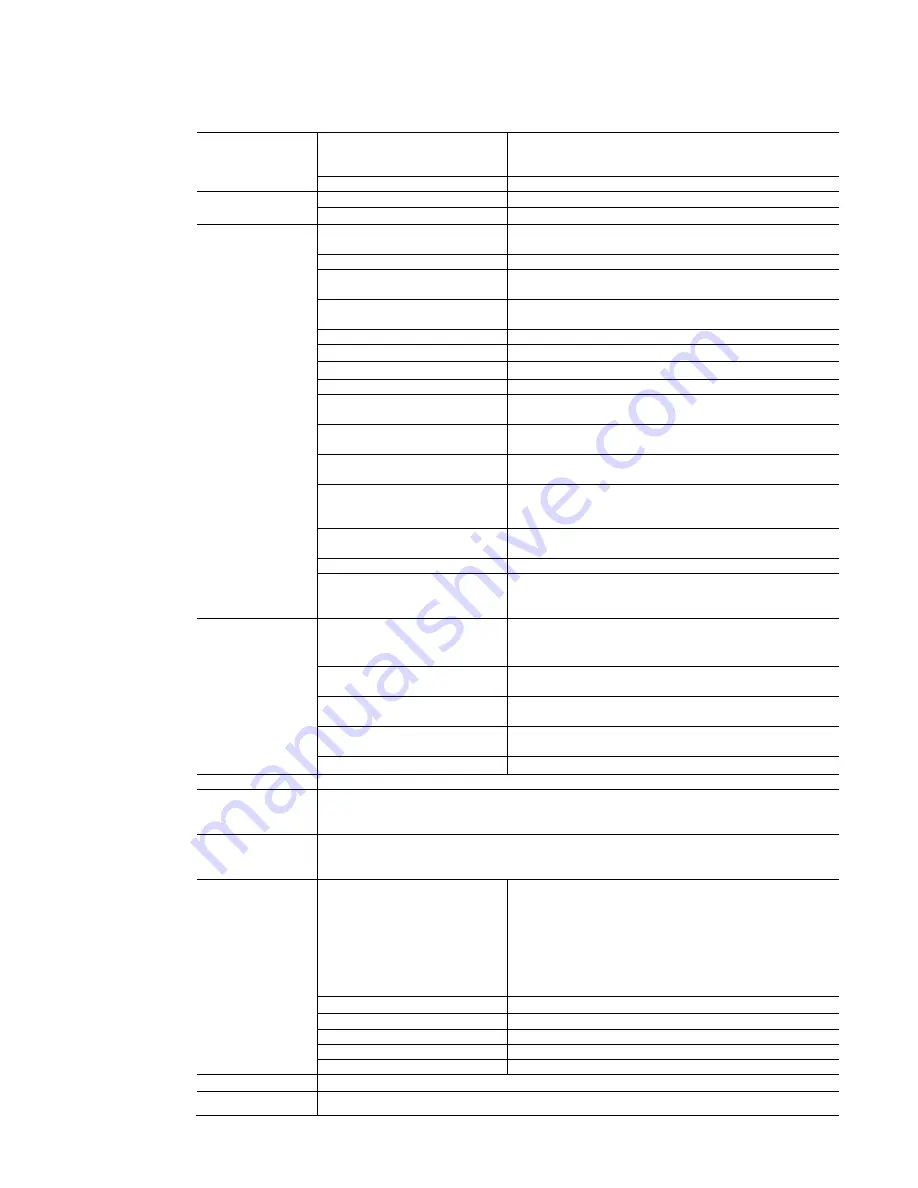
2-2
Product Overview
AC10 Inverter
2.2 Control Features
Table 2-1 Technical Specification for AC10 series IP66 Inverters
Input
Rated Voltage Range
3-phase 380-480V (+10%, -15%)
1-phase 220-240V ±15%
3-phase 220-240V ±15%
Rated Frequency
50/60Hz
Output
Rated Voltage Range
3-phase 0-INPUT (V)
Frequency Range
0.50
~
590.0Hz
Control Mode
Carrier Frequency
2000~10000Hz; Fixed carrier-wave and random carrier-wave
can be selected by F159.
Input Frequency Resolution
Digital setting: 0.01Hz, analog setting: max frequency
×
0.1%
Control Mode
SensorlessVector Control (open-loop vector control), V/F
control, PMSM sensorless vector control
Start Torque
0.5 Hz / 150% (SVC)
5% of rated speed / 100% of rated
torque (PMSM)
Speed-control Scope
1:100 (SVC), 1:20 (PMSM)
Steady Speed Precision
±0.5%
(
SVC
)
Torque Control Precision
±5%
(
SVC
)
Overload Capacity
150% rated current, 60 seconds.
Torque Elevating
Auto torque promotion, manual torque promotion
includes 1-20 curves.
V/F Curve
3 kinds of modes: beeline type, square type and
under-defined V/F curve.
DC Braking
DC braking frequency: 0.2-50.00 Hz, braking time:
0.00~30.00s
Jogging Control
Jogging frequency range: min frequency~ max
frequency, jogging acceleration/deceleration time:
0.1~3000.0s
Auto Circulating Running and
multi-stage speed running
Auto circulating running or terminals control can realize
15-stage speed running.
Built-in PID adjusting
Easy to realize a system for process closed-loop control
Auto voltage regulation (AVR)
When source voltage changes, the modulation rate can
be adjusted automatically, so that the output voltage is
unchanged.
Operation
Function
Frequency Setting
Potentiometer or external analog signal (0
~
5V, 0
~
10V,
0
~
20mA); keypad (terminal)▲
/
▼ keys, external
control logic and automatic circulation setting.
Start/Stop Control
Terminal control, keypad control or communication
control.
Running Command Channels
3 kinds of channels from keypad panel, control terminal
and MODBUS.
Frequency Source
Frequency sources: given digit, given analog voltage,
given analog current and given MODBUS.
Auxiliary frequency Source
7 options
Optional
Built-in EMC filter, built-in braking unit, Modbus, tele-control panel
Protection
Function
Input phase loss, Output phase loss, input under-voltage, DC over-voltage, over-current,
inverter over-load, motor over-load, current stall, over-heat, external disturbance,
under-load, pressure control, analog line disconnected.
MMI
Display
Output frequency, rotate-speed (rpm), output current, output voltage, DC bus voltage, PID
feedback value, PID setting value, linear-velocity, types of faults, and parameters for the
system and operation; LED indicators showing the current working status of inverter.
Environment
Conditions
Equipment Location
In an indoor location with harse conditions, prevent dust
of other things from entering the inverter. Completely
protected against jets of water and heavy waves.
Meeting EN60529 standard.
For outdoor applications the drive should be installed
under a suitable cover to provide protection against
potential damage caused by direct exposure to sun, ice
and snow.
Environment Temperature
-10
o
C
~
+40
o
C
Environment Humidity
Below 95% (non condensing)
Vibration Strength
Below 0.5g (acceleration)
Height above sea level
1000m or below (3000m with derating)
Environment
3C3 conformance
Protection level
IP66
Applicable Motor
0.4
~
15kW
TC-Hydraulik - R
ü
sdorfer Str. 8 - 25746 Heide - Lars Lornsen - T: +49 481 909 - 34 - [email protected] - www.tc-hydraulik.de