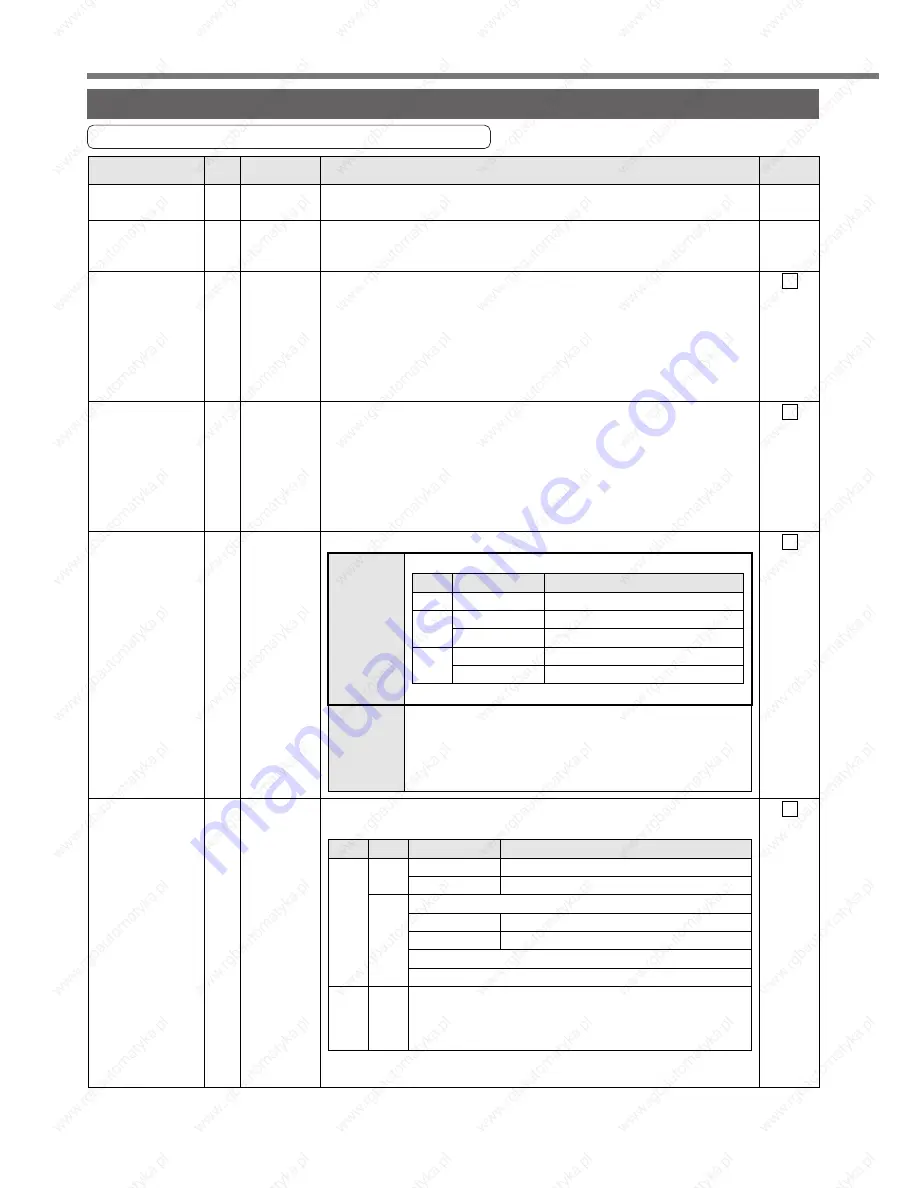
164
Input Signal and Pin No. of the Connector, CN X5
Input Signals (common) and Their Functions
Wiring to the connector, CN X5
Title of signal
Pin No.
Symbol
Function
I/F circuit
Power supply for
control signal (+)
7
–
COM+
• C of the external DC power supply (12 to 24V).
• Use the power supply voltage of 12V
±
5% – 24V
±
5%
Power supply for
control signal (-)
41
–
COM–
• Connect – of the external DC power supply (12 to 24V).
• The power capacity varies depending on a composition of I/O circuit. 0.5A
or more is recommended.
CW over-travel
inhibit input
8
SI
P.162
CWL
• Use this input to inhibit a CW over-travel (CWL).
• Connect this so as to make the connection to COM– open when the
moving portion of the machine over-travels the movable range toward CW.
• CWL input will be invalidated when you set up Pr04 (Setup of over-travel
inhibit input) to 1.Default is "Invalid (1)".
• You can select the action when the CWL input is validated with the setup
of up Pr66 (Sequence at over-travel inhibit). Default is "Emergency stop
with dynamic brake".(Pr66=0)
CCW over-travel
inhibit input
9
SI
P.162
CCWL
• Use this input to inhibit a CCW over-travel (CCWL).
• Connect this so as to make the connection to COM- open when the moving
portion of the machine over-travels the movable range toward CCW.
• CWL input will be invalidated when you set up Pr04 (Setup of over-travel
inhibit input) to 1.Default is "Invalid (1)".
• You can select the action when the CCWL input is validated with the setup
of Pr66 (Sequence at over-travel inhibit). Default is "Emergency stop with
dynamic brake".(Pr66=0)
Speed zero clamp
input
26
SI
P.162
ZEROSPD
• Function varies depending on the control mode.
• Becomes to a speed-zero clamp input (ZEROSPD).
• In case Pr06 is 2 at torque control, ZERPSPD is invalid.
• Becomes to an input of damping control switching (VS-SEL).
• While Pr24 (Damping filter switching selection) is 1, the
1st damping filter (Pr2B, Pr2C) will be validated when you
open this input, and the 2nd damping filter (Pr2D, Pr2E)
will be validated when you connect this input to COM–.
Pr06
0
1
2
Connection to COM–
–
open
close
open
close
Content
ZEROSPD input is invalid.
Speed command is 0
Normal action
Speed command is to CCW
Speed command is to CW.
Velocity/
Torque
control
Position/
Full-closed
control
Gain switching
input
or
Torque limit
switching input
27
SI
P.162
GAIN
TL-SEL
• Function varies depending on the setups of Pr30 (2nd gain setup) and
Pr03 (Selection of torque limit).
• For details of 2nd gain switching function, refer to P.243 "Gain Switching
Function" of Adjustment.
invalid
• Input of torque limit switching (TL-SEL)
• Pr5E (Setup of 1st torque limit) will be validated when you
open this input, and Pr5F (Setup of 2nd torque limit) will
be validated when you connect this input to COM–.
Pr30
0
1
–
Pr03
0 – 2
3
Connection to COM–
open
close
open
close
Content
Velocity loop : PI (Proportion/Integration) action
Velocity loop : P (Proportion) action
1st gain selection (Pr10,11,12,13 and 14)
2nd gain selection (Pr18,19,1A,1B and 1C)
when the setups of Pr31 and Pr36 are 2
when the setups of Pr31 and Pr36 are other than 2
Содержание Minas A4 Series
Страница 307: ...305 Supplement Supplement MEMO ...
Страница 364: ...362 MEMO ...