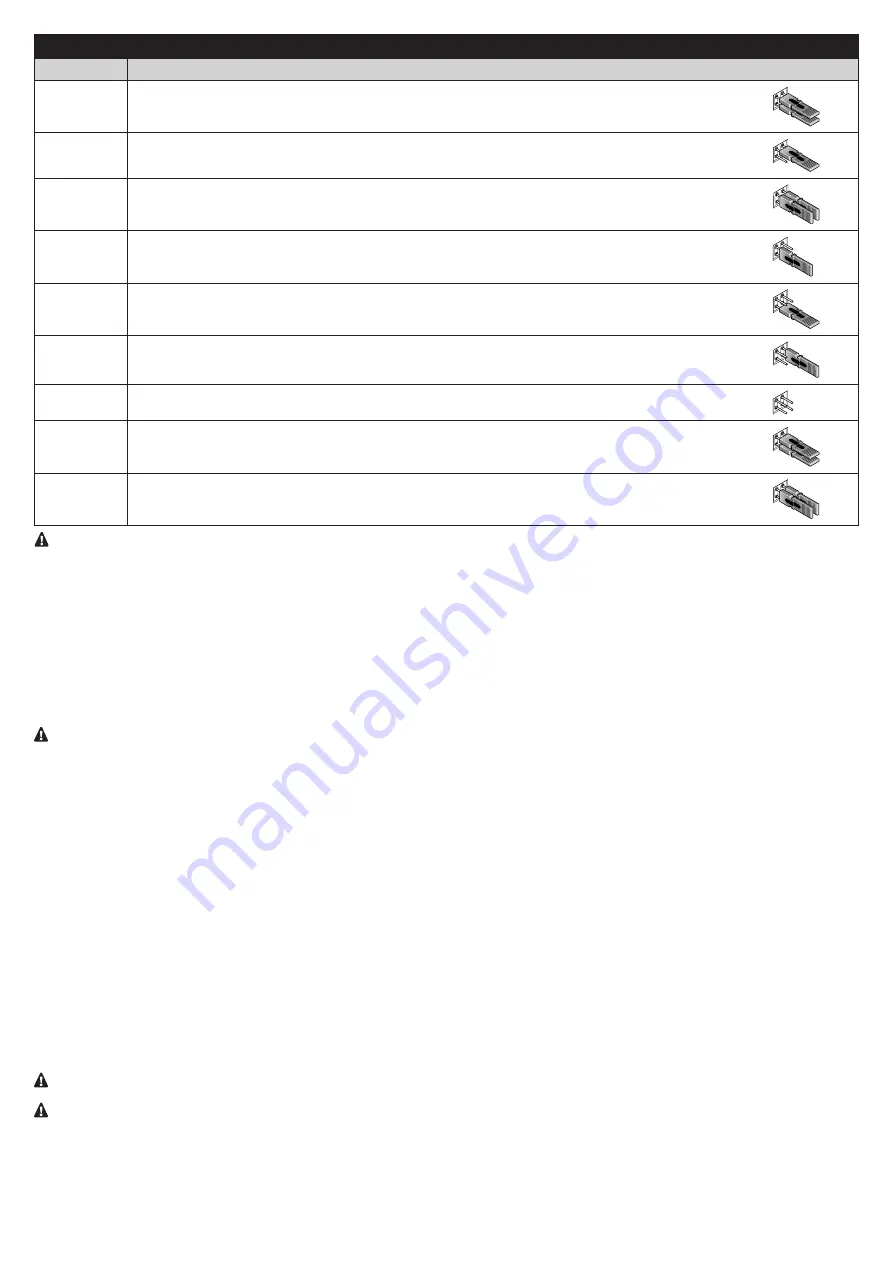
English –
21
Table 9
Photocells
Jumper
PHOTO
Photocell h = 50
activation during closing (reverses to ‘open’)
PHOTO II
Photocell h = 100
activation during closing (reverses to ‘open’)
PHOTO 1
Photocell h = 50
activation during closing (temporary stop and reverses to ‘open’)
PHOTO 1 II
Photocell h = 100
activation during closing (temporary stop and reverses to ‘open’)
PHOTO 2
Photocell with activation during opening (stops the manoeuvre)
PHOTO 2 II
Photocell with activation during opening (stops the manoeuvre)
PHOTO 3
Single photocell with activation during opening and closing (temporary stop and reverses in ‘open’)
FA1
Photocell for opening command
(cut jumper A on the back of the TX and RX cards)
FA2
Photocell for opening command
(cut jumper A on the back of the TX and RX cards)
IMPORTANT! - After the installation or removal of photocells, you need to perform the device acquisition phase (section 5.3)
Note: you can connect 2 photocells to the Bluebus input, with the ‘FA1 open’ and ‘FA2 open’ command function (it is necessary to cut the jumper
A on the back of the TX and RX cards). When these photocells intervene, the control unit commands an opening manoeuvre. For further informa-
tion, refer to the instruction manual for the photocells.
6.3 - STOP input connection
The Stop input causes the immediate stoppage of the manoeuvre, followed by a brief inversion.
Devices with contact types Normally Open (NO), Normally Closed (NC) or devices with a constant resistance of 8.2 KΩ (such as sensitive edges)
can be connected to this input.
During the device acquisition phase, the control unit recognises the type of device connected to the Stop input and later, during normal use of
the automation, the control unit commands a Stop when it senses a change with respect to the acquired situation.
CAUTION! - If you want to ensure category 3 safety with faults according to EN 954-1, you must only use the devices with 8.2
KΩ constant resistance output.
If the connection with 8.2 KΩ constant resistance is used, you can program a device test, at the start of each manoeuvre.
To activate the 8K2
test mode, you must enable the L5 parameter in the 1st level menu.
6.4 - Power for external devices
If you want to power external devices (proximity reader for transponder cards or the backlight of a key selector) you can connect the device to
the product control unit as shown in the figure at the side.
The power supply voltage is 30V DC +5% to -20% with a maximum available current of 100 mA.
6.5 - Alarm system
Configured control units, and those identified with code ***/V1, have an integrated alarm system that activates following 2 consecutive obstacle
detections, or sensitive edge interventions, during the manoeuvre.
After two interventions as described above, the control unit inhibits any movement by activating the automation’s permanent lock and triggering
the siren (connected to the ALARM terminal) for 5 minutes.
To unlock the automation and silence the siren, (any) one of the following must occur: the STOP button on the control panel is pressed, the sensi-
tive edge is pressed, the contact on the SbS terminal is triggered (with the motor stopped) or the contact on the STOP terminal (NC) is triggered.
From then onwards, the control unit will resume its normal operation.
The start of each closing manoeuvre (commanded from a radio transmitter or Oview Terminal) is preceded by a pre-flashing sequence and by
the activation of the siren for 5 seconds (non-excludable), after which the motor will start.
IMPORTANT! - In the event of a power supply failure during the automation’s permanent lock condition, the alarm system will
re-emit the acoustic and visual signals for 5 minutes at the next re-start of the control unit.
WARNING! - The alarm system is active by default and can be deactivated by the user: please note, however, that in this case the
control unit will no longer be compliant with standard UL325.
If required, the alarm siren can be disconnected and the ALARM output can be reconfigured for other applications: in this case the alarm will be
disabled, but all the other safety systems required to detect obstacles will remain active.
The alarm system can be activated/deactivated using the Oview programmer (see paragraph
“Connecting the Oview programmer”
).