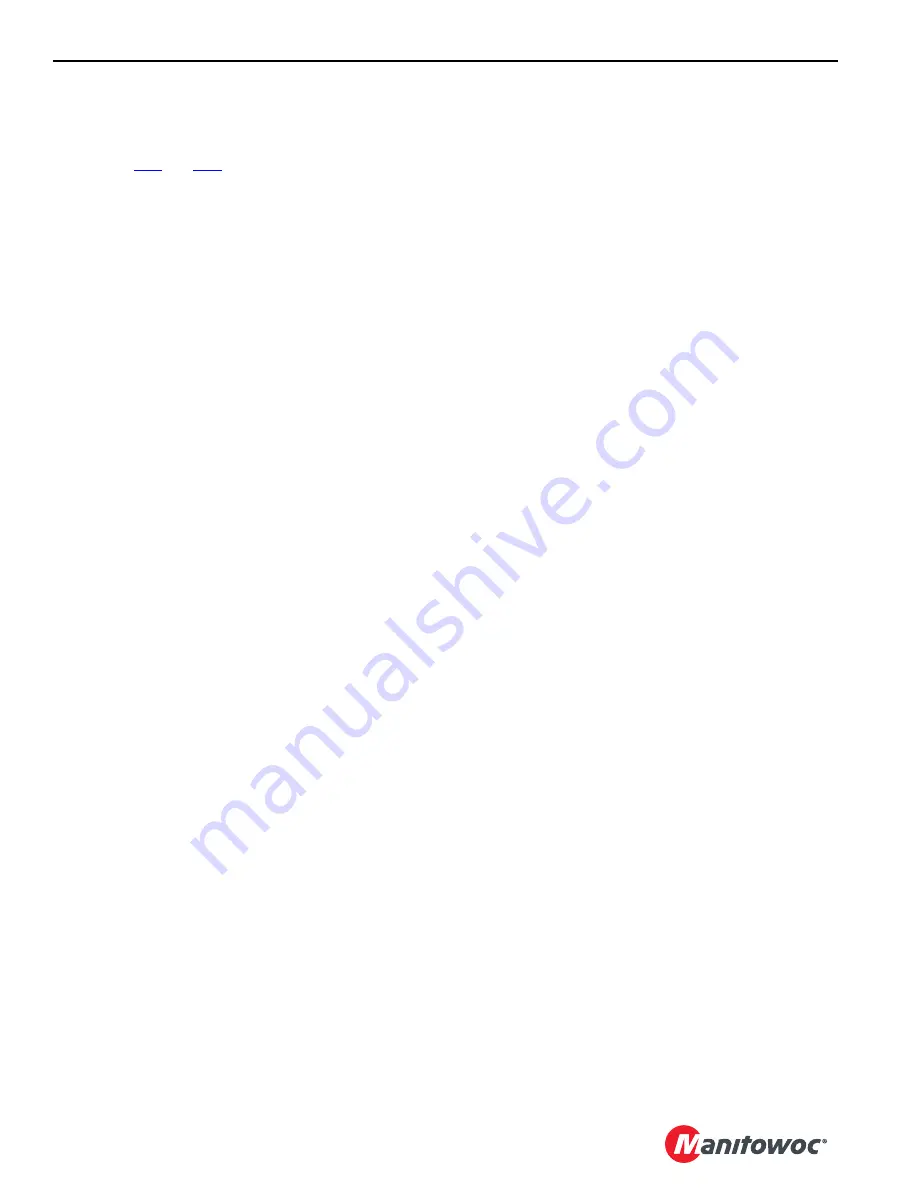
Reference
Only
INTRODUCTION
18000 SERIVCE/MAINTENANCE MANUAL
1-54
Published 12-05-17, Control # 035-23
MAST HOIST DRUM 5 SYSTEM
Mast Hoist System Components
See Figures
The live mast is rectangular shaped structure that supports
the main mast. The live mast is also used for crane assembly
and disassembly.
Mast raising cylinders are required to raise the live mast to a
working position of 114° to 160°. In crane Setup mode, live
mast-raising sequence is controlled automatically by the
computer program and the mast hoist control handle. Mast
raising and lowering rate is controlled by engine speed, as it
regulates pay out and haul in of the cable reeving between
mast hoist (Drum 5) and gantry sheaves.
Hydraulic connections between main hoist 2/5 pump and
mast hoist motor forms a closed-loop system that is
controlled with control handle movement and node
controllers. The far right drum control handle on the right side
console operates the mast hoist in Setup mode only. The
mast hoist control handle is inoperable when mast hoist park
brake is applied.
The mast hoist is located on the rotating bed. Main hoist 2
(Drum 2) and mast hoist form a dedicated system where only
one function can be operated at a time.
In Setup mode, main hoist 2/5 pump drives the mast hoist
motor through a diverting valve. The motor drives a drum
shaft that is connected to a gearbox. Drum 5 diverting
solenoid valve remains open to drum 5 motor until another
mode is selected.
A pressure sender in high-pressure side of system provides
system pressure information to node-1 controller. A fixed
orifice between pump ports A and B allows for smoother
drum operation.
Continuous changing of fluid occurs through leakage in
pump and motor. Fluid from system is dumped into the motor
case where the fluid returns to tank.
When mast hoist drum motor rotates, a speed sensor at
motor rotor monitors and sends an input voltage to node-1
controller. Node-2 controller sends an output voltage to
rotation indicator in control handle. As drum rotates faster,
the rotation indicator on top of control handle pulsates with a
varying frequency that indicates drum rotational speed.
Mast Hoist Brake and Pawl
Hydraulic charge pressure to operate mast hoist (Drum 5)
brake and pawl is from main hoist 2/5 charge pump.
Hydraulic charge pressure from pump must be above 200 psi
(14 bar) for brake or pawl to retract from drum.
When mast hoist (Drum 5) brake switch is in on - park
position, brake solenoid valve HS-11 is disabled and drum
brake is applied. Mast hoist drum pawl in solenoid valve HS-
12 is enabled to keep pawl applied to mast hoist drum flange.
The pawl in solenoid is open to charge pressure from pump
2/5 to piston end of cylinder to extend pawl to drum flange.
Mast hoist pump does not stroke in response to mast hoist
control handle movement.
When mast hoist (Drum 5) brake switch is placed in off - park
position, brake remains applied to drum until node-6
controller sends a 24 volt output to brake solenoid valve HS-
11 to release brake. Node-6 controller sends 24 volt output to
enable drum pawl out solenoid valve HS-13 in the out
direction. The pawl out solenoid shifts to block drain port and
opens charge pressure port from pump 2/5 to rod end of
cylinder to retract pawl from drum flange. Mast system circuit
is active, waiting for a control handle command.
Mast Raising Cylinders
The mast raising cylinders can be manually operated with
controls on the hand-held radio remote control for extending/
retracting mast cylinders without rope rigging. Power is
available to hand-held radio remote control when Setup
Remote mode is selected, engine is running, and power
button is pressed.
Hydraulic pressure to operate mast-raising cylinders is from
accessory pump. Node-1 controller monitors system
pressure to control accessory system proportional relief
valve setting. Mast raising cylinders proportional directional
control valve is “motor spooled” where both cylinder ports
and tank port of the valve spool section are connected in
center position. This type of spool prevents premature
opening of load equalizing valves. Load equalizing valves
ensures mast-raising cylinders operate in unison, protecting
mast from structural damage caused by twisting. Load
equalizing valves also provide support resistance against
mast to ensure control of the unit while rotating it at
assembly.
When mast cylinders switch is placed in the extend position
and held, an input voltage from Setup Remote is sent to
node-1 controller. Node-4 controller sends a 24 volt output to
enable mast raise cylinders solenoid valve HS-33.
When mast cylinders switch is placed in the retract position
and held, an input voltage is sent to node-1 controller. Node-
4 controller sends a 24 volt output to enable to mast raise
cylinders solenoid valve HS-34.
Mast Hoist Raising from Transport Position
The following drum lowering operation is for mast hoist
(Drum 5) while raising from transport position 0° (mast
lowering) to 160°. Node-4 controller monitors the mast angle
sensor in Setup mode.
When Setup mode is selected, Node-4 controller sends a 24
volt output to drum 5 diverting solenoid valve HS-14 to shift
solenoid valve and apply hydraulic pressure to shift diverting
Содержание 18000
Страница 1: ...R e f e r e n c e O n l y Service Maintenance Manual Manitowoc 18000 ...
Страница 2: ...R e f e r e n c e O n l y ...
Страница 4: ...R e f e r e n c e O n l y THE ORIGINAL LANGUAGE OF THIS PUBLICATION IS ENGLISH ...
Страница 210: ...R e f e r e n c e O n l y NOTES SKETCHES AND PHOTOGRAPHS ...
Страница 315: ...R e f e r e n c e O n l y ...
Страница 316: ...R e f e r e n c e O n l y ...