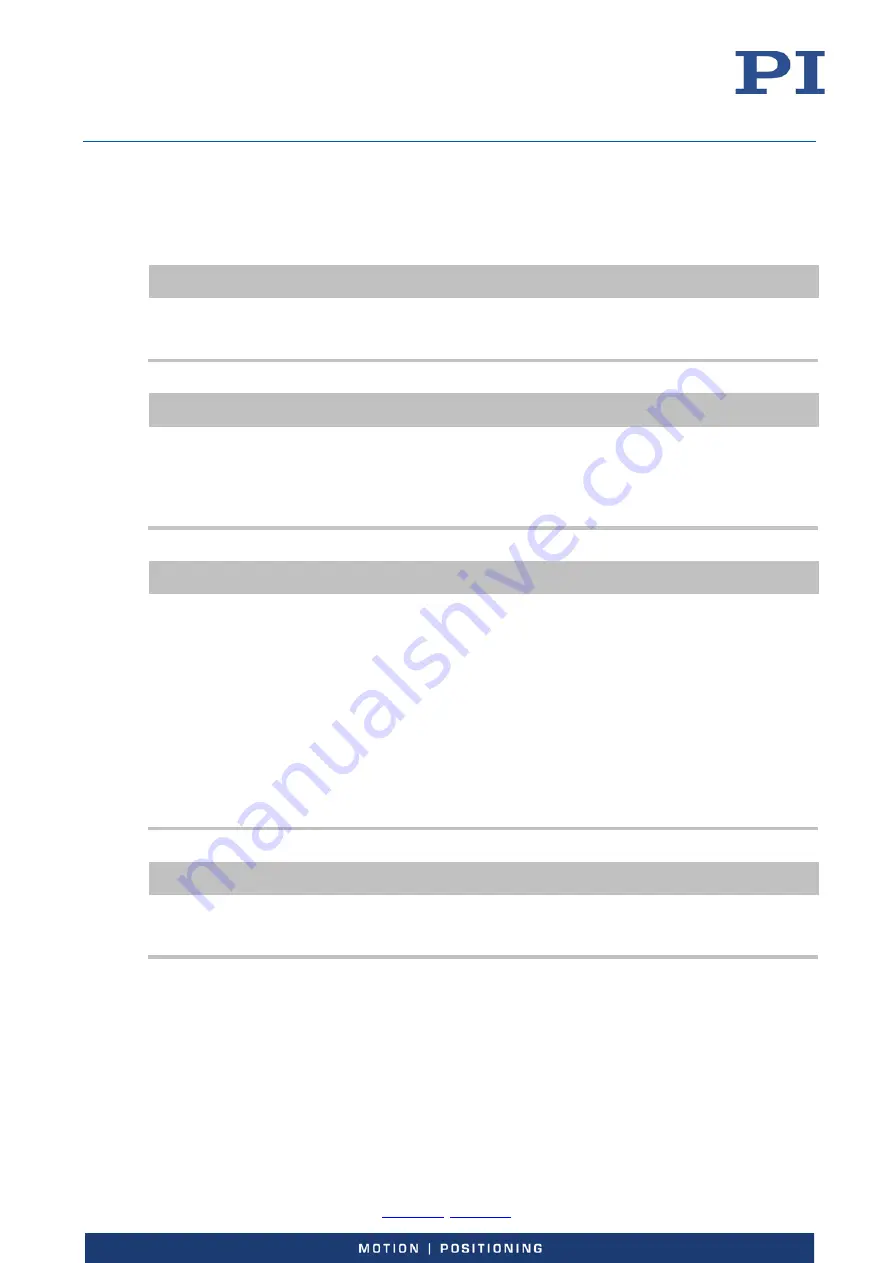
User Manual
E727T0005, valid for E-727
BRO, 2019-06-28
Physik Instrumente (PI) GmbH & Co. KG, Auf der Roemerstrasse 1, 76228 Karlsruhe, Germany
Page 176 / 240
Phone +49 721 4846-0, Fax +49 721 4846-1019, Email
For further details, see the description of the Profile position mode in the IEC 61800-7-201
standard.
When the EtherCAT communication is interrupted, any motion is stopped.
INFORMATION
The units of the position and velocity values are set via the
FieldbusAxis Resolution
parameter (ID
0x10000800) of the E-727 and the scaling factor numerator of the EtherCAT master. The values
must be identical. For further details, see p. 165.
INFORMATION
For each axis, the E-727 provides an input buffer for value sets consisting of target position (object
0x607A) and profile velocity (object 0x6081). Maximum size of the input buffer: 10 value sets.
The maximum buffer size of the E-727 is given by the
Fieldbus Set-Point List Size
parameter (ID
0x10000801). You can read this parameter via the TCP/IP or USB interface only; for details, see
“Parameters” (p. 185)
INFORMATION
Bit 10 of the status word indicates if the target position is reached. The value of bit 10 is
influenced by two parameters of the E-727: settling window (
On Target Tolerance
, ID
0x07000900) and settling time (
Settling Time
, ID 0x07000901). Bit 10 has the value 1 (“Target
position reached”) when the current position is inside the settling window and stays there for at
least the settling time. The settling window is centered around the target position.
Settling window and settling time are also applied if a set of target positions is specified. The next
target position is activated not until the previous target position has been reached accordingly.
The value of bit 10 of the status word corresponds to the on-target status flag of the E-727 which
can be output by a digital output line ("On Target" trigger mode, p. 72) or read by the ONT?
command via TCP/IP or USB.
You can read or adjust the values of the settling window and settling time parameters via the
TCP/IP or USB interface. For details, see “Parameters” (p. 185).
INFORMATION
Optimization of digital filter settings (p. 27) and tuning of the servo parameters (p. 134) can
improve the settling behaviour and reduce position noise of the axes. Optimization must be done
via the TCP/IP or USB interface.