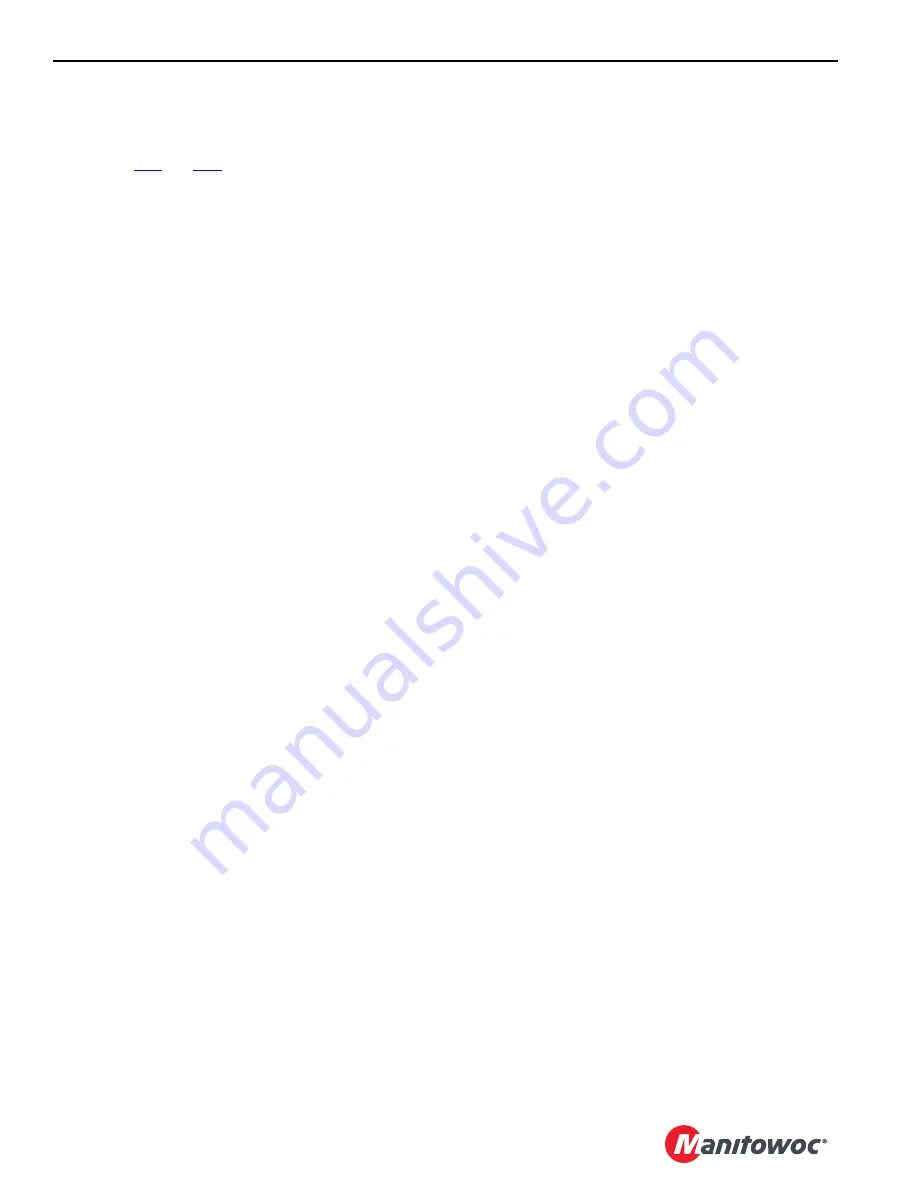
Reference
Only
INTRODUCTION
18000 SERIVCE/MAINTENANCE MANUAL
1-38
Published 12-05-17, Control # 035-23
BOOM HOIST SYSTEM OPERATION
Boom Hoist System Components
See Figures
Two separate hydraulic pumps and motors drive a gearbox
on each end of boom hoist drum (Drum 4). The boom hoist
drum is controlled with the boom hoist control handle
movement and node controllers. Boom hoist control handle
is inoperable when boom hoist park brake is applied. Each
boom hoist drum motor drives a shaft that is connected to a
gearbox.
In Standard mode boom hoist (Drum 4) is controlled with
control handle on left side console. In Luffing Jib mode boom
hoist is controlled with control handle on far right of right side
console, while the luffing jib hoist (Drum 6) is controlled by
control handle on left side console.
Hydraulic charge pressure from left travel charge pump
supplies hydraulic pilot pressure to operate both boom hoist
motor servos. Hydraulic charge pressure from system
charge pumps supplies hydraulic make-up fluid to low-
pressure side of each boom hoist motor. A pressure sender
in one high-pressure side of boom hoist system provides
system pressure information to node-1 controller. There are
equalizing lines between legs A and legs B when two pumps
drive two motors. A fixed orifice between pump ports A and B
allows for smoother drum operation.
When boom hoist motor rotates, a speed sensor mounted at
one motor monitors rotor movement and sends an input
voltage to node-1 controller. Node-2 controller sends a 24
volt output to rotation indicator in control handle. As boom
hoist drum rotates faster, the rotation indicator on top of
control handle pulsates with a varying frequency that
indicates drum rotational speed.
Continuous changing of closed-loop fluid occurs through
leakage in pump, motor, and external sequence/flow valve.
Sequence/flow valve opens at 200 psi (14 bar) and removes
4 gallons per minute (15 l/m) of hot fluid from system by
dumping the fluid into the motor case where fluid returns to
tank.
Boom Hoist Brake and Pawl
Hydraulic pressure to operate boom hoist brake is from low-
pressure side of boom hoist system. A electrical motor
operates the boom hoist drum pawl.
When boom hoist brake switch is in on - park position, boom
hoist brake solenoid valve HS-6 is disabled to apply brake to
drum. Boom hoist electric drum pawl in relay K1 is enabled to
keep pawl applied to boom hoist drum. Boom hoist pump
does not stroke in response to boom hoist control handle
movement.
When boom hoist brake switch is placed in off - park position,
boom hoist brake remains applied to boom hoist drum until
node-6 controller sends a 24 volt output to brake solenoid
valve HS-6 to release brake. Node-6 controller sends 24 volt
output to enable boom hoist pawl electric motor K2 relay in
the pawl out direction. Boom system circuit is active, waiting
for a control handle command.
Boom Hoist Raise
When boom hoist control handle is moved back for booming
up
, an input voltage of 2.4 volts or less is sent to node-1
controller. Node-5 controller sends a variable zero to 24 volt
output that is divided by a resistor and applied to each boom
pump EDC. Node-6 controller sends a variable zero to 24
volt output that is divided by a resistor and applied to each
boom hoist motor PCP. Node-1 controller checks that boom
up limit switch is closed and no hydraulic system fault is
present.
Each pump EDC tilts swashplate in the
up
direction to satisfy
pressure memory. Node-1 controller compares boom hoist-
holding pressure to value in pressure memory. When system
pressure is high enough, node-6 controller sends a 24 volt
output to boom hoist brake solenoid valve HS-6. The brake
solenoid shifts to block drain port and opens port to low-
pressure side of boom hoist system to release boom hoist
drum brake.
Each pump EDC continues to tilt swashplate in the up
direction as hydraulic fluid flow is from pump ports to motor
ports. Return fluid is from motor outlet ports to pump inlet
ports.
Node-5 controller output voltage to each pump EDC and
node-6 controller output voltage to each motor PCP is
relative to control handle movement. As boom hoist control
handle is moved back, pump swashplate angle is increased.
When system pressure exceeds the PCOR (Pressure
Compensating Over-Ride) valve setting of 4,930 psi (340
bar), the valve shifts to direct flow from shuttle valve into
maximum displacement side of servo cylinder. The PCOR
valve over-rides the command from servo PC valve,
increasing motor displacement and output torque and
reducing output speed. When PCOR valve closes, control of
the motor returns to servo PC valve.
Node controllers are continuously balancing the system
pressure and the motor displacement angle so the motor
displacement goes to minimum when control handle is fully
back, if the motor torque requirement is not too high. Node-6
controller monitors motor displacement and controls motor
speed by regulating the hydraulic fluid flow through the
pumps.
When boom hoist control handle is moved to neutral
position, node-1 controller compensates for hydraulic
system leakage or changing engine speed. Node-5
controller sends a zero output voltage to each boom hoist
pump EDC that moves swashplate to center position. This
shifts the motor back to maximum displacement for slower
output speed to slow the drum rotation. The controller stores
Содержание 18000
Страница 1: ...R e f e r e n c e O n l y Service Maintenance Manual Manitowoc 18000 ...
Страница 2: ...R e f e r e n c e O n l y ...
Страница 4: ...R e f e r e n c e O n l y THE ORIGINAL LANGUAGE OF THIS PUBLICATION IS ENGLISH ...
Страница 210: ...R e f e r e n c e O n l y NOTES SKETCHES AND PHOTOGRAPHS ...
Страница 315: ...R e f e r e n c e O n l y ...
Страница 316: ...R e f e r e n c e O n l y ...