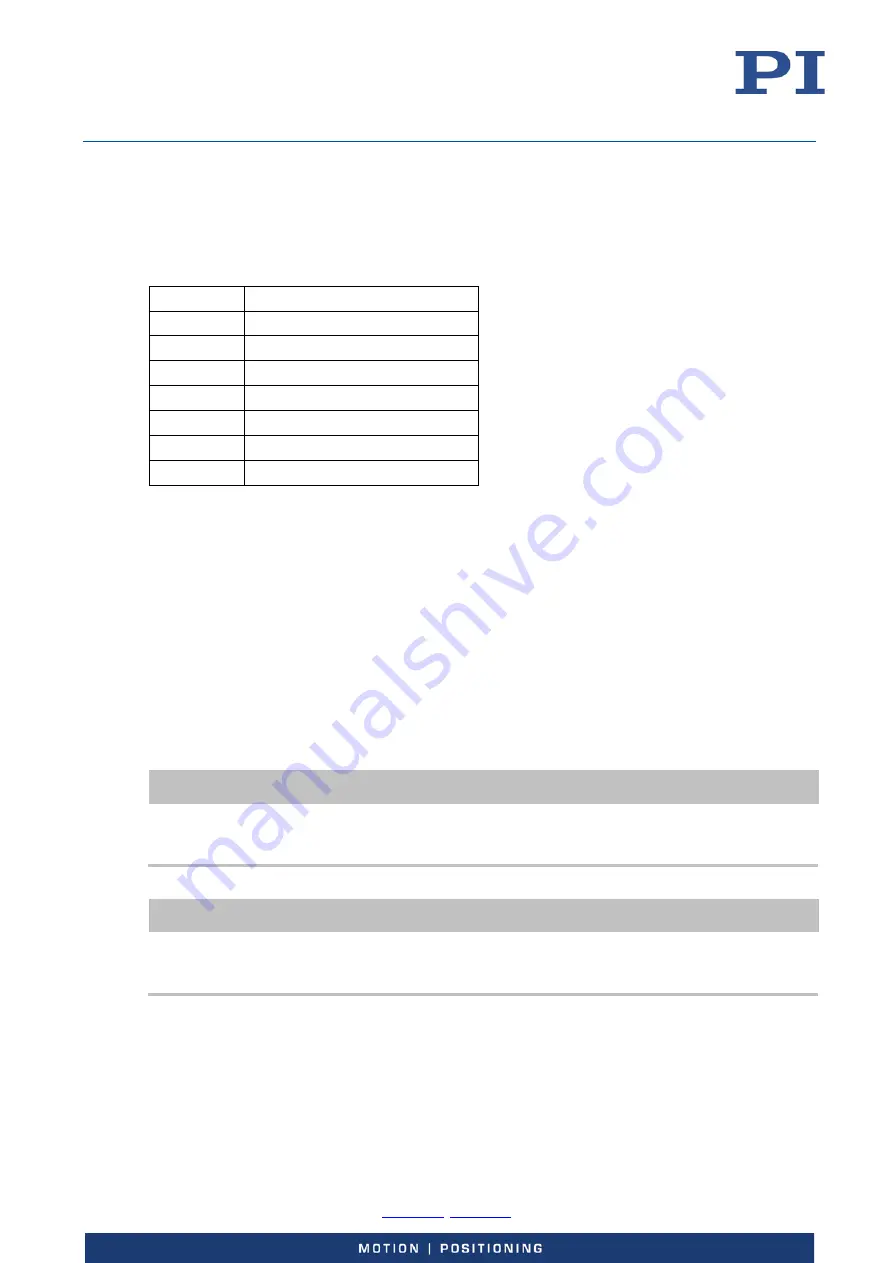
User Manual
E727T0005, valid for E-727
BRO, 2019-06-28
Physik Instrumente (PI) GmbH & Co. KG, Auf der Roemerstrasse 1, 76228 Karlsruhe, Germany
Page 177 / 240
Phone +49 721 4846-0, Fax +49 721 4846-1019, Email
Cyclic Synchronous Position Mode
In Cyclic Synchronous Position mode (CSP), the dynamics profile is calculated by the EtherCAT
master.
Supported objects (per axis):
Index*
Name
0x6040
Control word
0x6041
Status word
0x6064
Position actual value
0x607A
Target position
0x6060
Modes of operation
0x6061
Modes of operation display
0x60F4
Following error actual value
* Index for the first axis. Note that the object index is shifted by 0x800 per axis, e.g. the index of
the status word for the second axis is 0x6841.
The operation-mode-specific bits 4 to 6 and bit 8 of the control word are ignored in CSP.
The following error actual value (object 0x60F4) is calculated by the E-727 as the difference of
target and actual position.
In CSP the new target position is given cyclically by the EtherCAT master. Bit 10 of the status word
is therefore used as status-toggle information to indicate if the EtherCAT master provides updated
input data. The bit is toggled between 0 and 1 with every update of the input process data.
Bit 12 of the status word in CSP is set if the axis is in the
Operation enabled
state and follows the
target values of the EtherCAT master. In all other cases it is 0 (= target position ignored).
Bit 13 of the status word is always 0.
INFORMATION
The unit of the position values is set via the
FieldbusAxis Resolution
parameter (ID 0x10000800)
of the E-727 and the scaling factor numerator of the EtherCAT master. The values must be
identical. For further details, see p. 165.
INFORMATION
Optimization of digital filter settings (p. 27) and tuning of the servo parameters (p. 134) can
improve the settling behaviour and reduce position noise of the axes. Optimization must be done
via the TCP/IP or USB interface.