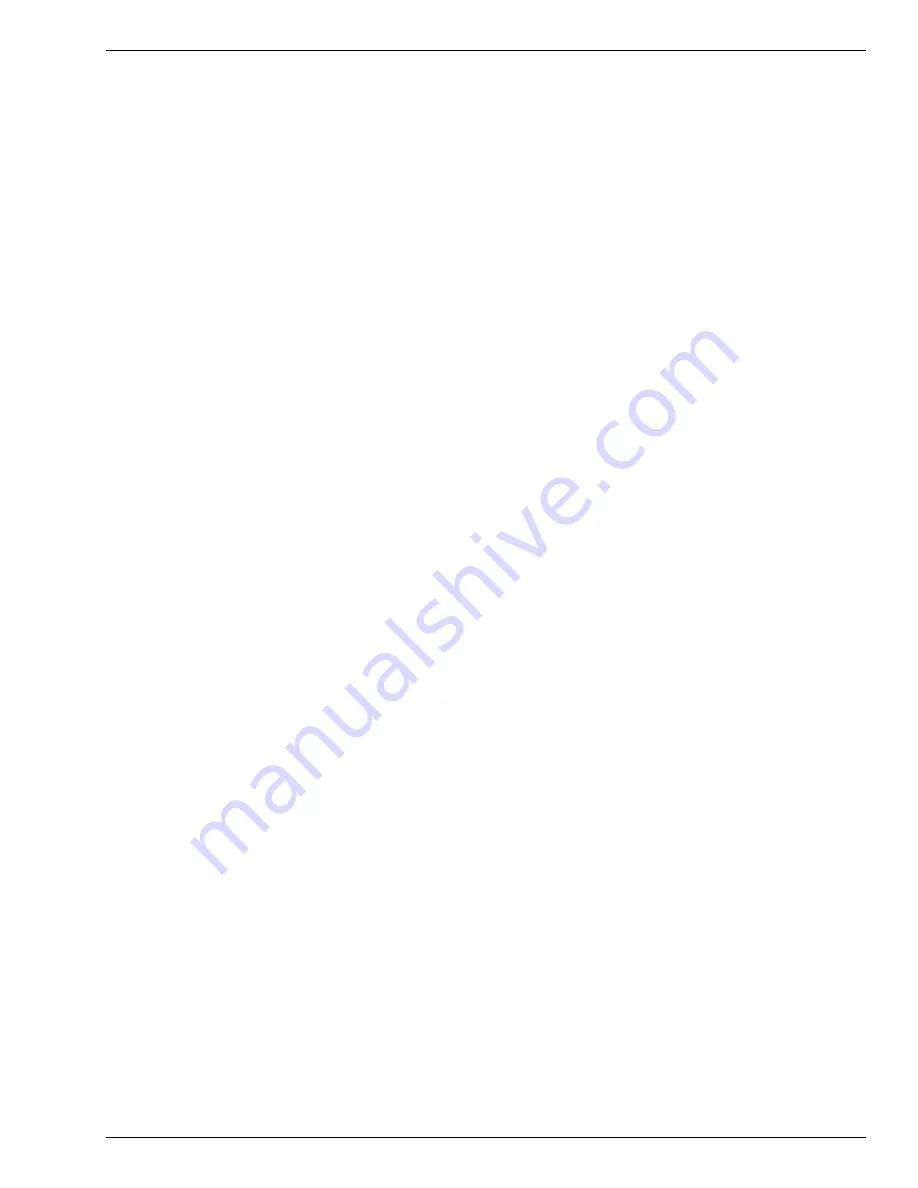
Kollmorgen 4/13/2012
Product
Overview
S200 Position Node Installation Guide
4
2.0 PRODUCT OVERVIEW
The S200 Position Node with CANopen/DeviceNet
TM
brings greater flexibility to the S200 drive platform
by adding profile generation and field bus capabilities. It also brings added I/O, Digital Oscilloscope
emulation, and the ability to use incremental encoder with commutation tracks (ComCoder) for motor
feedback.
The S200 Position Node brushless position node servo drives with CANopen push high performance
servo technology into lower power applications than was previously possible without having to
compromise on reliability or package size. Couple a S200 position node drive with an AKM servo motor
for a complete servo control solution designed to excel in applications such as semiconductor fabrication,
electronic assembly, packaging, medical, and woodworking equipment.
The S200 position node servo drives with CANopen communication are the first all digital industrial drives
with a velocity loop bandwidth up to 400 Hz offering unmatched system throughput and simplified tuning.
High resolution (24 bit) feedback and high performance 3-5 kHz current loop bandwidth provide smooth
motion and rapid start and stop action to optimize machine performance. Smart feedback and industry
leading high bandwidth deliver fast and accurate commissioning by eliminating the need for servo loop
tuning in most applications.
A separate "keep alive" power input allows rapid recovery from emergency stop conditions. Optically
isolated inputs/outputs, positive locking connectors and full fault protection promise long machine life and
immunity to accidental damage. A single motor power/feedback cable simplifies connectivity. All
connectors and LED status indicators are easily accessible from the front of the drive.
H
IGHLIGHTS
DC or AC input voltage:
DC type: 20 V ... 90 V
AC type: 110 V ... 240 V, 1Ø or 3Ø, 50/60 Hz
Highest performance all digital servo in the industry
Operation and Setup via a PC using the S200 OC Tools setup software
Easy set up and tuning with Smart Feedback Device
Optimized performance with Kollmorgen AKM motors
Rugged optically isolated I/O
UL508C recognition, CE (EN50178, EN61800-3)
Very compact footprint
Full fault protection
Velocity, Position, and Electronic Gearing, Step and Direction control
Indexing - 180 unique motion tasks can be defined and initiated via the serial port, Can
Port, or discrete inputs
Jogs, Relative, Absolute, Simple Registration, and Home motion tasks can be easily
setup and executed
Individual motion tasks can be linked or blended with each other
Digital Oscilloscope Functions
Built-in CANopen / DeviceNet Communication bus
Incremental Encoder Input port allows ComCoder motor feedback for position loop
control.