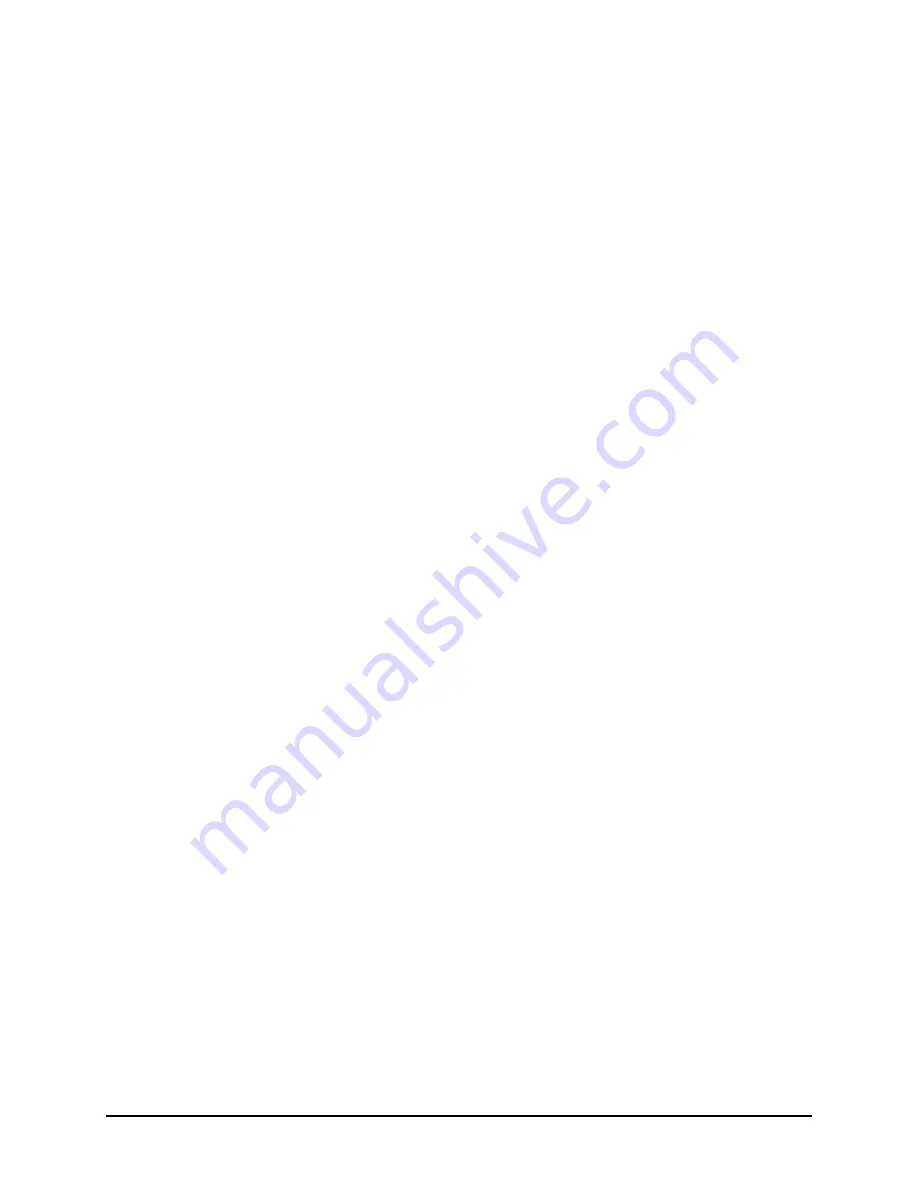
Introduction
1-9
1.10.16.2 Low Fluid Sensor Hardware
An optional capacitive or magnetic sensor is available to detect low fluid conditions. The sensor activates
the light beacon and causes the software to issue a low fluid alert message.
1.10.17 Low Pressure Sensor
The Low Pressure Sensor can be manually set for a pressure from 10 to 100 psi (69 to 689 kPa). The
sensor will issue a signal when main air pressure is lower than the manual set point. This signal causes the
yellow light on the beacon to flash and gives a software error before dispensing is performed.
1.10.18 Mass Flow Calibration
Mass Flow Calibration (MFC) for needle dispensing, also called Calibrated Process Jetting (CPJ) for jet
dispensing, is a patented feature that enables the user to specify the mass to be dispensed as a separate
parameter within the dispensing elements. This is made possible by using a high-precision scale to take
flow rate measurements.
Dispense patterns are programmed with a specified weight. The Fluidmove software includes a fluid
manager where the user specifies flow rate measurement intervals to ensure that a statistically meaningful
flow rate value is obtained. MFC (CPJ) automatically compensates for changes in fluid viscosity,
measuring the mass per dot and comparing it to user-specified min/max values. See
CPJ has two major benefits. First, it ensures the right amount of material is dispensed for each part from
the beginning to the end of the production run. Second, it reduces daily setup time by automatically
compensating for changes in viscosity or fluid delivery flow rate.
1.10.19 Power Manager
The Power Manager is located inside the rear cabinet and houses the Main Circuit Breaker and the Main
Power Inlet. It also contains the EMO circuitry. The EMO button, the green ON (
I
) button, and the black
OFF (0) button are directly connected to the Power Manager. A 10 Amp Power Manager is standard on
S2-900 dispensing systems. A 30 Amp Power Manager is standard on the S2-900P dispensing systems.
An optional Japanese Power Manager is also available.
1.10.20 Pre- and Post-Queue Stations
Pre- and/or post-queue heat stations can be added depending on application requirements.
1.10.21 Process Development Hot Plate
The Process Development Hot Plate (PDHP) converts the S2-900 system to batch mode for process
development with contact heat, providing precise temperature control for improved material flow-out.
The PDHP includes an integral vacuum source with threaded tooling holes for vacuum access or part
fixturing and accommodates a wide variety of standard carrier sizes.
1.10.22 Programmable Fluid and Valve Pressure
Electro-pneumatic regulators control the valve pressure, fluid pressure and cooling/coaxial pressure.
These regulators are integrated into the platform so pressure set point values can be set in the Fluidmove
software. This reduces the possibility of operator error associated with manual regulator adjustment and
allows the user to import a recipe with pressure set points incorporated into the program.
Содержание Spectrum II S2-900 C Series
Страница 2: ......
Страница 34: ...1 20 Introduction 1 11 7 Rear View Figure 1 8A S2 900 Rear View 30A Power Manager shown 1 2 3 4 5 7 6...
Страница 36: ...1 22 Introduction 1 11 8 Rear View Open Figure 1 9A S2 900 Rear View Open 1 2 3 4...
Страница 40: ......
Страница 124: ......
Страница 157: ...Calibration and Adjustment 5 33 Figure 5 38 Dispense Lift Table Controls...
Страница 159: ...Calibration and Adjustment 5 35 Figure 5 40 Beacon Configuration Window...
Страница 186: ......
Страница 197: ...Troubleshooting 7 11 Figure 7 1 Scale Setup Menu Figure 7 2 Scale Error Message...
Страница 200: ......
Страница 215: ...Parts Replacement 8 15 Figure 8 11 Replacing a Panel Mounted Fuse...
Страница 218: ......
Страница 223: ...Specifications 9 5 Top View mm Back View mm Figure 9 2 S2 900 System Dimensions 2 of 2...
Страница 225: ...Specifications 9 7 Top View mm Back View mm Figure 9 4 S2 9XXC System Dimensions 2 of 2...
Страница 228: ...A 2 Appendix A Material Safety Information A 2 1 Multemps PS NO 2...
Страница 229: ...Appendix A Material Safety Information A 3...
Страница 230: ...A 4 Appendix A Material Safety Information...
Страница 231: ...Appendix A Material Safety Information A 5...
Страница 232: ...A 6 Appendix A Material Safety Information...
Страница 233: ...Appendix A Material Safety Information A 7...
Страница 234: ...A 8 Appendix A Material Safety Information A 2 2 Moly Graph Extreme Pressure Multi Purpose Grease...
Страница 235: ...Appendix A Material Safety Information A 9...
Страница 236: ...A 10 Appendix A Material Safety Information...
Страница 237: ...Appendix A Material Safety Information A 11...
Страница 238: ...A 12 Appendix A Material Safety Information...
Страница 239: ...Appendix A Material Safety Information A 13...
Страница 240: ...A 14 Appendix A Material Safety Information...
Страница 246: ......
Страница 252: ......
Страница 258: ......