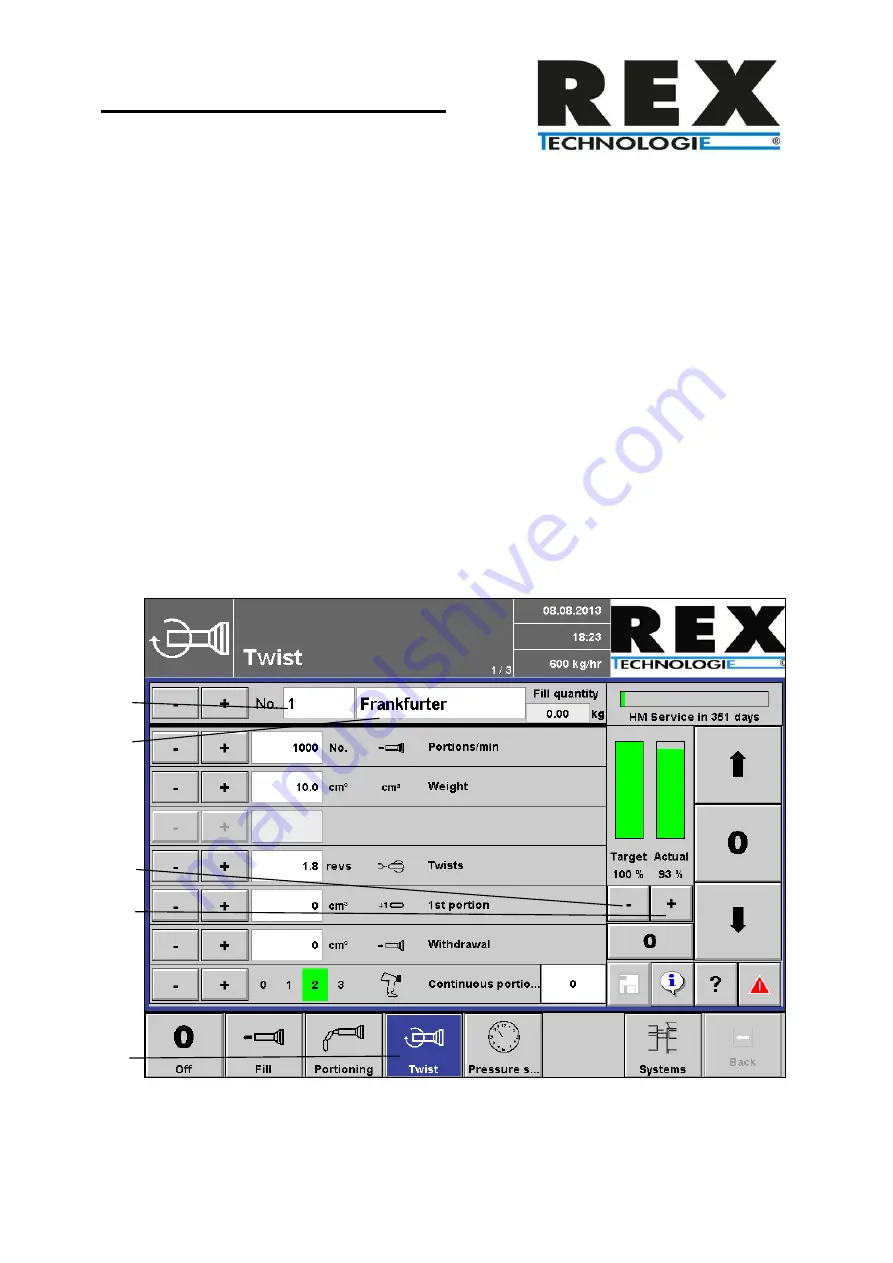
RVF 327, 327 S, 330, 330 S
ex no. 1200
Operation of the vacuum filling
machine
page 66 of 144
Version 1.5
4.8
ADJUSTMENT OF A TWISTING OFF PROGRAM
1. Press key (23) in the operational performance type
2. Select program area (31)
3. type in name of sausage (32)
4. adjust desired vacuum pressure (13, 14)
5. The following amounts can be selected with the help of the respective key:
-
speed
-
filling weight
-
twisting off number
-
1. additional portions
-
withdrawal
-
Knee lever positioning for single portions (34), continuous portioning (35) or piece
ordering
31
32
14
13
23
Figure 22: mask twisting off