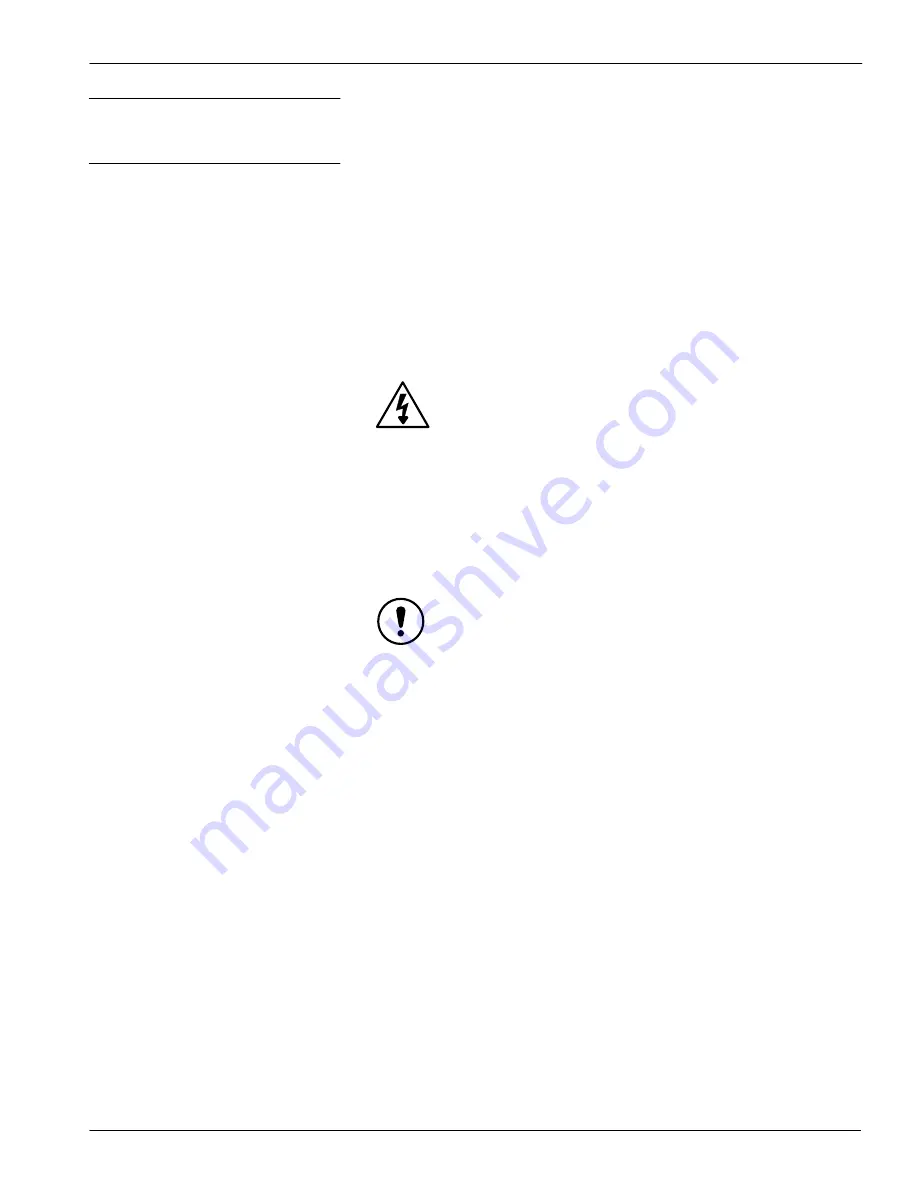
Installation
3-17
E
1996 Nordson Corporation
All rights reserved
107 041A
Issued 1/96
Manual 12-28
4. Use a small screwdriver, pencil or similar tool to push the notched
card lock (8) on the lower card guide (7) to the left. Align the lock with
the unlock notch (9) on the front of the guide.
NOTE: Do not remove the thermocouple wires from the
thermocouple card.
5. Disconnect the ribbon cable from the touchscreen card (4).
6. Disconnect the cables from the remaining controller cards (5).
7. Pull the controller cards (4, 5, and 6) away from the backplane about
2.5 cm (1 in.). Leave the cards in the card cage. Remove the
grounding strap from the E-stop panel.
WARNING: Hazardous voltages are present when the main
power is on. Serious injury or death may result if personnel fail
to observe safety procedures.
8. Apply power to the oven.
9. Turn on the circuit breaker (2).
10. Make sure that the system blower is rotating in the direction indicated
by the red arrow above the blower shaft.
CAUTION: Do not change the wiring at the blower motor.
Serious system failure may result.
11. If the blower rotates in the wrong direction:
a. Turn off, lock out, and tag the 3-phase service line to the oven.
b. Remove the circuit breaker access panel (20).
c. Remove the screws (1) and the plastic cover (3) attached to the
circuit breaker (2).
d. Perform the necessary tasks to switch any two of the service line
connections to the circuit breaker (2).
e. Repeat steps 7 through 9.
12. Verifying Operating
Voltages and Blower
Rotation
(contd.)
Содержание 107 041A
Страница 1: ...Select Cure 100 Inch IR Oven Part 107 041A NORDSON CORPORATION D AMHERST OHIO D USA ...
Страница 8: ...Table of Contents vi E 1996 Nordson Corporation All rights reserved 107 041A Issued 1 96 Manual 12 28 ...
Страница 9: ...E 1995 Nordson Corporation All rights reserved Issued 11 95 12 28s1 Section 1 Safety ...
Страница 10: ...Safety 1 0 E 1995 Nordson Corporation All rights reserved Issued 11 95 12 28s1 ...
Страница 23: ...E 1996 Nordson Corporation All rights reserved 107 041A Issued 1 96 Manual 12 28 Section 2 Description ...
Страница 24: ...Description 2 0 E 1996 Nordson Corporation All rights reserved 107 041A Issued 1 96 Manual 12 28 ...
Страница 32: ...Description 2 8 E 1996 Nordson Corporation All rights reserved 107 041A Issued 1 96 Manual 12 28 ...
Страница 33: ...E 1996 Nordson Corporation All rights reserved 107 041A Issued 1 96 Manual 12 28 Section 3 Installation ...
Страница 34: ...Installation 3 0 E 1996 Nordson Corporation All rights reserved 107 041A Issued 1 96 Manual 12 28 ...
Страница 61: ...E 1996 Nordson Corporation All rights reserved 107 041A Issued 1 96 Manual 12 28 Section 4 Operation ...
Страница 62: ...Operation 4 0 E 1996 Nordson Corporation All rights reserved 107 041A Issued 1 96 Manual 12 28 ...
Страница 83: ...E 1996 Nordson Corporation All rights reserved 107 041A Issued 1 96 Manual 12 28 Section 5 Maintenance ...
Страница 84: ...Maintenance 5 0 E 1996 Nordson Corporation All rights reserved 107 041A Issued 1 96 Manual 12 28 ...
Страница 101: ...E 1996 Nordson Corporation All rights reserved 107 041A Issued 1 96 Manual 12 28 Section 6 Troubleshooting ...
Страница 102: ...Troubleshooting 6 0 E 1996 Nordson Corporation All rights reserved 107 041A Issued 1 96 Manual 12 28 ...
Страница 147: ...E 1996 Nordson Corporation All rights reserved 107 041A Issued 1 96 Manual 12 28 Section 7 Parts ...
Страница 148: ...Parts 7 0 E 1996 Nordson Corporation All rights reserved 107 041A Issued 1 96 Manual 12 28 ...
Страница 161: ...E 1996 Nordson Corporation All rights reserved 107 041A Issued 1 96 Manual 12 28 Section 8 Specifications ...
Страница 162: ...Specifications 8 0 E 1996 Nordson Corporation All rights reserved 107 041A Issued 1 96 Manual 12 28 ...
Страница 166: ...Specifications 8 4 E 1996 Nordson Corporation All rights reserved 107 041A Issued 1 96 Manual 12 28 ...