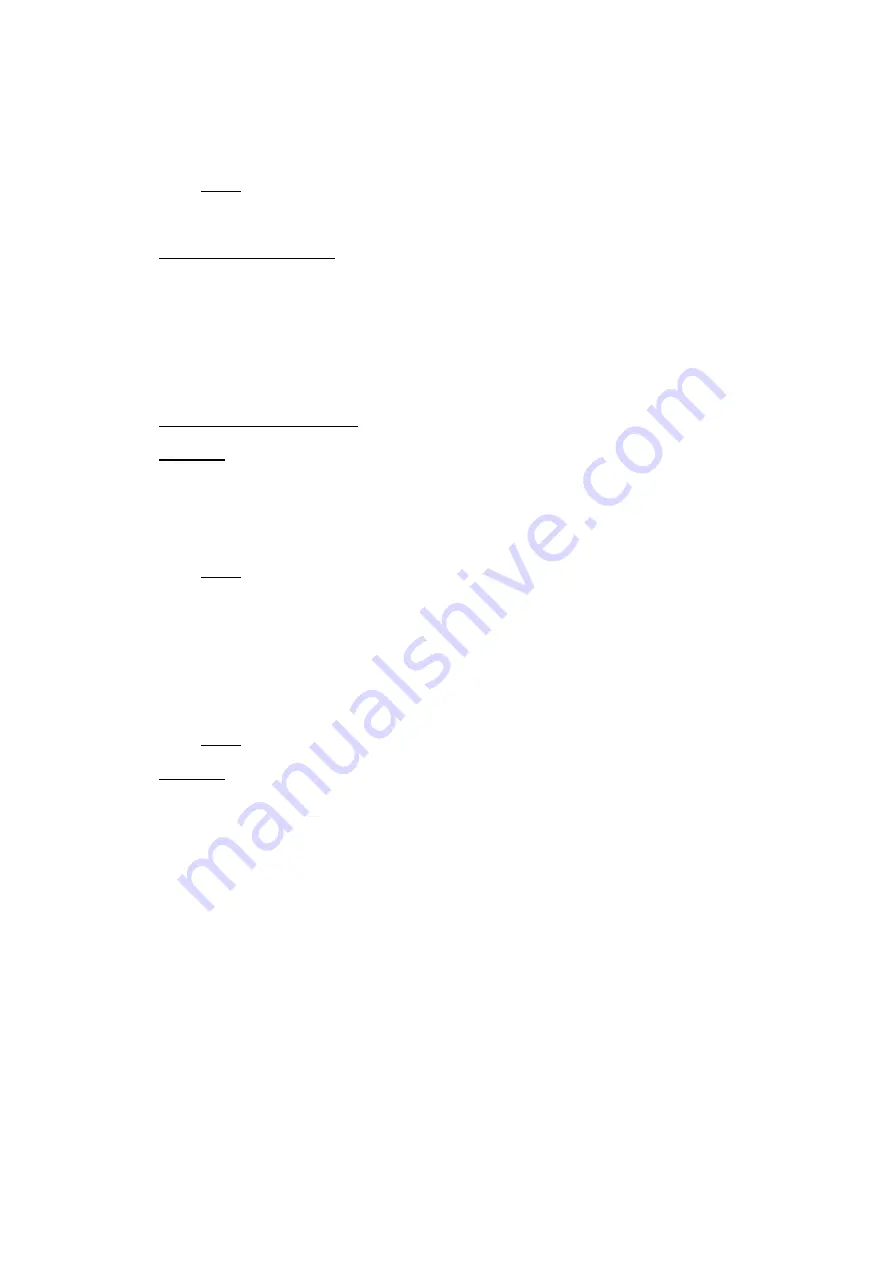
L'HOTELLIER
COMPONENT MAINTENANCE MANUAL
12589-( )
PRINTED IN FRANCE
26-20-50
Page 6002
APR 01/11
NOTE : The applicable thread sizes are given in DESCRIPTION AND OPERATION section,
Table 1, Specified Data.
TASK 26-20-50-300-803-A01
4. Container
External
Surface
A.
Use 320 grit minimum sandpaper to remove any scratches and gouges in the permitted limits
specified in CHECK section.
B.
After the repair is complete, do the minimum wall thickness check and hydrostatic test specified
in TESTING AND FAULT ISOLATION section.
TASK 26-20-50-300-804-A01
5.
Pressure Switch Fitting Flange
CAUTION :
DO NOT REPAIR THE FITTING IF THE BOSS IS MACHINED BELOW DIA 24 MM
(0.94 In – 24mm ). RETURN THE CONTAINER TO THE MANUFACTURER FOR
REPAIR.
A.
The flange of the fitting can be damaged or unusable after many removals of the pressure
gauge. This procedure gives instructions to replace the flange on the gauge fitting.
NOTE : This repair is NOT necessary if the flange has a diameter of DIA 24 mm (0.94 in) or
greater.
(1) Disassembly the container to the level necessary to do the repair (refer to DISASSEMBLY)
(2) Put protection caps on the outlets to protect the closures
(3) Install an applicable aluminium plug in the fitting. The plug will keep unwanted materials out
of the container and is also a heat sink
NOTE : Install the plug so there is sufficient clearance to machine the fitting
CAUTION :
MAKE SURE THAT THE CONTAINER IS CORRECTLY HELD BEFORE YOU REPAIR
THE FITTING. THIS WILL PREVENT DAMAGE TO THE CONTAINER,EQUIPMENT,
OR INJURY TO PERSONS.
(4) Machine the flange of the fitting to the tolerances given in figure 6001 with the vertical milling
machine and a fly cutter
(5) After you machine the flange, remove the cutting oil from the external surface of the
container with alcohol
(6) Make a new flange washer with the dimensions and materials given
(7) Put the new “washer” flange on the machined pressure gauge fitting with the chamfered side
up. Make sure that the washer is in the center of the flange.
(8) Use a Tungsten Inert Gas (TIG) welder, set to 25 to 35 amperes maximum, to attach (tack
weld) the washer to the flange in three (3) places.
The document reference is online, please check the correspondence between the online documentation and the printed version.