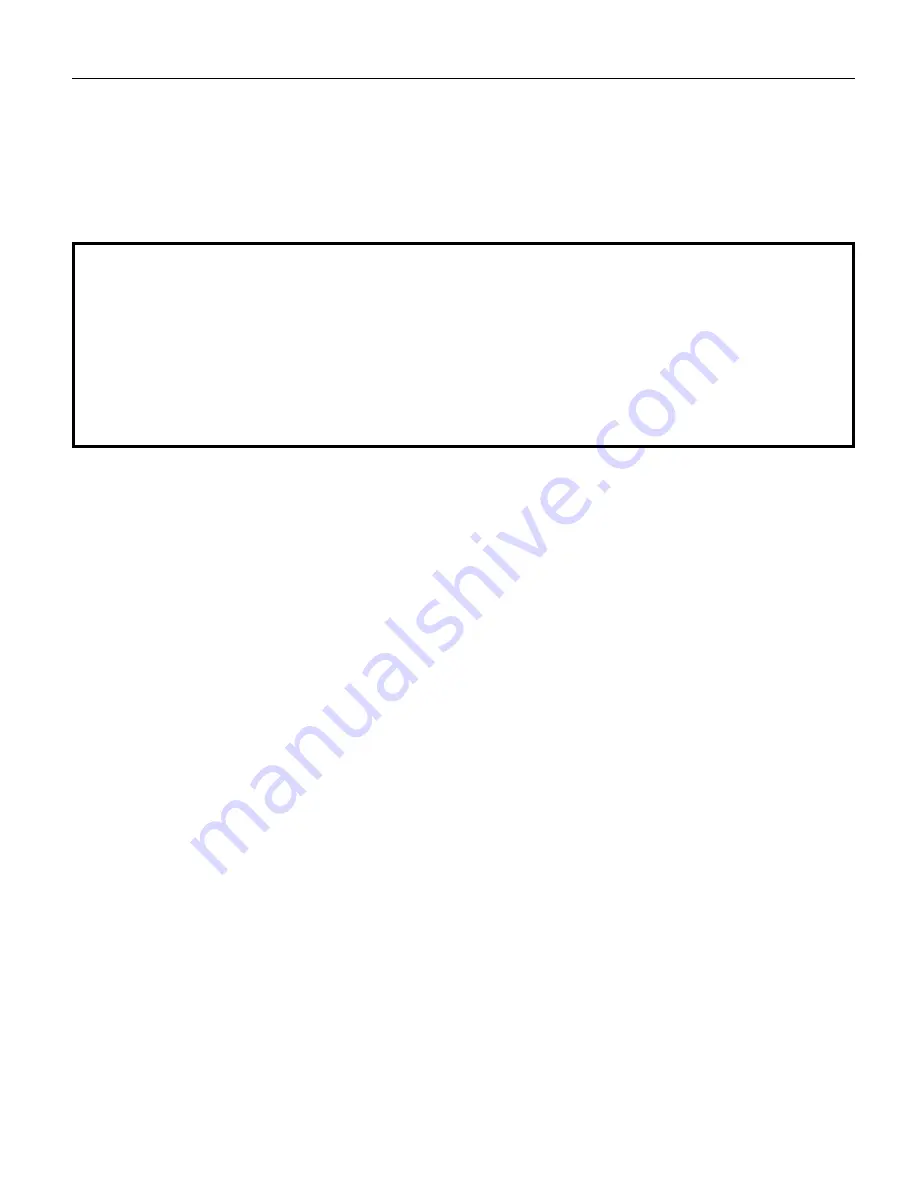
6
Installation
Warning
Do not install, rewire, or remove this control with line
voltage applied. Doing so may cause fire or serious injury.
Make sure you have read and understood the Safety
Warnings before attempting installation.
Mounting
• Drive components are sensitive to electrostatic fields. Avoid
direct contact with the circuit board. Hold drive by the chassis
only.
• Protect the drive from dirt, moisture, and accidental contact.
Provide sufficient room for access to the terminal block and
calibration trimpots.
• Mount the drive away from heat sources. Operate the drive
within the specified ambient operating temperature range.
• Prevent loose connections by avoiding excessive vibration of
the drive.
• Mount drive with its board in either a horizontal or vertical
plane. Six 0.19 in. (5 mm) wide slots in the chassis accept #8
pan head screws. Fasten either the large base or the narrow
flange of the chassis to the subplate.
• The chassis must be earth grounded. Use a star washer beneath
the head of at least one of the mounting screws to penetrate the
anodized chassis surface and to reach bare metal.
250-0281.qxd 4/4/01 11:16 AM Page 6
Содержание NRGD-4Q Series
Страница 9: ...vii Regenerative Drives Figure 1 Four Quadrant Operation...
Страница 12: ...x Notes...
Страница 15: ...3 Dimensions Figure 2 NRGD05 Series Dimensions ALL DIMENSIONS IN INCHES MILLIMETERS...
Страница 16: ...4 Dimensions Figure 3 NRGD10 Series Dimensions ALL DIMENSIONS IN INCHES MILLIMETERS...
Страница 17: ...5 Dimensions Figure 4 Heat Sink Dimensions for NRGD10 Series Drives...
Страница 33: ...21 Installation Figure 8 Regen Dump Circuit Connections To NRGD Drives...
Страница 57: ...45 Figure 15 Connection to DLC600 and PCM4 Application Notes Connection to other Minarik devices...
Страница 78: ...Notes...