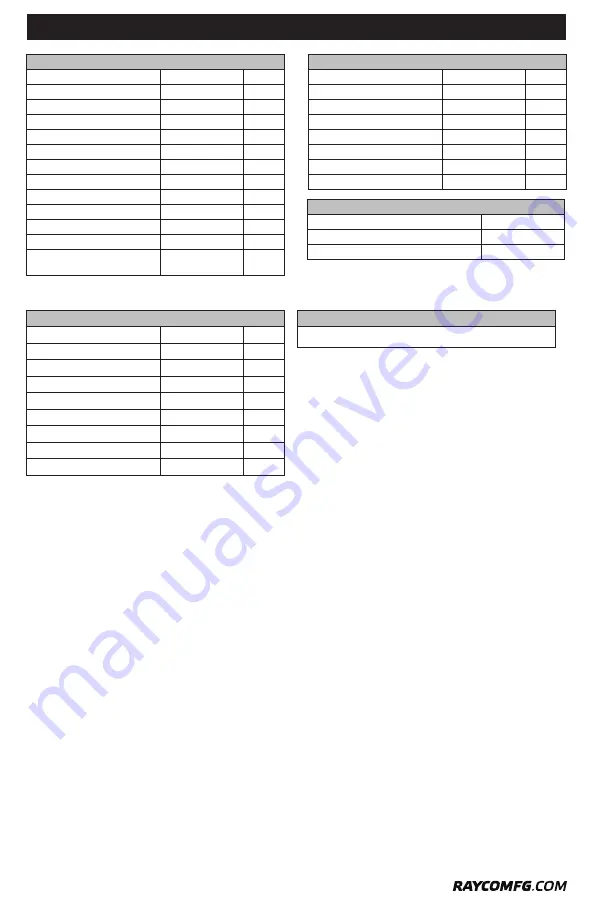
SERVICE PARTS - SAFETY SALES KIT
98
SERVICE FILTERS
DESCRIPTION
PART #
Qty.
Hydraulic Charge Pressure
762462
2
Fresh Air Filter
762823
1
Cutter High Pressure Filter
764726
1
Return Hydraulic Filter
800710
1
Hydraulic Fill Filter
761038
1
Engine Oil Filter
806182
1
Fuel Filter
806183
1
Fuel/Water Separator
806184
1
Main Air filter
806185
1
Secondary Air Filter
806186
1
Foam Cab Filter
806306
1
Hydraulic Vent Filter
(Located on Limb riser)
1200022
1
TRACK ASSEMBLY PARTS
DESCRIPTION
PART#
Qty.
Front Idler
803148
2
Idler Spring and Piston RH
803149
1
Idler Spring and Piston LH
803183
1
Bottom Roller 2 Flange
803150
2
Bottom Roller 3 Flange
803514
10
Track
804437
2
Sprocket
39576
2
MANUALS
Parts
PMC120R-19
Operator Service Maintenance
OSMC120R-19
Operator Booklet
OBC120R-19
COMMON WEAR AND REPLACEMENT PARTS
DESCRIPTION
PART#
Qty
Door Key
762015
1
Ignition Key
801208
1
Ignition Switch
805980
1
Fuel Cap
804467
1
Coolant Cap
806559
1
DEF Cap
806560
1
Fan /AC Belt
806050
1
O-Ring Kit
800186
1
FILTER SERVICE KIT 40161
KIT INCLUDES FILTERS IN THE “FILTER SERVICE” SECTION
LESS HYDRAULIC VENT FILTER
Содержание C120R
Страница 57: ...C120R Operator Service Maintenance Manual 800 392 2686 57 Maintenance ...
Страница 65: ...C120R Operator Service Maintenance Manual 800 392 2686 65 Troubleshoot Use ULSD Diesel Only ...
Страница 70: ...C120R Operator Service Maintenance Manual 70 A C Schematic 39965 Rev A ...
Страница 71: ...C120R Operator Service Maintenance Manual 800 392 2686 71 A C Schematic 39965 Rev A ...
Страница 72: ...C120R Operator Service Maintenance Manual 72 Hydraulic Hose Schematic 806134 Rev E ...
Страница 73: ...C120R Operator Service Maintenance Manual 800 392 2686 73 Hydraulic Hose Schematic 806134 Rev E ...