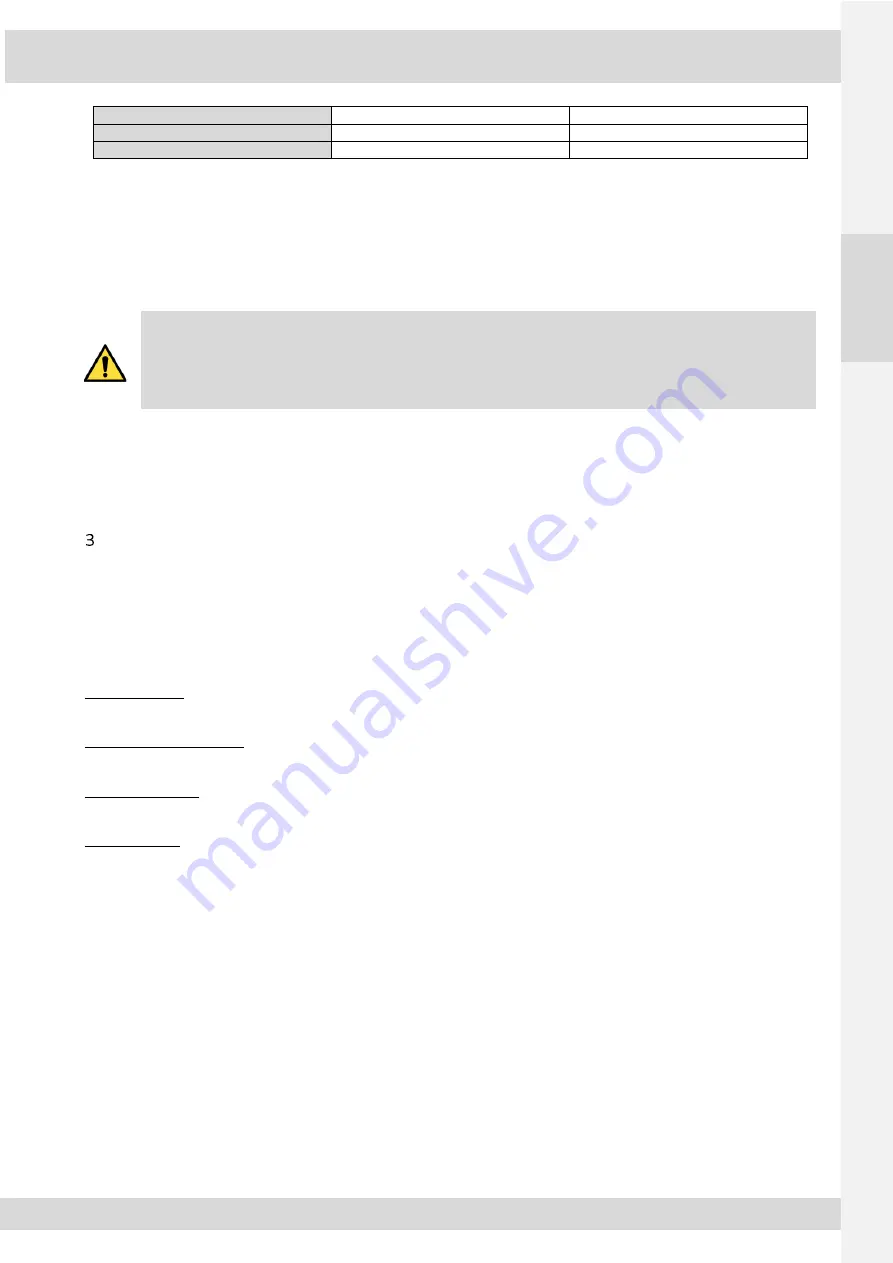
PRO
2
XY OXYGEN CONCENTRATOR
519211-22
5
EN
Oxygen pressure
Hydrocarbon
Particles
Up to 30 bar
≤
550 mg/m²
--
Above 30 bar
≤
220 mg/m²
No particle larger than 50 µm in size
Any modification of the concentrator or its components without MIL'S SAS agreement will mean the specification and purity of the
oxygen produced will not be guaranteed.
2.3
Safety relief valve
When a relief valve with discharge line operates and must be tested, no persons may stand in front of the valve discharge direction.
Not allow discharge toxic, explosive or flammable products, into the atmosphere. Before the test, a controlled discharge procedure
in a confined volume is requested.
Never tamper with the valve, nor remove the lead/manufacturer's seal, nor modify its adjustment pressure.
Not create cold or hot thermal shock on the relief valve.
Make sure that the lead/manufacturer's seal is never damaged.
Maintain the valve clean and in functioning order. Check in particular that the exhaust remains free and that no foreign
body blocks the evacuation piping.
To make sure that the safety valves continue to operate in good working condition, these must be periodically tested.
To do this, open the valve manually using the lever or the test knob; this test must be done while keeping the protected appliance at
a pressure between 80 and 90% of the valve calibration pressure. The valve must open cleanly, and release an abundant amount of
fluid, and must then close fully once the lever has been released or the knob tightened. The operation must be short and performed
just once. When an installation is started, initially perform the test frequently.
SYSTEM DESCRIPTION
3.1
General
The O
2
PRO
2
XY concentrator process is based on the PSA (Pressure Swing Adsorption) procedure. PSA relies on the difference in
affinity of a body with adsorbent as a function of pressure. In fact, the quantity of material adsorbed depends strongly on the relative
pressure in the composite. In this case, it is entirely possible to proceed to a separation of two or more elements by playing on this
difference. Adsorption takes place at high pressure, and desorption at low-pressure. These phenomena are thus exploited in a 4-
stroke cycle using two columns in parallel filled with an adsorbent (molecular sieve):
1
–
Pressurisation
A column is put under pressure (between 5 and 6 bar) from the bottom using compressed air, with the other end being closed.
Nitrogen is mostly trapped in the adsorbent (molecular sieve) and the adsorption front moves in the feed direction within the column.
2
–
Saturation or production
When the pressure reaches its maximum, the top end of the column is opened. Oxygen (not adsorbed by the molecular sieve) is
collected at exit. During this phase the column is progressively saturated with adsorbed gas as the adsorption front shifts.
3
–
Depressurisation
The valve at the base of the column is opened quickly to provoke a sharp drop in pressure down to atmospheric pressure so as to
catch or desorb the gas that was adsorbed by the molecular sieve during the first two phases.
4
–
Regeneration
The column is then purged in the opposite direction using an oxygen-rich mixture from the second column so as totally to evacuate
any impurities from the end from which the desired pure oxygen will emerge.
From ambient air made up of 78% nitrogen, 21% of O
2
and 1% argon, the PRO
2
XY concentrator is able to provide a 95% oxygen
concentrate with the remainder being mainly made up of argon. CO content is less than 2 ppm, CO
2
content is less than 10 ppm and
hygrometry is less than
–
65°C
Note: it is necessary that the "primary material" - i.e., compressed air - be of good quality (see §6).
Содержание PRO2XY
Страница 47: ......
Страница 48: ...www mils fr Plaque de caract ristiques Specification plate...