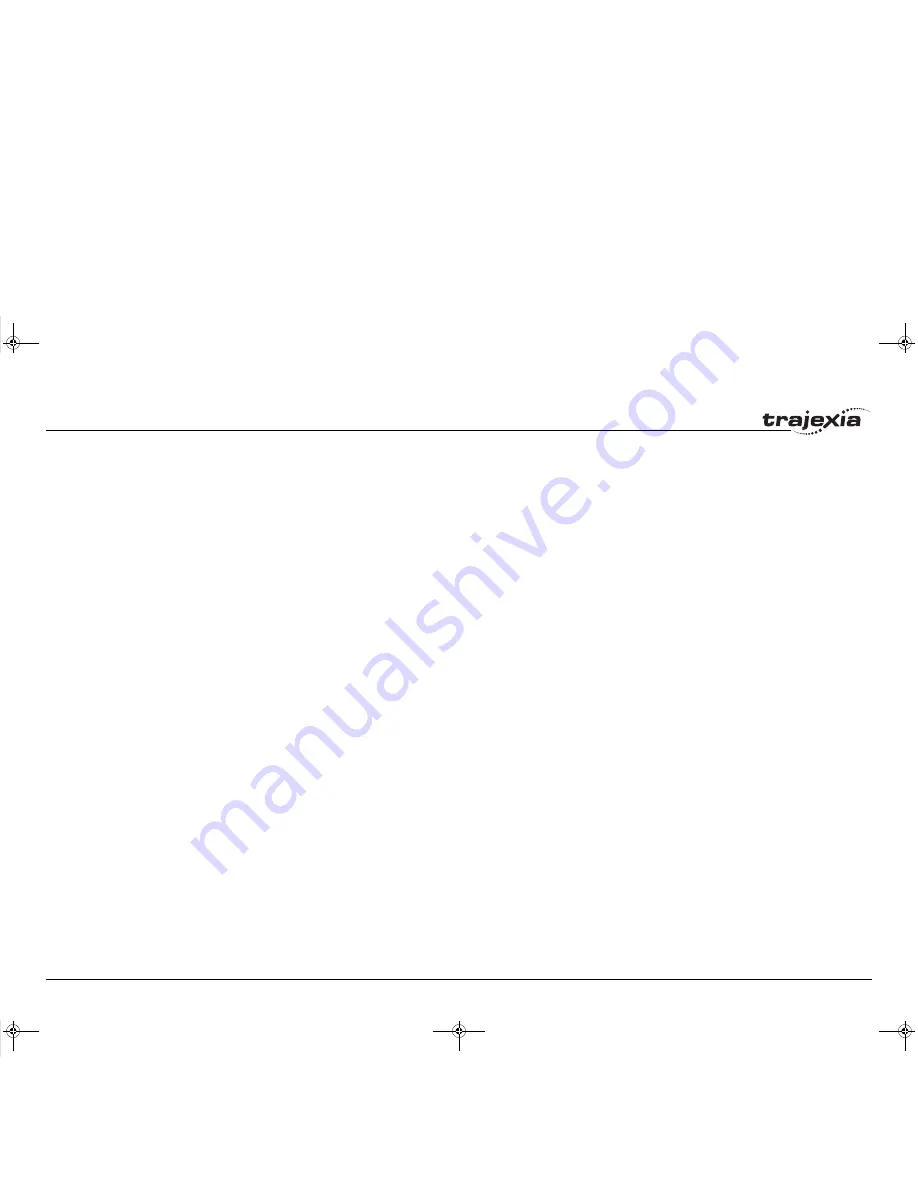
Examples and tips
PROGRAMMING MANUAL
243
Revi
si
on 3.0
on Servo Driver parameter Pn205, see the Sigma-II Servo Driver
manual. Taking this parameter value into account, the maximum
position value the encoder can signal is:
which makes it Pn205 complete turns, plus the position within one
turn (the fraction from 0 to and excluding 1). When the
MECHATROLINK connection is established with the drive, the
absolute encoder position is read from the drive and the value is
written in
MPOS
(after the conversion:
UNITS
× Pn202/Pn203).
When the mechanical system has a limited travel distance to move,
like in a ball screw, the value of the parameter Pn205 should be set
large enough to have an overflow of the counter out of the effective
position. This is called limited axis or finite axis. A typical example
of a limited axis is a ball screw, as shown in fig. 24. When the
mechanical system always moves in the same direction, it reaches
the overflow of the multiturn counter. In this case, the value of
Pn205 must guarantee that the overflow always occurs in the same
position with respect to the machine. This is called unlimited axis
and a typical example of it is a turntable shown in fig. 20. It can be
achieved with the following equation: the smallest value of
m
such
that:
Because
n
and
m
are integers: Pn205 =
m
– 1. This setting is
explained in the following example.
max_encoder_count_value = (Pn205 + 1) encoder_counts - 1
.
n machine_cycles = m motor_revolution
.
.
I52E-EN-03.book Seite 243 Freitag, 29. Juni 2007 11:55 11