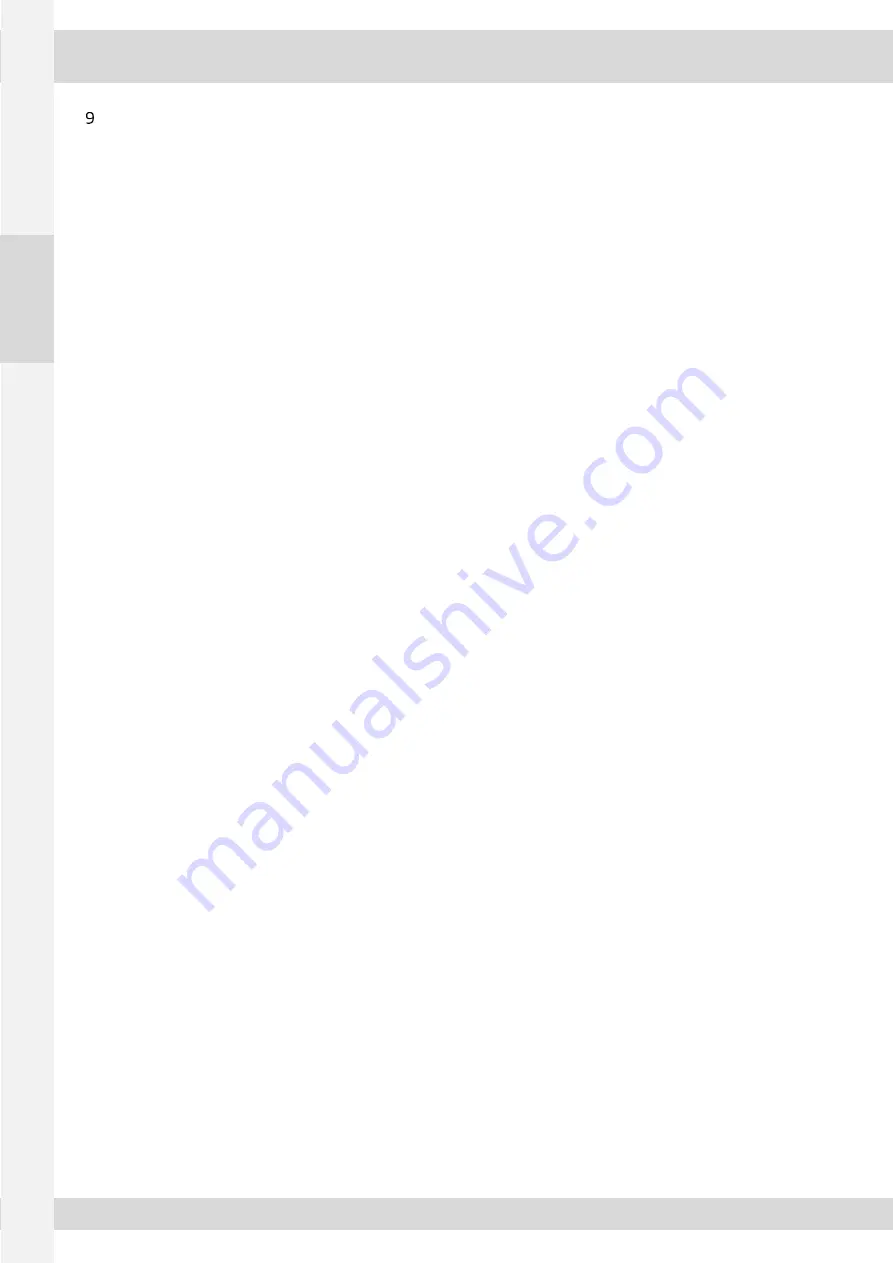
PRO
2
XY OXYGEN CONCENTRATOR
20
519211-22
EN
CONNECTIONS
The connecting hose between the air production unit and the filtration line is supplied by MIL'S company.
The connection between the filtration line, the receiver(s), the concentrator and the final filtration line is the responsibility of the
installer or customer, as well as the power supply of the air production unit and the concentrator.
The following paragraphs describe the requirements that the installer or customer must comply with during installation and
connection, based on the risk analysis.
9.1
Skills, training and qualification requirements
The installer and his employees must be able to demonstrate a good knowledge of medical gases, their use and the associated risks.
This level of knowledge may be justified by initial training, additional training programs and experience.
Personnel working on this project must be able to prove, at all times, that they have the required regulatory qualifications and
certifications (electrical authorisation in particular).
It is imperative that the installer:
➢
qualifies its brazing personnel in compliance with the requirements of the
ISO 13585
standard,
➢
describes its brazing procedures in accordance with
EN 13134
standard,
➢
keeps records of personnel qualifications and operating procedures for at least 15 years. These registrations must be
available on request from MIL' S, the competent authorities and the manufacturer's notified body.
9.2
Start of work
Work cannot begin without the issuing of a Work Authorization from the operator.
If a network shutdown is necessary, the sub-contractor MUST follow the shutdown procedure in effect in the establishment. The
shutdown cannot be carried out unless the operator has issued a switch-off authorisation.
The sub-contractor must comply with the health care establishment's hygiene and cleanliness requirements, particularly when
operating in sterile and/or patient occupied areas. Particular attention will be paid to the risk of bio-contamination of equipment or
components.
Before installing each component, the sub-contractor must check its integrity, its level of cleanliness and, if necessary, the expiry
date. All components which have damaged packaging must be discarded.
The sub-contractor must be particularly vigilant, when working near production sources, regarding the possible automatic restart of
rotating machines (remote or autonomous controlled starting).
Lockout devices must be used when working on electrical control panels.
All components used must be oxygen-compatible and delivered clean, in accordance with the requirements of
NF EN ISO 15001
standard.
9.3
Optional receiver
If the operator takes charge of supplying the storage receiver, it must be adapted to the nominal working pressure of the installation
and must bear the CE marking in accordance with directive
2014/68/EU
(pressure equipment) or
2014/29/EU
(single pressure
vessels).
The tank must be equipped with:
➢
one or several sectional valves,
➢
a CE marked safety valve in compliance with directive
2014/68/EU
(pressure equipment),
➢
a pressure gauge,
➢
a drain valve.
9.4
Pipes, flexible hoses and fittings
The rigid pipes must be made of copper in compliance with standard
NF EN 13348
.
The pipe diameters must be identical to the inlet/outlet diameters of the elements to be connected. The piping, of a diameter less
than 32 mm (diameter 1’’1/4 maximum) is, in the meaning of directive
2014/68/UE
, classified in the meaning of article
4.3
.
The fittings used to connect the copper pipes must be compliant with
EN 1254-1
and
EN 1254-4
.
If low pressure connecting hoses are used, they must be in compliance with standard
NF EN ISO 5359
.
All the components used must be delivered clean, protected from all contamination before and during the installation.
In addition, they must be oxygen-compatible in compliance with the requirements of
NF EN ISO 15001
Furthermore, the components and materials must be able to withstand 1.5 times the operating pressure for the compressed gases.
Proof of the maintaining of the pressure of the piping and components used must be presented by the installer on request from MIL'
S Company, the Competent Authorities and the manufacturer's notified body.
The storage and handling conditions must ensure the product preservation and of its level of cleanliness, until the final assembly.
The cutting of piping intended for the distribution of compressed medical fluids must be
EXCLUSIVELY
done with a pipe cutter in
order to limit the risk of introduction of shavings or particles.
The installation of the piping must be done according to Professional Standards and must meet the applicable requirements of section
§ 11.1
of
NF EN ISO 7396-1
standard.
The pipe supports must be compliant with the requirements of section
§ 11.2
of
NF EN ISO 7396-1
standard.
All the components of the network must be connected to a ground connector in compliance with the regulations in effect.
The pipes must be protected against all physical damage.
Содержание PRO2XY
Страница 47: ......
Страница 48: ...www mils fr Plaque de caract ristiques Specification plate...