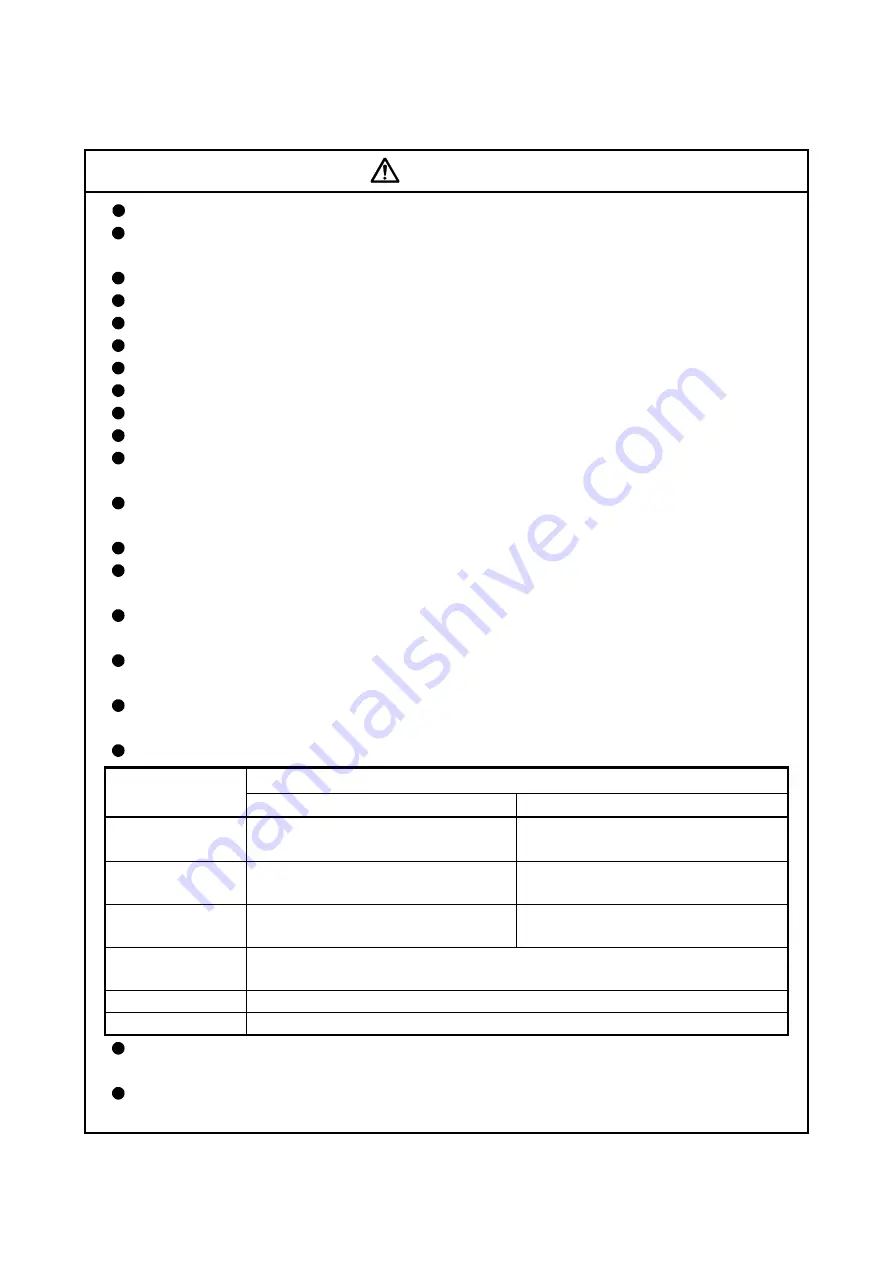
A - 6
CAUTION
Transport the product with the correct method according to the mass.
Use the servomotor suspension bolts only for the transportation of the servomotor. Do not
transport the servomotor with machine installed on it.
Do not stack products past the limit.
When transporting the module or servo amplifier, never hold the connected wires or cables.
When transporting the servomotor, never hold the cables, shaft or detector.
When transporting the module or servo amplifier, never hold the front case as it may fall off.
When transporting, installing or removing the module or servo amplifier, never hold the edges.
Install the unit according to the instruction manual in a place where the mass can be withstood.
Do not get on or place heavy objects on the product.
Always observe the installation direction.
Keep the designated clearance between the module or servo amplifier and control panel inner
surface or the module and servo amplifier, module or servo amplifier and other devices.
Do not install or operate modules, servo amplifiers or servomotors that are damaged or that have
missing parts.
Do not block the intake/outtake ports of the servo amplifier and servomotor with cooling fan.
Do not allow conductive matter such as screw or cutting chips or combustible matter such as oil
enter the module, servo amplifier or servomotor.
The module, servo amplifier and servomotor are precision machines, so do not drop or apply
strong impacts on them.
Securely fix the module, servo amplifier and servomotor to the machine according to the
instruction manual. If the fixing is insufficient, these may come off during operation.
Always install the servomotor with reduction gears in the designated direction. Failing to do so
may lead to oil leaks.
Store and use the unit in the following environmental conditions.
Environment
Conditions
Module/Servo amplifier
Servomotor
Ambient
temperature
According to each instruction manual.
0°C to +40°C (With no freezing)
(32°F to +104°F)
Ambient humidity
According to each instruction manual.
80% RH or less
(With no dew condensation)
Storage
temperature
According to each instruction manual.
-20°C to +65°C
(-4°F to +149°F)
Atmosphere
Indoors (where not subject to direct sunlight).
No corrosive gases, flammable gases, oil mist or dust must exist
Altitude
According to each instruction manual
Vibration
According to each instruction manual
When coupling with the servomotor shaft end, do not apply impact such as by hitting with a
hammer. Doing so may lead to detector damage.
Do not apply a load larger than the tolerable load onto the servomotor shaft. Doing so may lead
to shaft breakage.
Содержание LD77MH
Страница 2: ......
Страница 48: ...1 16 Chapter1 Outline of Synchronous Control MEMO ...
Страница 84: ...2 36 Chapter 2 Input Axis Module MEMO ...
Страница 104: ...3 20 Chapter 3 Cam Function MEMO ...
Страница 168: ...4 64 Chapter 4 Synchronous Control MEMO ...
Страница 223: ...Appendix 7 Appendices 3 Create the cam data cam No 1 4 Set the synchronous parameter of the axis 1 ...
Страница 234: ...Appendix 18 Appendices MEMO ...
Страница 237: ......