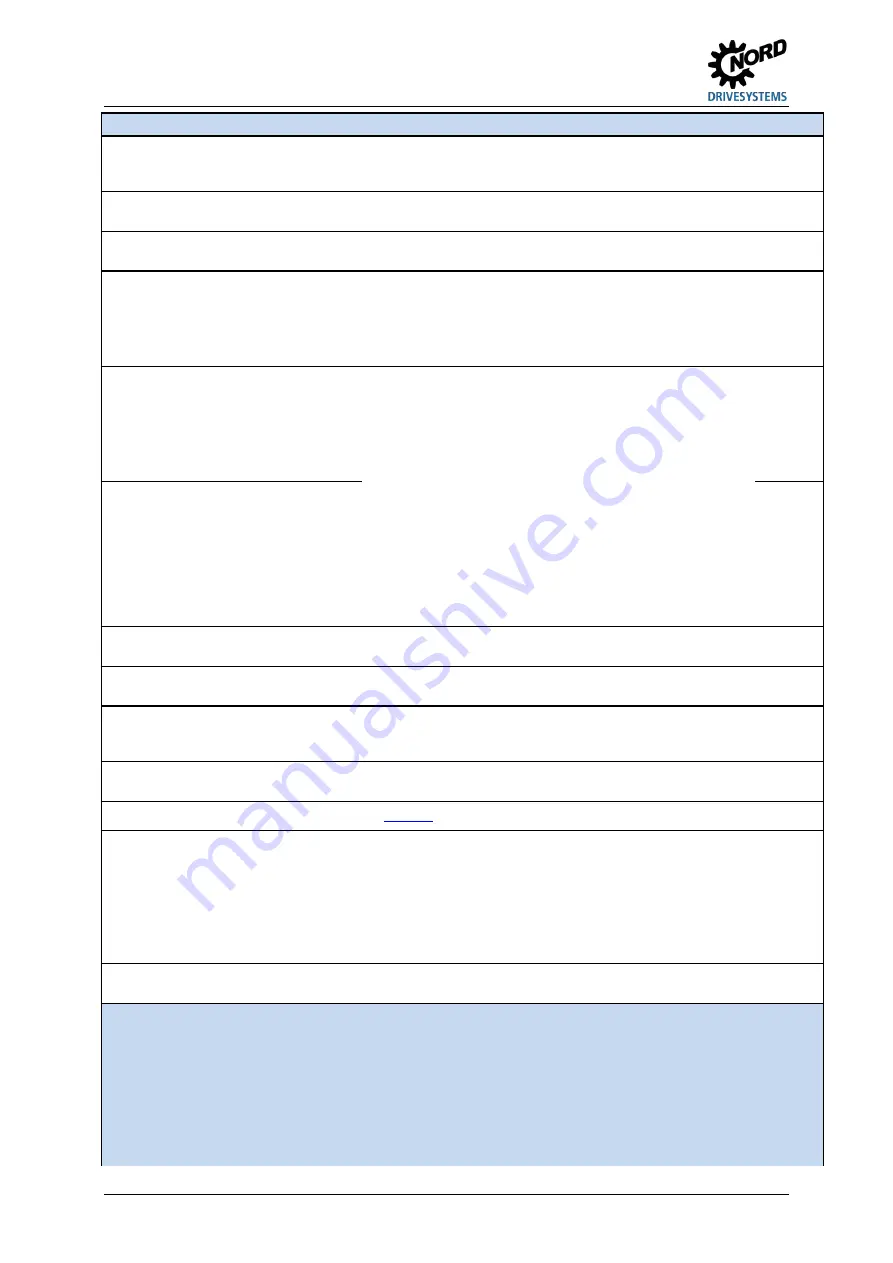
NORDAC LINK (SK 250E-FDS ... SK 280E-FDS) – Users Manual for Frequency Inverters as Field Distributors
122
BU 0250 en-3021
Value
Function
Description
Signal
67
Dig. output man/auto set
“Set digital output manually /
automatically”
Set digital output 1 manually or via the set function in (P434).
High
68
Digital output. man set
“Set digital output manually”
Set digital output 1 manually
High
69
Speed measurement with ini.
“Speed measurement with initiator”
Simple speed measurement (pulse measurement) with initiator
pulses
70
Evacuation run
“Activate evacuation run”
This provides the option of operation with a very low link circuit
voltage (e.g. from batteries). With this function the charging
relay is actuated and the existing monitoring functions are
disabled.
NOTICE!
No overload monitoring! (E.g. lifting equipment)
High
71
3
Motorpot.F+ and Save
“Motor potentiometer function
Fre with automatic saving".
With this “motor pot. Function” a setpoint (value) is set and
saved via the digital inputs. With R/L by the controller, this is
then started up in the correspondingly enabled direction. The
frequency is retained if the direction is changed.
Simultaneous activation of the +/- function causes the
frequency setpoint value to be set to zero.
The frequency setpoint value can also be displayed or set in the
operating value display (P001 = 30, actual setpoint MP-S) or
can be displayed or set in P718.
A minimum frequency which is set (P104) remains effective.
Other setpoint values, e.g. analog or fixed frequencies can be
added or subtracted.
Adjustment of the frequency setpoint is performed with the
ramps from P102/103.
High
72
3
Motorpot.F- and Save
“Motor potentiometer function
frequency
-
with automatic saving".
High
73
2
Right dfast.
“Disable left Quick stop“
As for setting 31, however coupled to the "Quick Stop” function. Low
74
2
Left fast.
“Disable left Quick stop“
As for setting 32, however coupled to the "Quick Stop” function. Low
75
Dig. output man/auto set
“Set digital output 2 manually /
automatically”
As for function 67, but for digital output 2
High
76
Dig. Output 2 man. set
“Set digital output 2
manually”
As for function 68, but for digital output 2
High
77
… 78 reserved for POSICON
79
Rotor pos. ident.
Precise knowledge of the rotor position is essential for PMSM
operation. Rotor position identification is performed if the
following conditions are met:
•
The frequency inverter is in the status “ready for switch-on”,
•
The rotor position is not known (see P434, P481, function
“28”),
•
Function “2” is selected in P336.
1
0
flank
80
PLC stop
Program execution of the integrated PLC is halted for as long
as the signal is present.
High
1
If no digital input is parameterised for “enable right” or “enable left”, and for devices SK 270E-FDS and higher, all BUS In bits
(P480) which are relevant for AS-i are deactivated, a fixed frequency or the jog frequency results in enabling of the frequency
inverter. The direction of rotation depends on the prefix of the setpoint.
2
Also effective for control via BUS (e.g. RS232, RS485, CANopen, AS Interface, …)
3
For devices without an integrated low voltage unit (integrated low voltage unit: Option “-HVS“), the control unit of the frequency
inverter must be supplied with power for at least 5 minutes after the last motor potentiometer change in order to permanently
save the data.
4
Function cannot be selected via BUS IO In Bits
Содержание NORDAC LINK SK250E-FDS
Страница 211: ...Key word index BU 0250 en 3021 211...
Страница 212: ...6072502 3021...