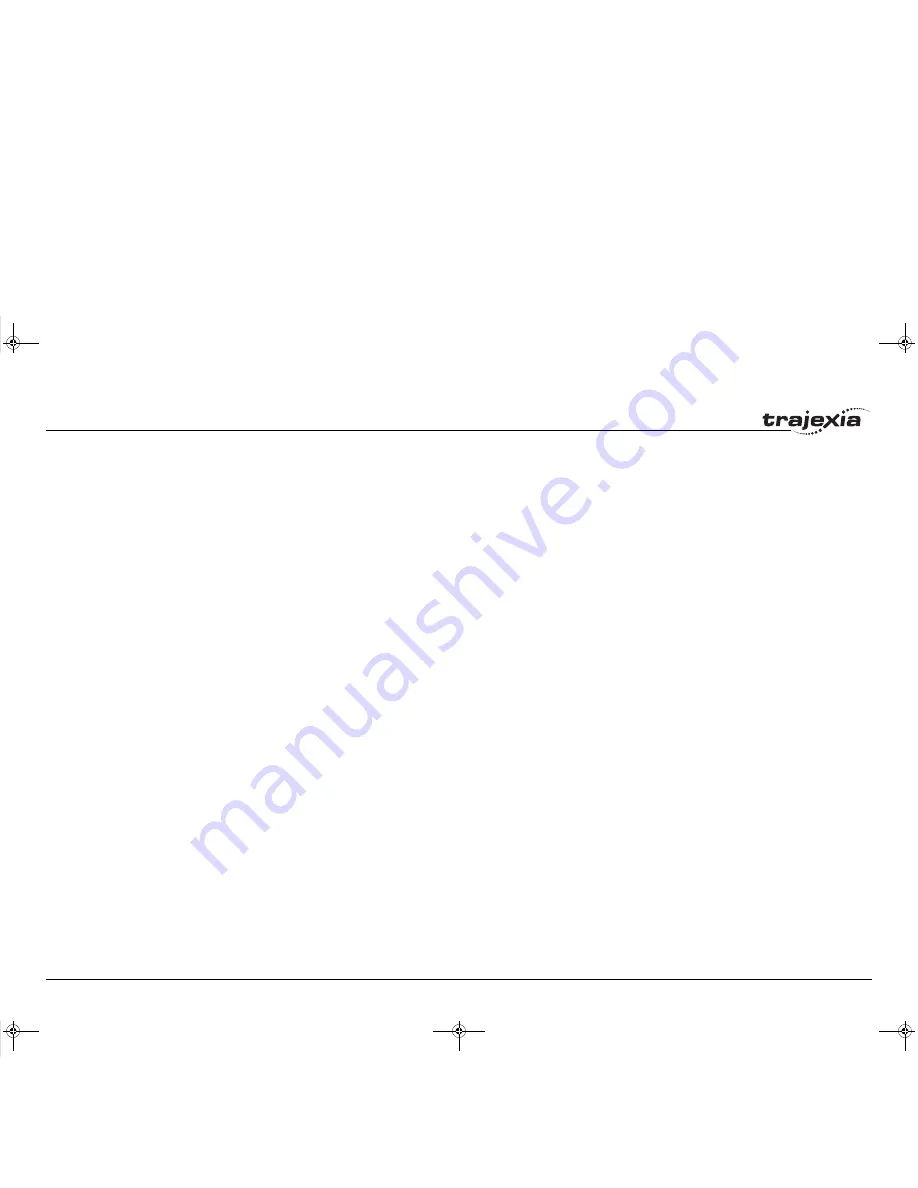
Contents
PROGRAMMING MANUAL
12
Revi
si
on 3.0
3.2.238 SCOPE_POS .................................................................................................................................................................................................................137
3.2.239 SELECT..........................................................................................................................................................................................................................137
3.2.240 SERVO ...........................................................................................................................................................................................................................137
3.2.241 SERVO_PERIOD ...........................................................................................................................................................................................................137
3.2.242 SET_BIT .........................................................................................................................................................................................................................138
3.2.243 SETCOM ........................................................................................................................................................................................................................138
3.2.244 SGN................................................................................................................................................................................................................................139
3.2.245 SIN..................................................................................................................................................................................................................................139
3.2.246 SLOT ..............................................................................................................................................................................................................................139
3.2.247 SPEED ...........................................................................................................................................................................................................................139
3.2.248 SQR................................................................................................................................................................................................................................140
3.2.249 SRAMP...........................................................................................................................................................................................................................140
3.2.250 STEP ..............................................................................................................................................................................................................................140
3.2.251 STEP_RATIO .................................................................................................................................................................................................................140
3.2.252 STEPLINE ......................................................................................................................................................................................................................141
3.2.253 STOP..............................................................................................................................................................................................................................141
3.2.254 SYSTEM_ERROR..........................................................................................................................................................................................................142
3.2.255 T_REF ............................................................................................................................................................................................................................142
3.2.256 TABLE ............................................................................................................................................................................................................................143
3.2.257 TABLEVALUES ..............................................................................................................................................................................................................143
3.2.258 TAN ................................................................................................................................................................................................................................144
3.2.259 THEN..............................................................................................................................................................................................................................144
3.2.260 TICKS .............................................................................................................................................................................................................................144
3.2.261 TIME ...............................................................................................................................................................................................................................144
3.2.262 TIME$ .............................................................................................................................................................................................................................145
3.2.263 TO...................................................................................................................................................................................................................................145
3.2.264 TRANS_DPOS ...............................................................................................................................................................................................................145
3.2.265 TRIGGER .......................................................................................................................................................................................................................145
3.2.266 TROFF............................................................................................................................................................................................................................145
3.2.267 TRON .............................................................................................................................................................................................................................146
3.2.268 TRUE..............................................................................................................................................................................................................................146
3.2.269 TSIZE .............................................................................................................................................................................................................................146
3.2.270 UNITS.............................................................................................................................................................................................................................147
3.2.271 UNLOCK.........................................................................................................................................................................................................................147
3.2.272 UNTIL .............................................................................................................................................................................................................................147
3.2.273 VERIFY...........................................................................................................................................................................................................................147
3.2.274 VERSION .......................................................................................................................................................................................................................147
3.2.275 VFF_GAIN ......................................................................................................................................................................................................................148
3.2.276 VP_SPEED.....................................................................................................................................................................................................................148
3.2.277 VR...................................................................................................................................................................................................................................148
I52E-EN-03.book Seite 12 Freitag, 29. Juni 2007 11:55 11