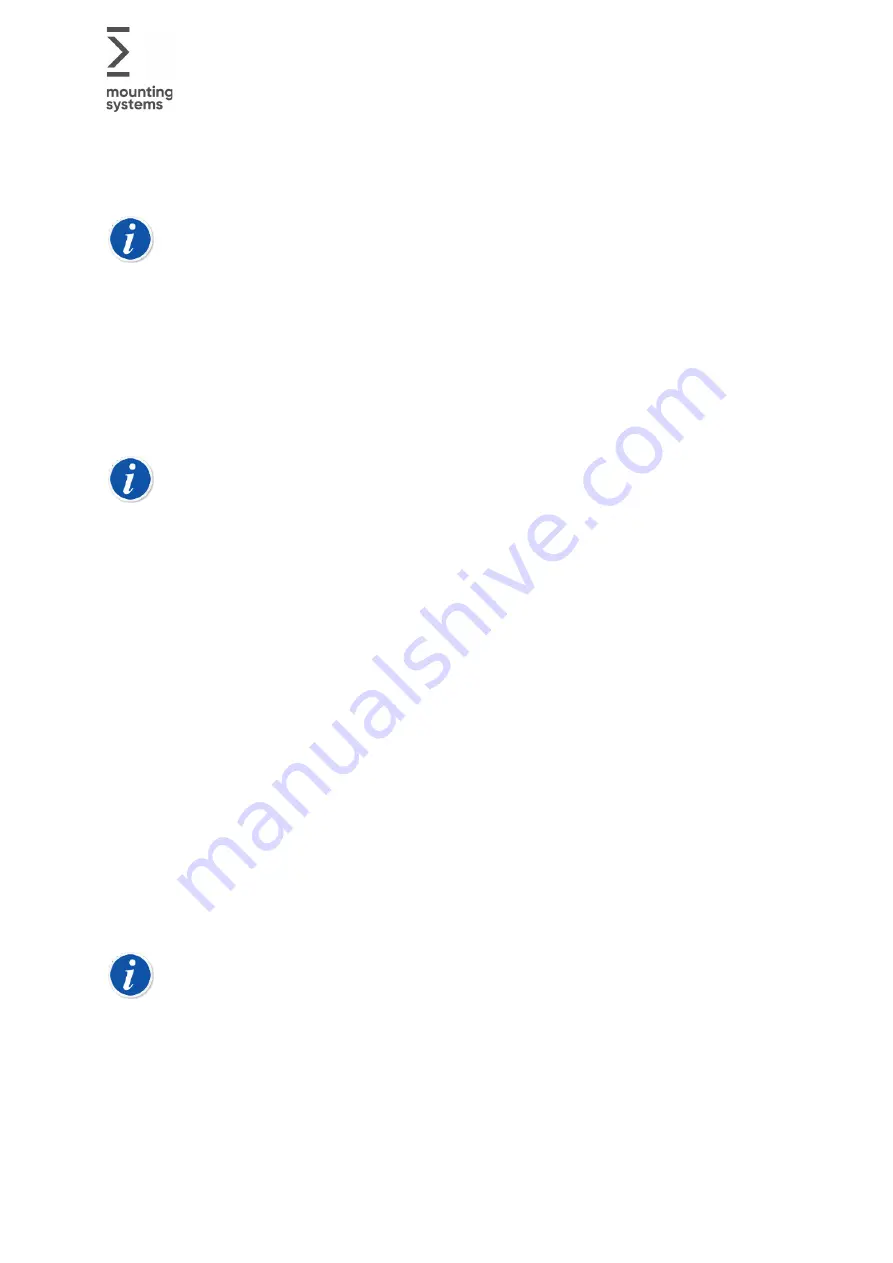
12/60
ST_PM_ Installation Manual_EN_V1.0 | 08.2020
Copyright © 2020 Mounting Systems GmbH
6
Installation
6.1
Cabling
The cabling can be routed differently depending on the project planning
requirements.
Please find the exact details in your project-specific documents.
6.1.1
Network
Each master control unit must be connected to the other master control units via the TCP
network. The connection is made to the on-site network by means of a ground-layable
Cat 7 connecting cable. The maximum length of the connecting cable is 100 m.
The master control units must be connected to the internet to enable support and
upgrades and to synchronise the time.
With an internet connection, the network should be protected from unauthorised
access.
6.1.2
Motor cable
Each power connection in the control cabinet is connected separately to the
corresponding motor on the tracker array. This connection cable must be ground-layable
and shielded. The maximum cable length, between the motor and the frequency inverter
is 50 m, due to the voltage drop in accordance with the data sheet of the frequency
inverter.
Frequency inverter: Siemens SINAMICS V20, 400V, frame size FSA
Connecting cable: 2YSLCYK-JB 3X1.5+3G0.25 BK
Motor connection: MSWTL 25 ISO cable gland
6.1.3
Sensor cables
Each tracker array is equipped with a tilt sensor, fitted directly over the related control
unit at the rafter. The sensor cable is preinstalled at the tilt sensor.
The wind sensor is connected to the analogue input module in the master control cabinet.
The corresponding control cabinet for the wind sensor connection must be indicated in
the project-specific documents.
Sensor cable:
Li2YCYv 2X2X0.34 SW
The motor cable and sensor cables must be laid in accordance with current
standards (respecting the prescribed distances).
6.1.4
Modbus cables
The slave control units must be connected to the assigned master control unit via
Modbus cable as a daisy chain. This connection cable must be ground-layable and
shielded. See the project specific documents.