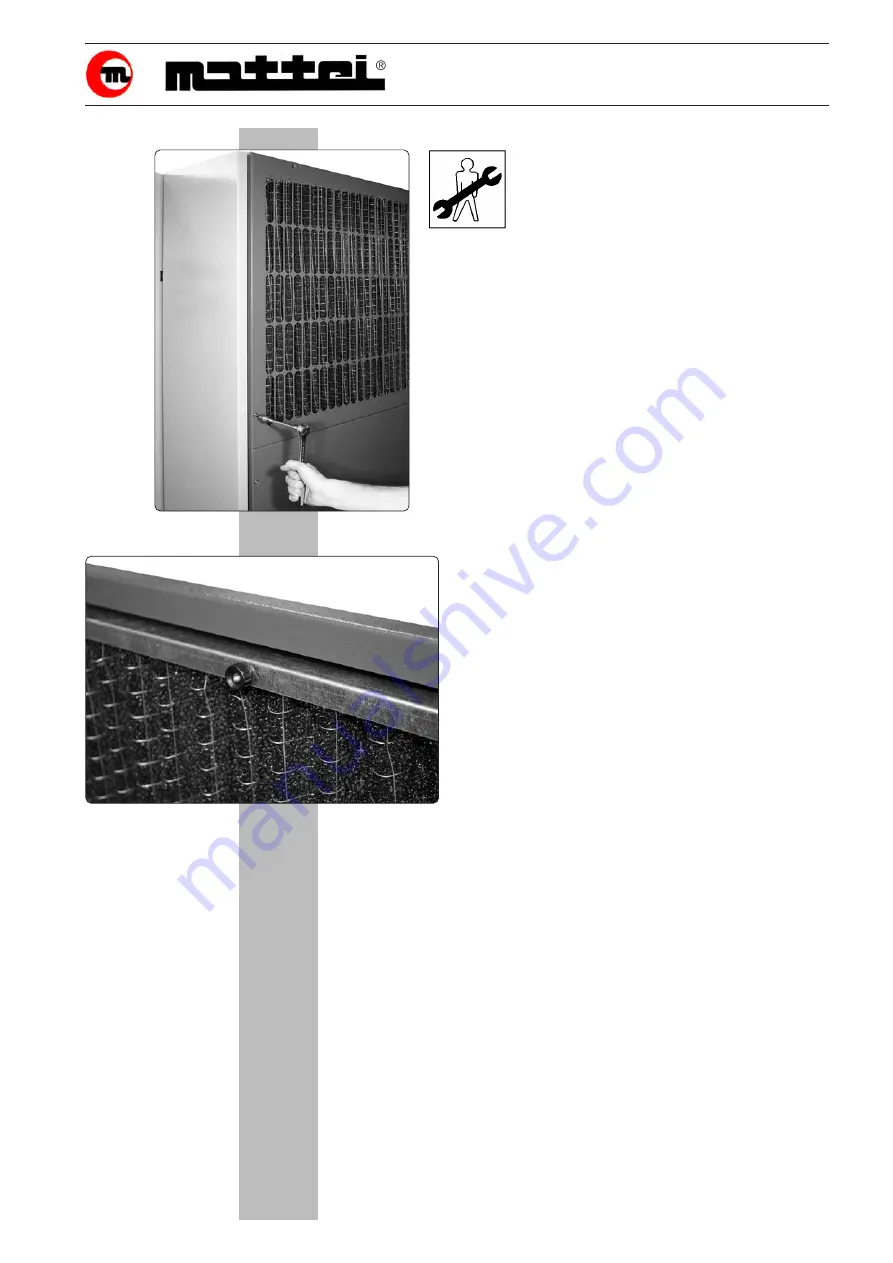
TI008G0001
7.04
Maintenance
Cleaning the prefilters
The machine is equipped with a prefilter
to remove dust and is articulated by the
intake air.
The prefilter is composed of a metal frame contai-
ning a filtering wire mesh.
It slides on metal guides in the side panel and
should be removed from its housing for
replacement or cleaning purposes.
It filters the intake air and washes the compressor
while preventing foreign particles from entering the
machine.
Frequent cleaning of panels is essential.
To do this, open the door through the fixing lock,take
out the panel and blow out with compressed air.
The synthetic material can be washed whenever
necessary.
No solvents should be used for the washing.
225
224
101