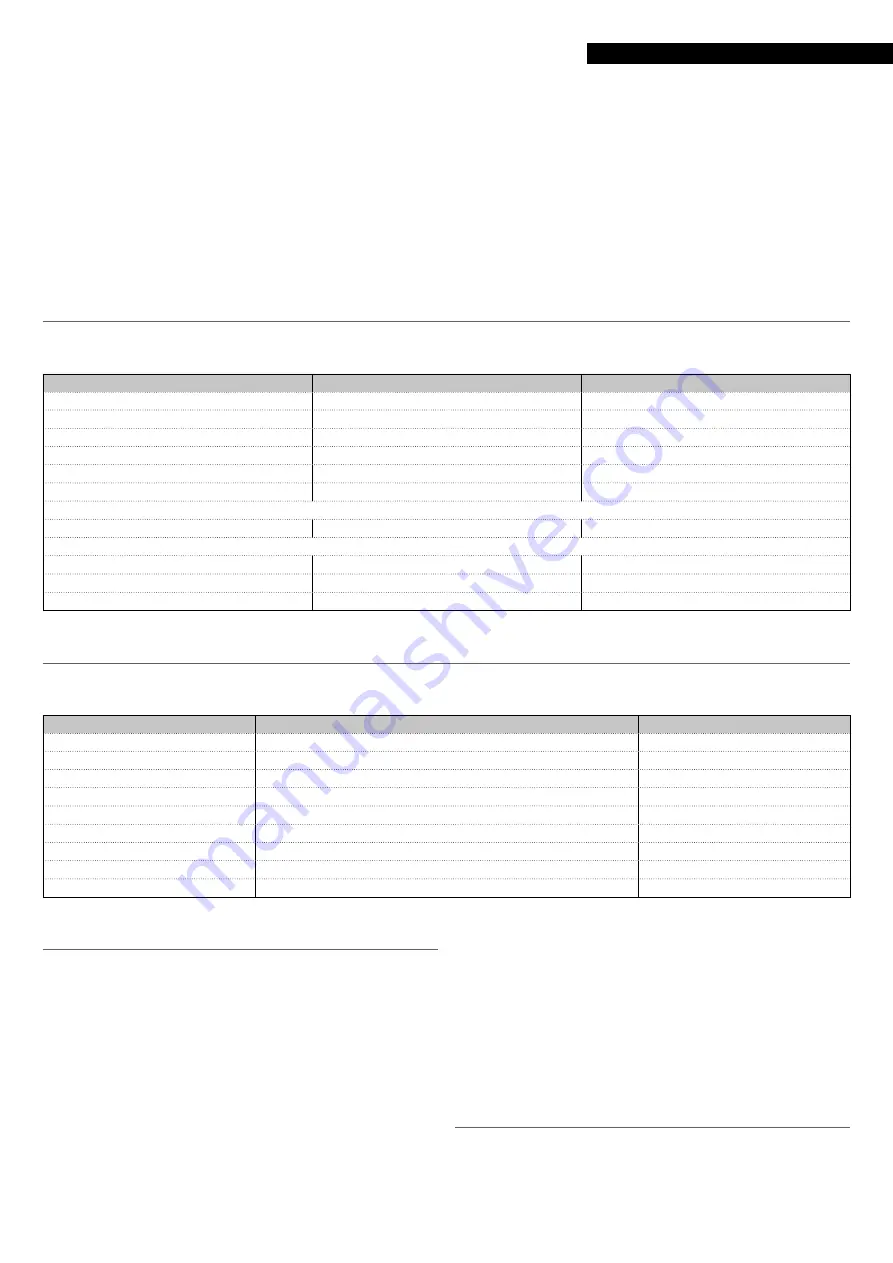
63
MAINtENANCE
—
The modification of the parameters set in the factory
(change of application)
—
Removal or disassembly of the unit
—
Any intervention due to a planned maintenance interven-
tion not carried out
—
Qualsiasi intervento coperto dalla garanzia
—
One to two leak checks per year performed with a certified
leak detector and a qualified person
To reduce waste, the refrigerant and the oil must be in compli-
ance with current legislation, using methods that limit the loss-
es of refrigerant and the pressure drops and with the materials
suitable for the products.
Detected faults and leaks must be repaired immediately.
The compressor oil that is recovered during maintenance con-
tains refrigerant and must be treated accordingly.
The coolant under pressure must not be drained in the open air.
If a refrigerant circuit is opened, plug all openings, if the oper-
ation takes up to a day; for longer periods, load the circuit with
nitrogen.
NOtA: Any deviation or non-compliance with the maintenance
criteria will void the warranty conditions of the unit and the
manufacturer can no longer be held responsible.
4.2 Tightening torque for main electrical connections
Component
Unit designation
Value (N.m)
Main switch (option 70)
L1 /L2 /L3/N/PE
2,00
Terminal X1
L1 /L2 /L3/N/PE
1,5 - 1,8
Terminal X3
0,6 - 0,8
Contactor (power and control)
1,50
Thermal relay
2,50
Transformer
1,70
Connections on the compressor
Screw on phases (only for 21kW)
2,50
Compressor speed variator
6 nuts M10
L1 /L2 /L3/N
1,20
2 nuts M10 or M8
PE
1,20
9 nuts M8 (with fuses and bars)
01/02/03
1,20
4.3 Tightening torque for main screws and nuts
Screw type
Use
Value (N.m)
Wood screw H M8
Assembly of the frame on the pallet
13,00
Nut H M8
Fixing the compressor on the base and fixing the plate exchanger and receiver
15,00
Self-tapping screw D=4,2mm
Sheet metal parts, plastic grid and electrical components
4,20
Self-tapping screw D=3mm
Mounting the deflector on the front panel
2,00
Self-tapping screw M6
Fan sub-assembly and assembly of the frame on the feet
7,00
Screw M8
Water pump unit on the partition panel
15,00
Gas nutD D1” e D1”1/4”
Inlet and outlet group of heat pump pipes
70,00
Gas nut D1/2”
Water filling system and nut assembly on the suction pipe of the water pump
20,00
Nut H M6
Fan propeller assembly on the fan motor
7,00
4.4 Air side heat exchanger
It is advisable to regularly inspect the finned coils to verify their
degree of soiling. It depends on the environment in which the
unit is installed, and will be worse in urban and industrial in-
stallations and near deciduous trees.
For cleaning the finned coil, there are two maintenance levels:
—
If the air heat exchangers are clogged, gently clean them
vertically with a brush.
—
Work on the air heat exchangers with the fan off.
—
For this type of operation, turn off the unit if, having made
all the appropriate service considerations, it is considered
appropriate.
—
Clean the air heat exchangers to ensure optimal unit op-
eration. This cleaning is necessary when the air heat ex-
changers start to get dirty. The frequency of cleaning de-
pends on the season and the location of the unit (area
exposed to the wind, forest, dusty, etc.).
Clean the finned coil with suitable products.
9
Never use pressurized water without a large diffuser. Do not
use high pressure cleaners for Cu / Cu and Cu / Al coils.
Concentrated or rotating water jets are strictly prohibited. Never
use liquid with a temperature higher than 45 ° C to clean the air
heat exchangers.
Proper and frequent cleaning (approximately every three
months) will avoid 2/3 of the corrosion problems.
4.5 Plates heat exchanger maintenance
Check that:
—
The insulating foam is intact and firmly in place.
—
the bPHE and the electric pipe heaters are in operation,
and correctly positioned securely.
Содержание 20161608
Страница 1: ...NXH 005 015 cod Doc 0096185 rev 0 05 2020 EN INSTALLATION AND TECHNICAL SERVICE INSTRUCTIONS ...
Страница 65: ......
Страница 66: ......
Страница 67: ......