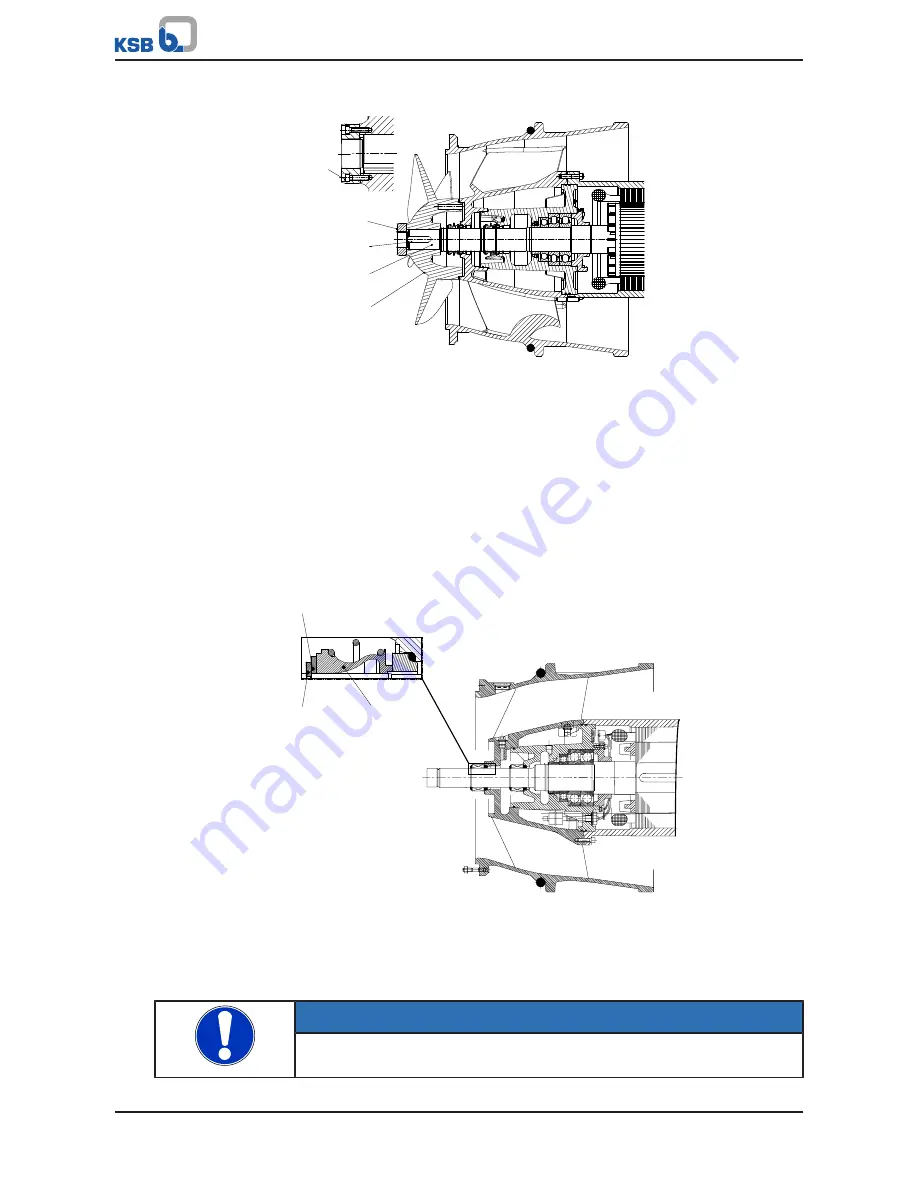
7 Servicing/Maintenance
62 of 132
Amacan P
7.5.4 Removing the impeller
914.07
922
940.02
210
230
Fig. 32:
Removing the impeller
ü
The pump has been placed on wooden supports in a horizontal position and is
protected against rolling off.
ü
The lubricant and leakage have been drained.
1. Undo socket head cap screw 914.07 and impeller nut 922.
2. Pull impeller 230 off shaft 210.
3. Remove keys 940.02 from shaft 210.
4. Protect the shaft thread against damage.
7.5.5 Removing the mechanical seal
7.5.5.1 Impeller-end mechanical seal for pump sizes 700-... to 1200-...
932.44
550.44
433.02
Fig. 33:
Removing the impeller-end mechanical seal
ü
The pump has been securely placed in a horizontal position on wooden supports.
ü
The impeller has been removed.
1. Remove circlip 932.44 and disc 550.44.
2. Pull mechanical seal 433.02 off the shaft.
NOTE
To protect the mechanical seal against damage when pulling it off the shaft placing
a foil (no thicker than 0.3 mm) around the free shaft stub is recommended.
Содержание Amacan P 1000-700
Страница 129: ......
Страница 130: ......
Страница 131: ......
Страница 132: ...KSB SE Co KGaA Johann Klein Stra e 9 67227 Frankenthal Germany Tel 49 6233 86 0 www ksb com 1580 87 08 EN 01137299...