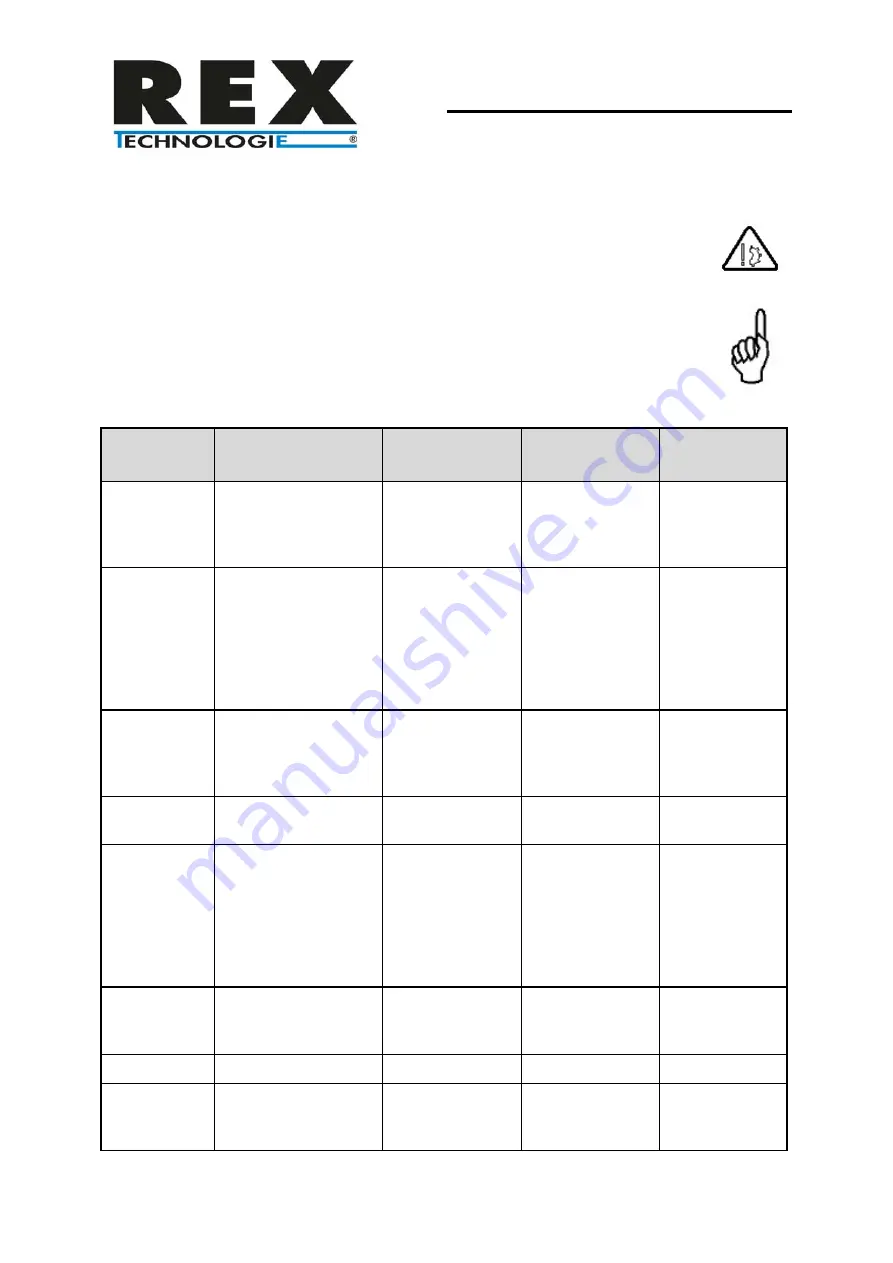
RVF 327, 327 S, 330, 330 S
ex no. 1200
Maintenance
Version 1.5
page 121 of 144
Cleaning plan applies only for the machine parts made of stainless steel
(For other material, the approval from the cleaning and disinfection agent manu-
facturer is required.)
The Vacuum filling machine must be treated, according to the cleaning plan, after
the end of every production, after a break in operation of more than 1-1, 5 hours,
but at least 1x daily.
5.2.5
Cleaning for acidic cleaning procedures
Working
steps
Cleaning agents
Cleaning meth-
ods
device/
remedy
Suggestions
Rough clean-
ing, removal
of product
remains
Water,
Max. 50-60°C
manual,
mechanical
Water hose,
scraper, spatula
Begin immedi-
ately after end
of production
Dismantle
and clean
small parts
3-6 % solution of e.g.
Henkel: P3topax 56
Goldschmidt: SOM-
PLEX acid foam
First a basic pre-
rinsing with water
max. 60°C, then
allow to foam, or
apply manually,
effective time
15min
High pressure
cleaning, low
pressure foaming
machine, spray
gun or brush for
removal of calci-
um deposits
Attention! For
parts not made
of stainless
metal: follow
instructions of
the manufac-
turer exactly!
Final rinse
Water of drinking
quality ~60°C
Low pressure
<30bar manual
Low pressure
cleaning ma-
chine, water
hose
Check for
cleanliness
visual
As needed after
cleaning
Disinfecting
0,5-2 % solution of
Henkel: P3-topax 99
Henkel: P3-topax 91
Goldschmidt:
TEGO 2000
TEGO IMC
Spray, foam,
effective time
according to
product data
sheet
High pressure
cleaner, low
pressure device,
spray gun
Tot. Vacuum
filling machine
and small parts
(after finishing
all the cleaning
procedures in
the room)
Clear rinse
Drinking water
Low pressure
<30 bar, manual
Low pressure
device, spray
pistol, hose
Follow acc. to
LMBG §31
drying
care
z. B. wheat oil
Spray/ rub in
Spray gun
Conveyor ma-
chine.-outer
area