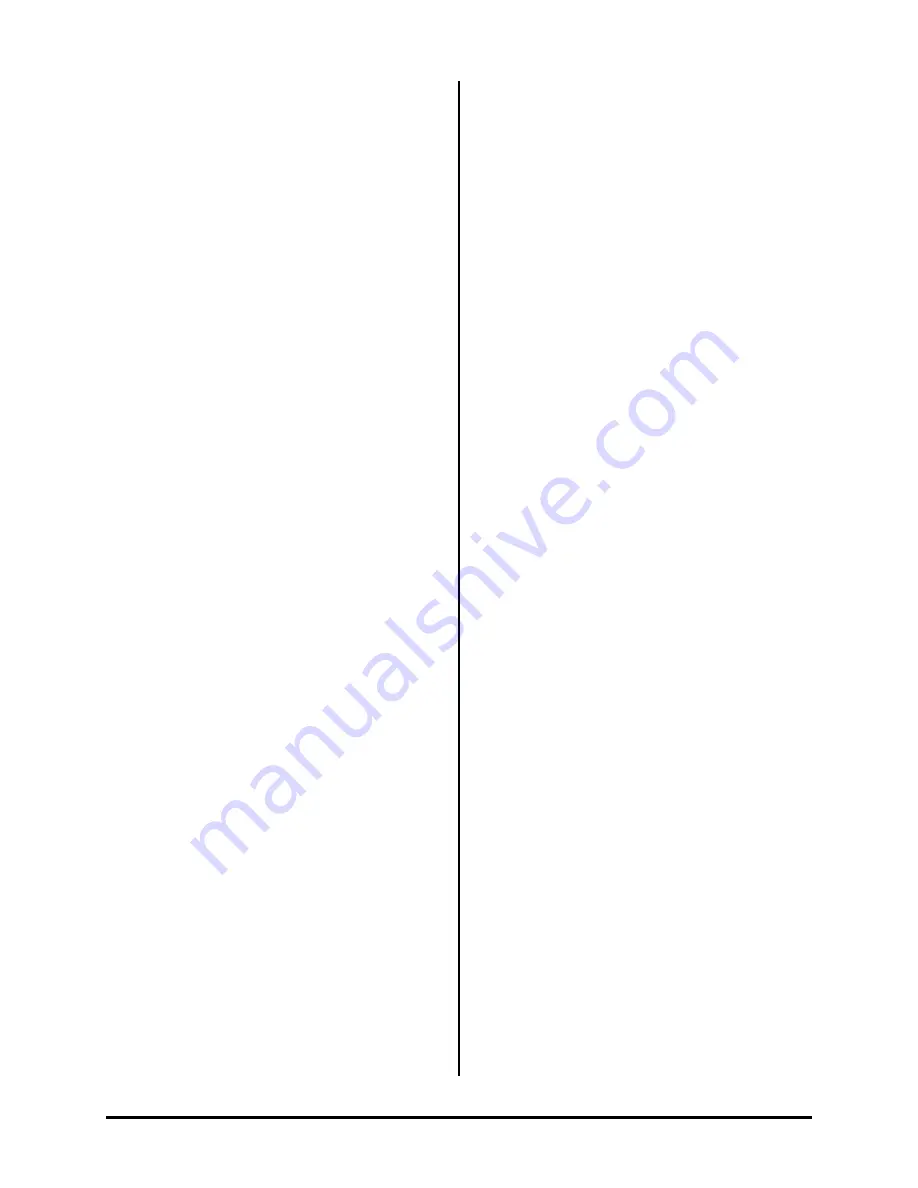
G-4
Glossary
Main Circuit Breaker:
The Main Circuit Breaker is the
main power switch for the dispensing system. It protects
the dispensing system from facility power surges and
controls the flow of facility AC power supplied to the
Power Manager. A flange to the right of the Main
Circuit Breaker allows it to be locked in the OFF
position during servicing. Switching OFF the Main
Circuit Breaker cuts power to all dispensing system
electrical components.
Maintenance:
Planned or unplanned activities intended
to keep the dispensing system in good working order.
Mass Flow Calibration (MFC):
Mass Flow Calibration
for needle dispensing is a patented feature that enables
the user to specify the mass to be dispensed as a
separate parameter within the dispensing elements. This
is made possible by using a high precision scale to take
flow rate measurements.
Monocle Vision:
A 5-light vision system that features
five independently adjustable LED's at different angles.
This feature is available on the S2-900 Dispensing
System.
Multimove Conveyor :
Multi-move technology allows
parts to move concurrently. Simultaneous movement
significantly decreases convey time, contributing to
increased throughput. In one sequence, a part is
transported from the upstream machine while the
dispensing system unloads a part from the dispense
station to the downstream machine
Needle Heater:
The Needle Heater is an RTD-
controlled heating element that provides needle heat on
the DV-7000 and DV-8000 Dispensing Valves and
nozzle heat for the DJ-9000 Dispense Jet. The Needle
Heater heats the dispensing fluid to maintain a
consistent viscosity and flowrate.
Needle Sensor Substrate:
A ceramic pad near the
Needle Sensor that is dispensed upon during needle
location definition routines.
OEM:
Original Equipment Manufacturer.
Operation:
Functions, such as setting and manipulating
dispensing system controls, by which the operator
causes the equipment to perform its intended purpose.
Operator:
A non-technical level position. The
production operator monitors and operates pre-
programmed dispensing systems during production runs
and performs minor routine maintenance.
Outputs:
Electrical signals to control devices that must
turn On and Off on command.
Pattern Recognition System:
A vision system that
finds workpiece fiducials to reliably locate dispensing
sites and compensates for minor workpiece
misalignment during dispensing.
Personal Protective Equipment (PPE):
Clothing and
Equipment worn to reduce the risk of personal injury
from hazards associated with operation, maintenance,
and servicing of the dispensing system. This includes
the wearing of rubber gloves and safety glasses.
Pneumatic Devices:
Air pressure actuated devices such
as Stop Pins, Clamp Bars, and Lift Tables.
Port:
A hardware interface on a computer to which you
can connect a device. An opening in a mechanical
device such as the vacuum port in a contact heater or the
Conveyor port on the dispensing system.
Post-Dispense Station:
The part of the dispensing
chamber where a workpiece is held after it leaves the
Dispense Station and before the workpiece leaves the
system. The part may be heated in the Post-dispense
Station, but no dispensing is performed.
Power Manager:
The Power Manager is located inside
the rear cabinet and houses the Main Circuit Breaker
and the Main Power Inlet. It also contains the EMO
circuitry. The EMO button, the green ON (
I
) button, and
the black OFF (0) button are directly connected to the
Power Manager.
Precision Fluid Air Gauge and Regulator:
The
Precision Fluid Air Gauge and Regulator controls air
supplied to the fluid syringe.
Pre-Dispense Station:
The part of the dispensing
chamber where a workpiece is held before entering the
Dispense Station. The workpiece may be heated in the
Pre-dispense Station, but no dispensing is performed.
Production Shutdown:
When all dispensing has been
stopped under non-emergency conditions such as the
end of a shift.
Psi:
Pounds per Square Inch (lbs/in
2
). English unit of
pressure measurement.
Pump:
See Valve
.
Purge Station:
A location at the front of the dispensing
chamber where the outer diameter of the dispensing
needle is cleaned and the Dispensing Valve is
automatically purged at user-defined intervals. A
disposable plastic cup inside of the Purge Station
catches the dispensed fluid.
PWA:
Printed Wiring Assembly. The completed PWB
with electrical components installed. Also known as a
printed circuit board assembly (PCBA).
PWB:
Printed Wiring Board. An insulating board
containing conductive tracks for electrical circuit
connections on which chips and other electronic
components are placed.
Regulator:
Device for controlling the amount of air
pressure supplied to a pneumatic system.
Reticle:
A group of lines, circles, angles, or other
pattern used as a measuring reference, as a focusing
target, or to define a camera field of view.
Содержание Spectrum II S2-900 C Series
Страница 2: ......
Страница 34: ...1 20 Introduction 1 11 7 Rear View Figure 1 8A S2 900 Rear View 30A Power Manager shown 1 2 3 4 5 7 6...
Страница 36: ...1 22 Introduction 1 11 8 Rear View Open Figure 1 9A S2 900 Rear View Open 1 2 3 4...
Страница 40: ......
Страница 124: ......
Страница 157: ...Calibration and Adjustment 5 33 Figure 5 38 Dispense Lift Table Controls...
Страница 159: ...Calibration and Adjustment 5 35 Figure 5 40 Beacon Configuration Window...
Страница 186: ......
Страница 197: ...Troubleshooting 7 11 Figure 7 1 Scale Setup Menu Figure 7 2 Scale Error Message...
Страница 200: ......
Страница 215: ...Parts Replacement 8 15 Figure 8 11 Replacing a Panel Mounted Fuse...
Страница 218: ......
Страница 223: ...Specifications 9 5 Top View mm Back View mm Figure 9 2 S2 900 System Dimensions 2 of 2...
Страница 225: ...Specifications 9 7 Top View mm Back View mm Figure 9 4 S2 9XXC System Dimensions 2 of 2...
Страница 228: ...A 2 Appendix A Material Safety Information A 2 1 Multemps PS NO 2...
Страница 229: ...Appendix A Material Safety Information A 3...
Страница 230: ...A 4 Appendix A Material Safety Information...
Страница 231: ...Appendix A Material Safety Information A 5...
Страница 232: ...A 6 Appendix A Material Safety Information...
Страница 233: ...Appendix A Material Safety Information A 7...
Страница 234: ...A 8 Appendix A Material Safety Information A 2 2 Moly Graph Extreme Pressure Multi Purpose Grease...
Страница 235: ...Appendix A Material Safety Information A 9...
Страница 236: ...A 10 Appendix A Material Safety Information...
Страница 237: ...Appendix A Material Safety Information A 11...
Страница 238: ...A 12 Appendix A Material Safety Information...
Страница 239: ...Appendix A Material Safety Information A 13...
Страница 240: ...A 14 Appendix A Material Safety Information...
Страница 246: ......
Страница 252: ......
Страница 258: ......