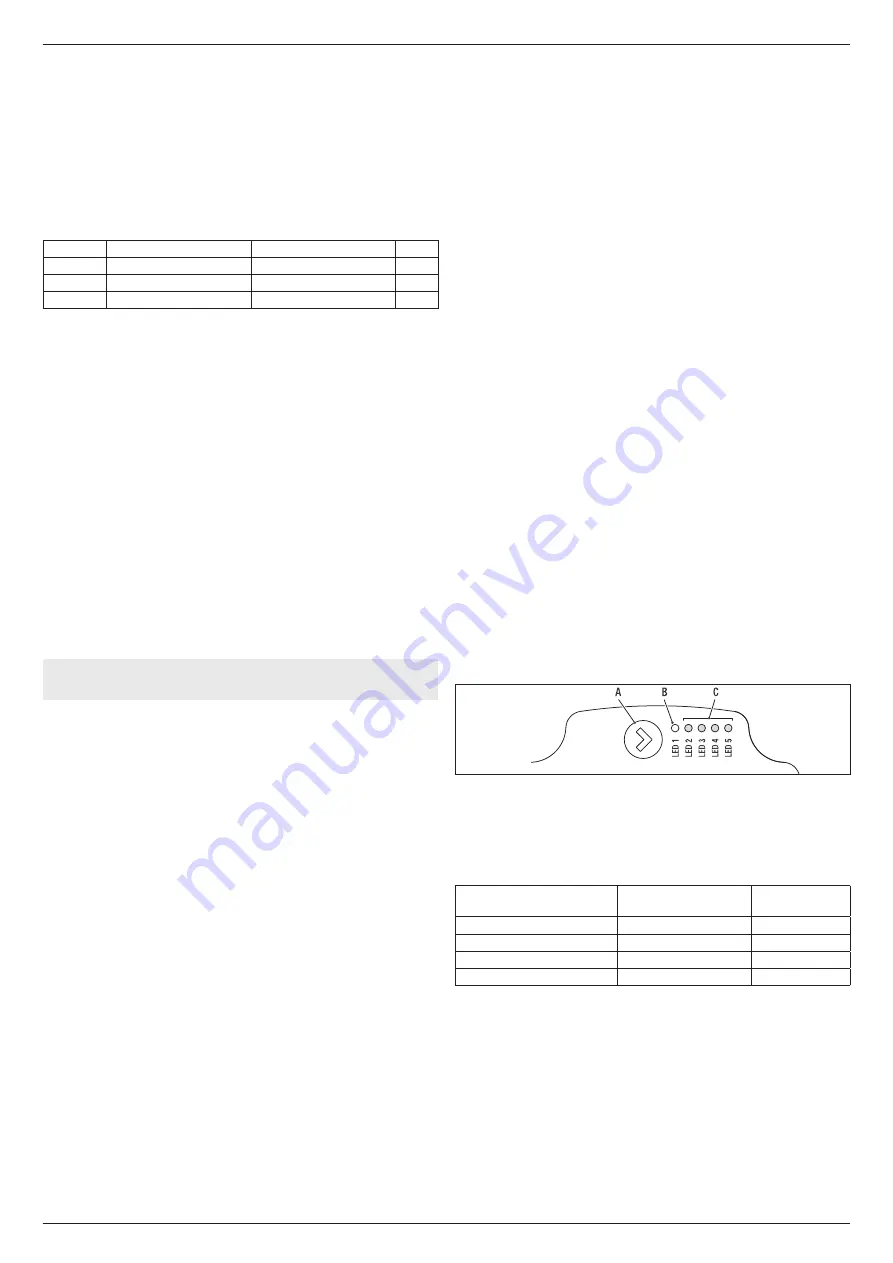
FAMILY
8
b
A data plate must be present at the connection point with the collective flue pipe. The
plate must include at least the following information:
-
the collective flue is sized for boilers C(10) type
-
the maximum permissible mass flow of the combustion products in kg/h
-
the dimensions of the connection to the common pipes
-
a warning concerning the openings for the air outlet and the entry of the combu-
stion products of the collective pressure pipe; these openings must be closed and
their tightness must be checked when the boiler is disconnected
-
the name of the manufacturer of the collective smoke pipe or its identification
symbol.
b
See applicable legislation for the discharge of the combustion products as well as
local regulations.
b
The flue gas pipe must be suitably selected based on the parameters shown below
.
maximum length
minimum length
UM
ø 60-100
4,5
0,5
m
ø 80
4,5
0,5
m
ø 80/125
4,5
0,5
m
b
The terminal of the collective pipe must generate an upward air current.
b
Before attempting any operation, disconnect the appliance from the electrical supply.
b
Before assembling, lubricate the gaskets with a non-corrosive glide lubricant.
b
The flue gases discharge pipe should be inclined, if the pipe is horizontal, by 3°
towards the boiler.
b
The number and characteristics of the exhaust ventilation devices which are the real
characteristics of the flue itself.
b
The condensation can flow inside the boiler.
b
The maximum recirculated value allowed in wind conditions is 10%.
b
The maximum permissible pressure difference (25 Pa) between the combustion
products inlet and the air outlet of a collective flue can not be exceeded when-
1 boiler work at the maximum nominal heat output and 1 boiler within minimum
temperature allowed by the checks.
b
The collective smoke pipe must be adequate for an overpressure of at least 200 Pa.
b
The collective flue must not be equipped with a wind-proofing device.
At this point it is possible to install the curves and extensions, available as accessories,
depending on the type of installation desired.
The maximum permissible lengths of the flue pipe and the air intake pipe are given in the
instruction manual of the reference device.
With C(10) installation, in any case, report the number of fan speed (rpm) on the
label placed next to the data plate.
3.15 Filling the heating system and eliminating air (Fig. 19)
Note
: even if the boiler is fitted with a semi-automatic filling device, the first filling operation
must be carried out by turning the filler tap (
B
) with the boiler OFF.
Note
: each time the boiler is powered up, the
automatic venting cycle
is carried out.
Note
: the presence of a water alarm (40, 41 or 42) does not allow the venting cycle to be
carried out. The presence of a domestic hot water request during the venting cycle interrupts
the venting cycle.
Once the hydraulic connections have been made, fill the heating system as follows:
-
Set the boiler to OFF
-
Open the plug of the air vent valve (
D
) by two or three turns to allow the continuous
bleeding of the air, and leave the valve cap (
D
) open
-
Connect the supplied silicone pipe to the de-aeration tap (
A
)
and take a bucket to collect
any water that may come out after bleeding
-
Open the de-aeration tap (
A
)
-
Turn on the filling tap
(
B
)
-
Wait until the water comes out continuously from the de-aeration tap (
A
)
, then close it
-
Wait for the pressure to increase: check that it reaches 1-1.5 bar; then close the system
filling tap (
B
).
Note
: if the mains pressure is less than 1 bar, keep the system filling tap (
B
) open during the
venting cycle and close it once it has finished.
-
To start the vent cycle shut of the electrical power for a few seconds; connect the power
again leaving the boiler OFF. Check that the gas tap is closed.
-
At the end of the cycle, if the circuit pressure has dropped, open the filling tap (
B
) again
to bring the pressure back up to recommended levels (1-1.5 bar)
The boiler is ready after the vent cycle.
-
Remove any air in the domestic system (radiators, zone manifolds, etc.) using the bleed
valves.
-
Once again check that the system pressure is correct (ideally 1-1.5 bar) and restore the
levels if necessary.
-
If air is noticed when operating, repeat the vent cycle.
-
Once the operations are finished, open the gas tap and ignite the boiler.
At this point it is possible to carry out any heat request.
3.16 Draining the heating system (Fig. 19)
Before draining, set the boiler to OFF and shut off the electrical supply setting the system's
main switch to “off”.
-
Close the heating system's taps (if present).
-
Connect a pipe to the system discharge valve (
C
), then manually loosen it to let the
water flow out.
-
Once the operations have been completed, remove the pipe from the system discharge
valve (
C
) and close it again.
3.17 Emptying the domestic hot water circuit
Whenever there is risk of frost, the domestic hot water system must be emptied in the
following way:
-
turn off the main water supply tap
-
turn on all the hot and cold water taps
-
drain the lowest points.
3.18 Condensate siphon (Fig. 19)
When the boiler is first started the siphon for collecting the condensate is empty. When
eliminating air form the siphon fills.
-
Slowly open the de-aeration tap (
A
) and leave it open until the amount of water contained
in the siphon reaches the ledge.
-
Close the de-aeration tap (
A
)
-
Check that there are no leaks from the SRD device connection zone and that the device
allows the liquid to run off correctly.
-
Check that the system pressure has not dropped below 1 bar. If necessary, fill the system.
Repeat this operation during maintenance work.
CHECK THAT THE CONDENSATE DRAIN OUTLET SIPHON CONTAINS WATER, IF IT
WAS NOT FILLED PROCEED AS DESCRIBED ABOVE.
3.19 Circulator
Circulator residual discharge head
The boilers is equipped with an already hydraulically and electrically connected circulator,
whose useful available performance is indicated in the graph.
The modulation is managed by the board through the DUTY CYCLE PUMP - access level
INSTALLER. The circulator is factory set with discharge head of 6 meters.
The boiler is equipped with an anti-blocking system which starts up an operation cycle after
every 24 hours of stop, with the mode selector in any position.
b
The "anti-locking" function is only activated when the boiler is electrically powered.
a
It is strictly forbidden to operate the circulator without water.
Where there is the need to use a different curve, the desired level can be selected on the
circulator.
The main characteristics and how to set the desired operation are described below.
3.19.1
User interface
Note:
The user interface consists of a key (
A
), a red/green LED (
B
) and four yellow LED
(
C
) set in a line.
The user interface allows to view the operating performance (operating status and alarm
status) and set the operating mode of the circulator.
The performance, indicated by LEDs (B) and (
C
) are always visible during the normal opera-
tion of the circulator, while the settings are made by pressing button (
A
).
3.19.2 Indication of the operating status
When the circulator is operating, LED (
B
) is green. The four yellow LEDs (
C
) indicate the
consumption of electric power (
P1
) as shown in the following table.
LED status
Status
CIRCULATOR
Consumption in %
of P1 MAX (*)
Green LED on +1 yellow LED on
Minimum operation
0~25
Green LED on + 2 yellow LEDs on Minimum-medium operation
25~50
Green LED on + 3 yellow LEDs on
Medium-maximum operation
50~75
Green LED on + 4 yellow LEDs on
Maximum operation
100
(*) For the output (
P1
) absorbed by the circulator, refer to that indicated in the “Technical
Data” table.