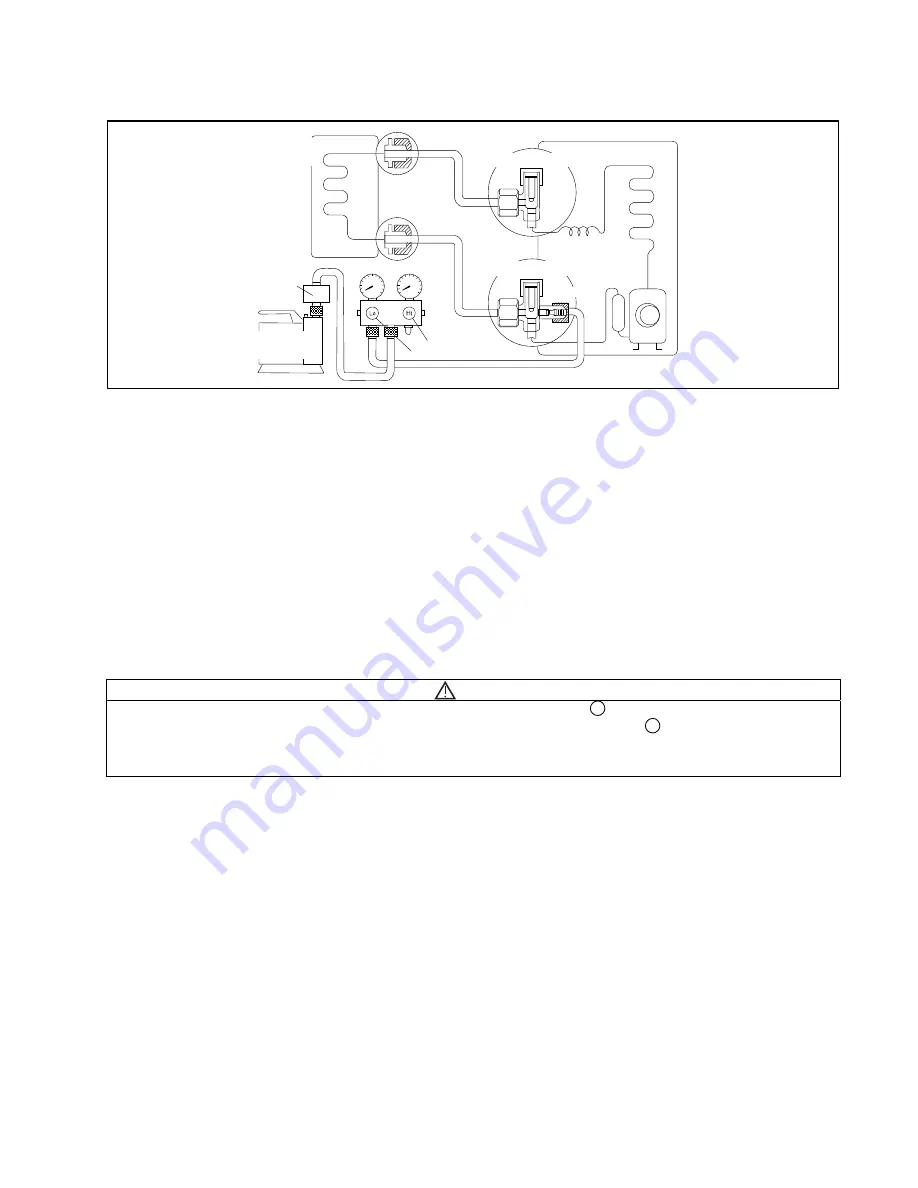
93
11.5.4 Evacuation Of The Equipment
WHEN INSTALLING AN AIR-TO-WATER HEAT PUMP, BE SURE TO EVACUATE THE AIR INSIDE THE UNIT
AND PIPES in the following procedure.
Vacuum
pump
adaptor
Vacuum
pump
OPEN
CLOSE
Close
Gas side
Liquid side
Outdoor unit
Three-way valve
Two-way valve
Close
Indoor unit
1 Connect a charging hose with a push pin to the Low side of a charging set and the service port of the 3-way
valve.
Be sure to connect the end of the charging hose with the push pin to the service port.
2 Connect the center hose of the charging set to a vacuum pump with check valve, or vacuum pump and
vacuum pump adaptor.
3 Turn on the power switch of the vacuum pump and make sure that the needle in the gauge moves from
0 cmHg (0 MPa) to –76 cmHg (–0.1 MPa). Then evacuate the air approximately ten minutes.
4 Close the Low side valve of the charging set and turn off the vacuum pump. Make sure that the needle in the
gauge does not move after approximately five minutes.
Note: BE SURE TO FOLLOW THIS PROCEDURE IN ORDER TO AVOID REFRIGERANT GAS LEAKAGE.
5 Disconnect the charging hose from the vacuum pump and from the service port of the 3-way valve.
6 Tighten the service port caps of the 3-way valve at a torque of 18 N•m with a torque wrench.
7 Remove the valve caps of both of the 2-way valve and 3-way valve. Position both of the valves to “OPEN”
using a hexagonal wrench (4 mm).
8 Mount valve caps onto the 2-way valve and the 3-way valve.
Be sure to check for gas leakage.
CAUTION
If gauge needle does not move from 0 cmHg (0 MPa) to –76 cmHg (–0.1 MPa), in step 3 above take the following measure:
If the leak stops when the piping connections are tightened further, continue working from step 3 .
If the leak does not stop when the connections are retightened, repair the location of leak.
Do not release refrigerant during piping work for installation and reinstallation. Take care of the liquid refrigerant, it may cause
frostbite.
11.5.4.1 Air-Tightness Test on the Refrigerating System
Before system charged with refrigerant and before the refrigerating system in put into operation, below site test
procedure and acceptance criteria shall be verified by the certified technicians, and/or the installer:-
Step 1: Pressure test for refrigerant leak detection:
1. Steps for pressure test, in accordance to ISO 5149.
2. Evacuate the system from refrigerant before the leak test, attach the gauge manifold set correctly and tightly.
Charging hose of Low side connect to Gas side. (Charging hose of High side connect to Liquid side if applicable.)
3. Adjust the knob on the service valves, and regulator on the gauge set, so that test gas can be inserted through
the centre manifold of the gauge set.
4. Insert Nitrogen gas into the system through the centre manifold and wait until the pressure within the system to
reach about 1MPa (10 BarG) wait for a few hours and monitor the pressure reading on the gauges.
5. Please note that the system’s pressure may rise slightly if the test is carried out on mid day, due to temperature
rise. The inverse may happen when there is temperature drop at night. However, this variation will be minimal.
6. Waiting time depends on the size of the system. Larger systems may require 12 hours of waiting time. Leak
detection within smaller system can be achieved in 4 hours.
7. Check if there is a constant pressure drop. Move to next step “Step 2: Refrigerant leak detection...” if there is any
pressure drop. Otherwise, release the Nitrogen gas and, move to “Step 3: Vacuum test”.