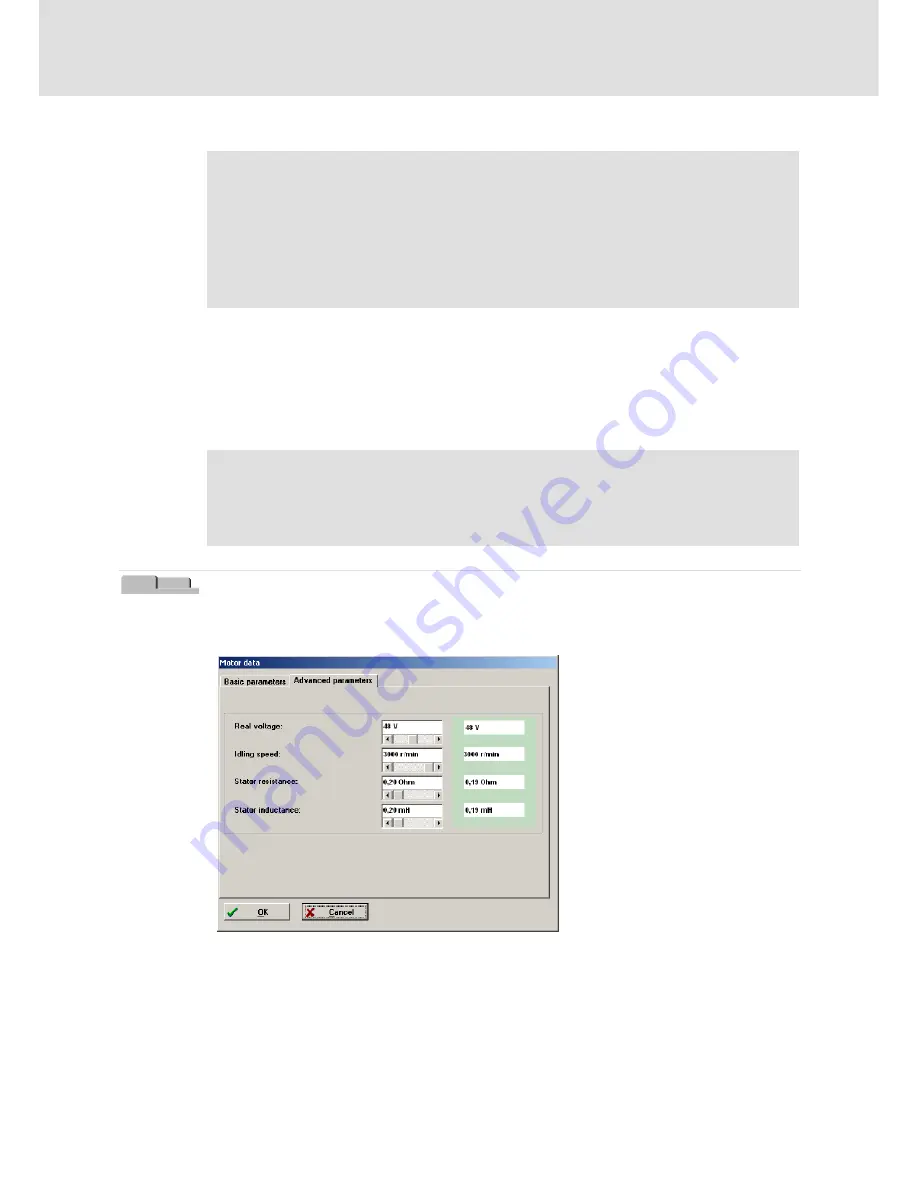
Appendix
Parameterisation of outside motors
Motor data
10
135
SW-HB 13.0002-EN EN 3.0
Stop!
Please observe that the entries for maximum current and rated current are
r.m.s. values!
If the currents are too high, the motor will be destroyed because the
permanent magnets in the motor are demagnetised.
For this reason, the current limits specified by the manufacturer must not be
exceeded.
The maximum current limits may depend on the clock frequency of the power stage. Click
Power stage
to set the clock frequency. For more information, please see the chapter
”Power stage”. (
143).
In addition, you can enter the pole pair number of the motor. Or, you can use the automatic
identificationroutine whichautomatically determines the pole pair number and theoffset
angle of the angle encoder. For this, simply click the
Auto detect
button.
Stop!
Before starting the motor identification, ensure that the current limits (menu
items
Parameters
Device parameters
Motor data
) have been set,
otherwise, the motor may be destroyed!
^Çî~åÅÉÇ é~ê~ãÉíÉêë
Use the A
dvanced parameters
tab to set the parameters required for the calculation of the
motor e.m.f..
931e_278
efesotomasyon.com - Lenze