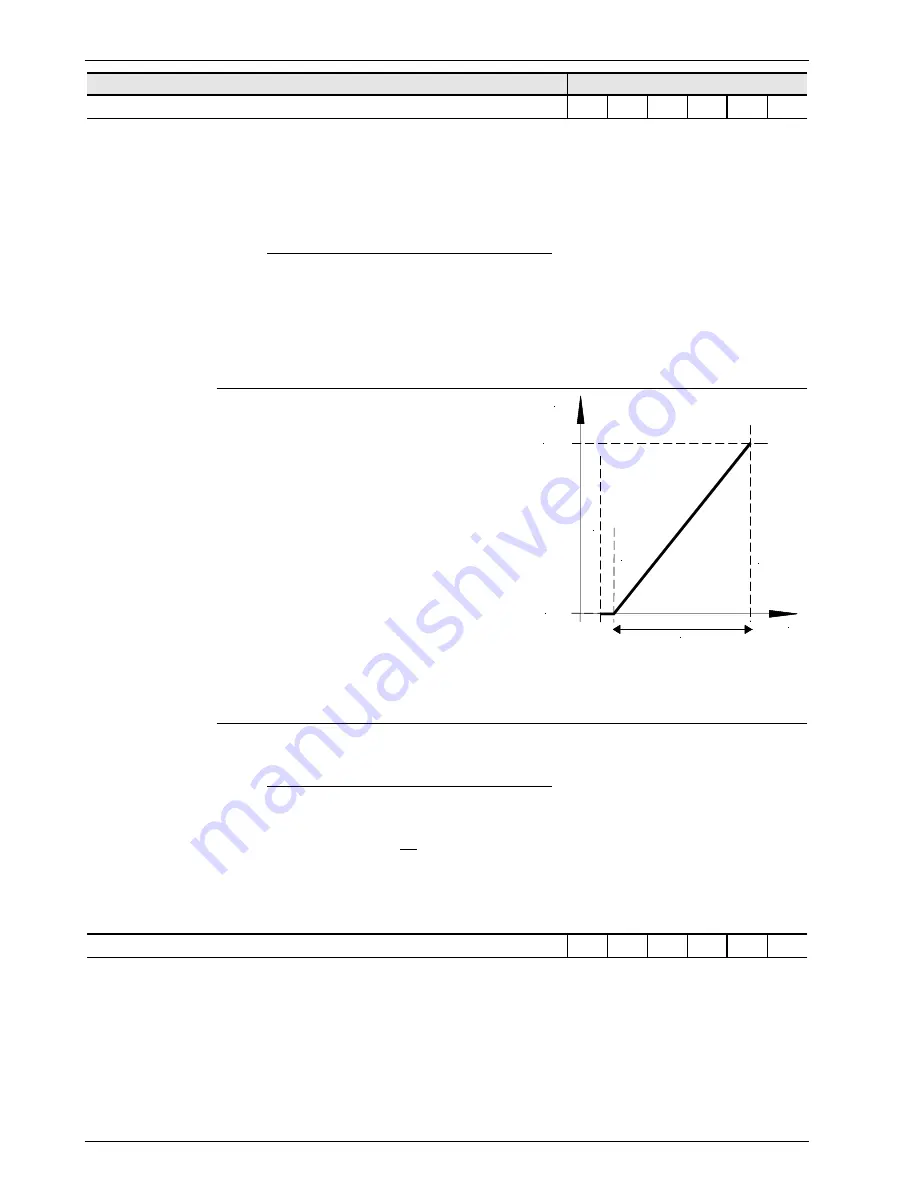
NORDAC SK 700E Operating Manual
76
Subject to technical alterations
BU 0700 EN
Parameter
Setting value / Description / Note
Available with option
P401
Mode analog input 1
BSC
STD
MLT
0...3
[ 0 ]
0 =
0 – 10V limited:
An analog setpoint smaller than the programmed adjustment 0% (P402) does
not lead to undershooting of the programmed minimum frequency (P104). Therefore does not
lead to any rotation direction reversal.
1 =
0 - 10V:
If a setpoint smaller than the programmed adjustment 0% (P402) is present, this can
cause a change in direction rotation. This allows rotation direction reversal using a simple
voltage source and potentiometer.
E.g. internal setpoint with rotation direction change: P402 = 5V, P104 = 0Hz, Potentiometer 0–
10V
⇒
Rotation direction change at 5V in mid-range setting of the potentiometer.
During the reversing moment (hysteresis =
±
P505), the drive stands still when the minimum
frequency (P104) is smaller than the absolute minimum frequency (P505). A brake that is
controlled by the FI will have entered the hysteresis range.
If the minimum frequency (P104) is greater than the absolute minimum frequency (P505), the
drive reverses when the minimum frequency is reached. In the hysteresis range
±
P104, the FI
supplies the minimum frequency (P104), the brake controlled by the FI does not enter the
range.
2 =
0 – 10V controled:
If the minimum
adjusted setpoint (P402) is undershot by
10% of the difference value from P403
and P402, the FI output switches off.
Once the setpoint is greater than [
P402
- (10% * (P403 - P402))]
, it will deliver
an output signal again.
f/Hz
P104 (fmin)
P105 (fmax)
P
403 = 10,
0V
P
402 = 2,
0V
= 8,0V
U/V
O
FF =
2,
0V
-
10%
*
8,
0V
=
1,
2V
Example setpoint 4-20mA:
P402: Adjustment 0% = 1V; P403: Adjustment 100% = 5V; -10%
corresponds to -0.4V; i.e. 1...5V (4...20mA) normal operating zone, 0.6...1V = minimum
frequency setpoint, below 0.6V (2.4mA) output switches off.
3 =
- 10V – 10V:
If a setpoint smaller than the programmed adjustment 0% (P402) is present, this
can cause a change in direction rotation. This allows rotation direction reversal using a simple
voltage source and potentiometer.
E.g. internal setpoint with rotation direction change: P402 = 5V, P104 = 0Hz, Potentiometer 0–
10V
⇒
Rotation direction change at 5V in mid-range setting of the potentiometer.
During the reversing moment (hysteresis =
±
P505), the drive stands still when the minimum
frequency (P104) is smaller than the absolute minimum frequency (P505). A brake that is
controlled by the FI will not have entered the hysteresis range.
If the minimum frequency (P104) is greater than the absolute minimum frequency (P505), the
drive reverses when the minimum frequency is reached. In the hysteresis range
±
P104, the FI
supplies the minimum frequency (P104), the brake controlled by the FI does not enter the
range.
P402
Adjustment 1 0%
BSC
STD
MLT
-50.0 ... 50.0 V
[ 0.0 ]
This parameter is used to set the voltage corresponding to the minimum value of the selected function
for analog input 1.
In the factory setting (setpoint) this value is equivalent to the setpoint set via P104 >Minimum
frequency<.
Typical setpoints and corresponding settings:
0 – 10V
Æ
0.0
V
2 – 10 V
Æ
2.0 V (for function 0-10 V monitored)
0 – 20 mA
Æ
0.0 V (internal resistance approx. 250
Ω
)
4 – 20 mA
Æ
1.0 V (internal resistance approx. 250
Ω
)