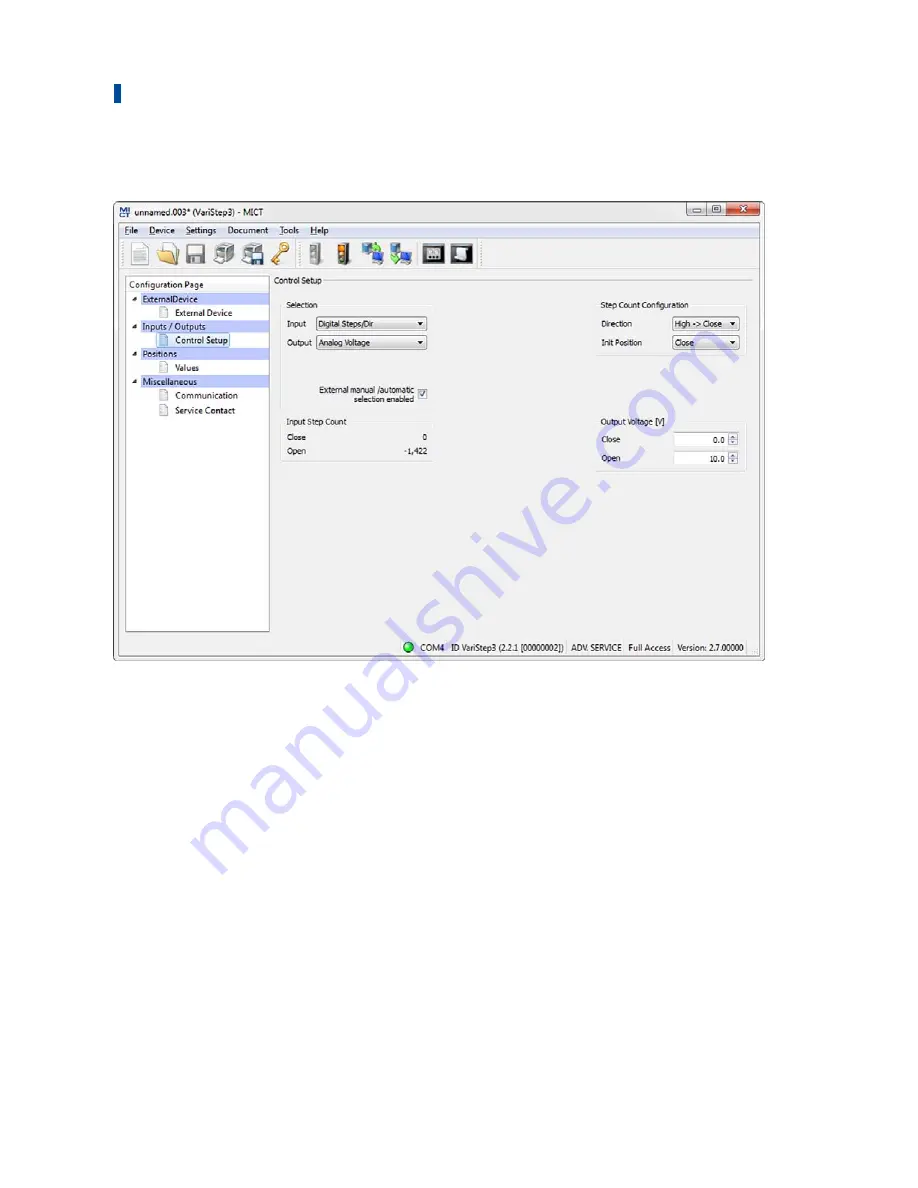
8 Settings via the MICT
56
Rev. 08/2018
8.9.2
Inputs/Outputs – Control Setup
The settings on the configuration page depend on the inputs and outputs used by your master
control. In this case, refer to all information given in the relevant documentations of the control
units. To make changes, approval for the access level
Advanced Service
is required.
Selection
–
Input
Select the input that is to be used for position setting by the master control connected. The
following options are possible:
–
Analog voltage
Position setting is achieved via the analog voltage signal.
–
Analog Current
Position setting is achieved via the analog current signal.
–
Digital Steps/Dir
Position setting is achieved via binary signals (
Steps
,
Dir
).
–
Field bus
Position setting is achieved via a field bus. This requires corresponding configuration of
the communication with the desired field bus (see
Miscellaneous – Communication
on
page 60).
Содержание VariStep3
Страница 1: ...VariStep3 Stepper Motor Driver Operating Manual P N 01 50 020 EN Rev 08 2018...
Страница 16: ...4 Product Description 16 Rev 08 2018...
Страница 91: ...Rev 08 2018 91...
Страница 92: ......