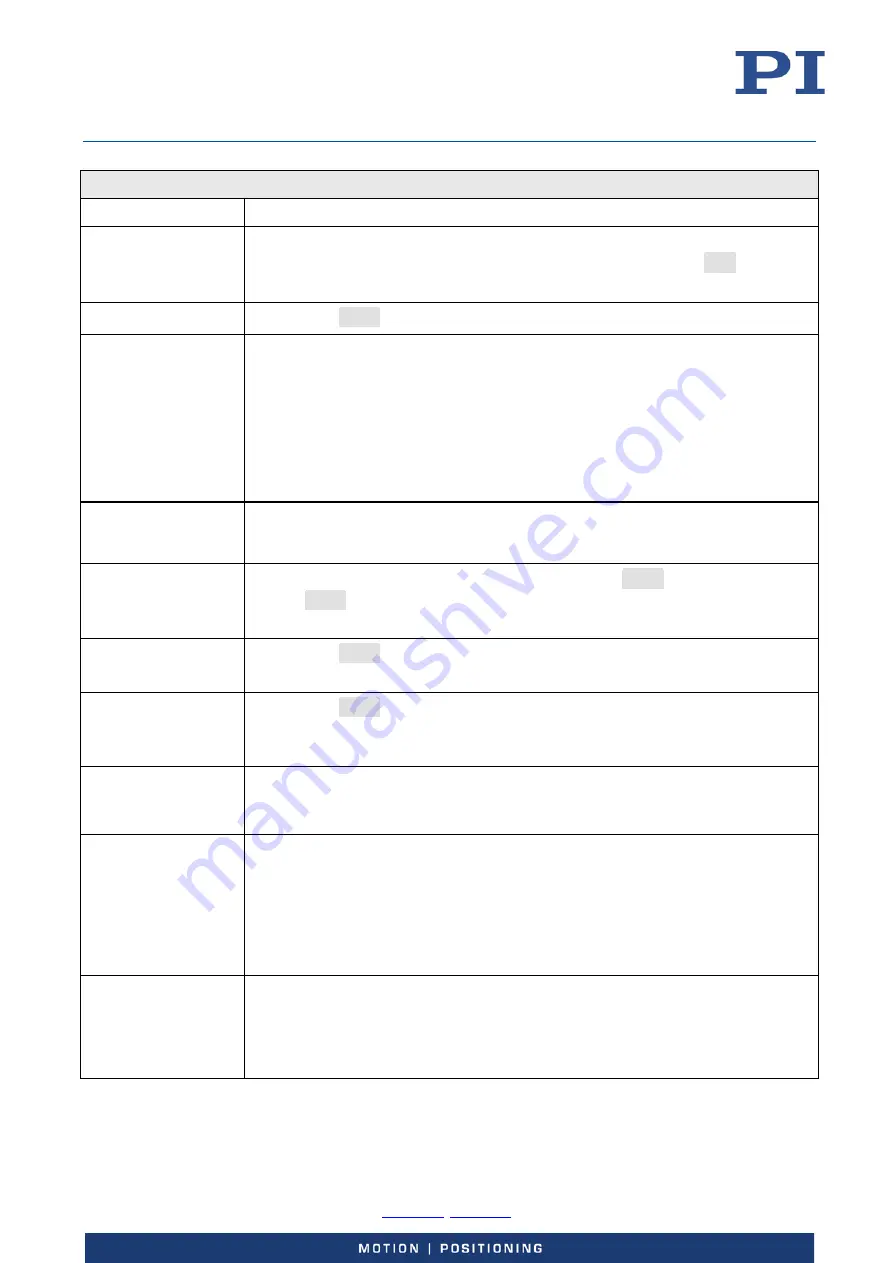
User Manual
E727T0005, valid for E-727
BRO, 2019-06-28
Physik Instrumente (PI) GmbH & Co. KG, Auf der Roemerstrasse 1, 76228 Karlsruhe, Germany
Page 214 / 240
Phone +49 721 4846-0, Fax +49 721 4846-1019, Email
Fault: Stage does not move
Possible Causes
Solution
The stage has been
connected to the
switched-on E-727
The ID chip of the stage has not been read out.
Switch the E-727 off and on again, or reboot the E-727 with the
RBT
command
or with the corresponding functions of the PC software.
E-727 is defective
Send the
ERR?
command and check the error code this returns.
Stage or stage cable is
defective
If available, replace the defective stage with a different stage of the same type
and test the new combination (only possible with stages which are equipped
with ID-chips).
Prevent damage to the stage as follows:
Prevent the stage from exceeding the maximally permissible operating
frequency, e.g. by using suitable waveforms with the wave generator output.
Prevent the stage from oscillating by suitably setting the control parameters.
High-voltage output of
the E-727 is deactiva-
ted due to overheating
Overheating of the E-727
See “Overtemp Protection” (p. 39) for possible measures.
Incorrect configuration
Check the parameter settings of the E-727 with the
SPA?
(volatile memory)
and
SEP?
(nonvolatile memory) commands or in the
Device Parameter
Configuration
window of PIMikroMove.
Incorrect command or
incorrect syntax
Send the
ERR?
command and check the error code this returns.
Make sure that the used motion commands match the operating mode (p. 30).
Motion commands or
wave generator
output are ignored.
Send the
ERR?
command and check the error code this returns.
Observe that only one control source can be used at a time; see "Control Value
Generation" (p. 30).
Incorrect axis
commanded
An axis identifier is even required in commands on systems with only one axis.
Make sure that the correct axis identifier (p. 22) is used and that the
commanded axis belongs to the correct stage.
In the case of analog
control, there is no
connection between
the axis and the
analog input.
When the analog input is used as control source and the axis motion is stopped with
STP or #24, the behaviour depends on the value of the
Disconnect Analog Target
Input When Stopping
parameter (ID 0x0E001E00): 1 = the analog input channel is
disconnected from the axis; 0 = the analog input channel remains connected to the
axis.
If necessary: Reconnect the corresponding input signal channel to the axis.
Further information see "Using the Analog Input" (p. 85).
Sensor zero point is
not set correctly
Changes in temperature or changes in the mechanical load can cause small
deviations of the sensor zero point. When the sensor zero point is not set correctly,
the complete output voltage range of the amplifier cannot be used in closed-loop
operation.
Start an AutoZero procedure (p. 62).