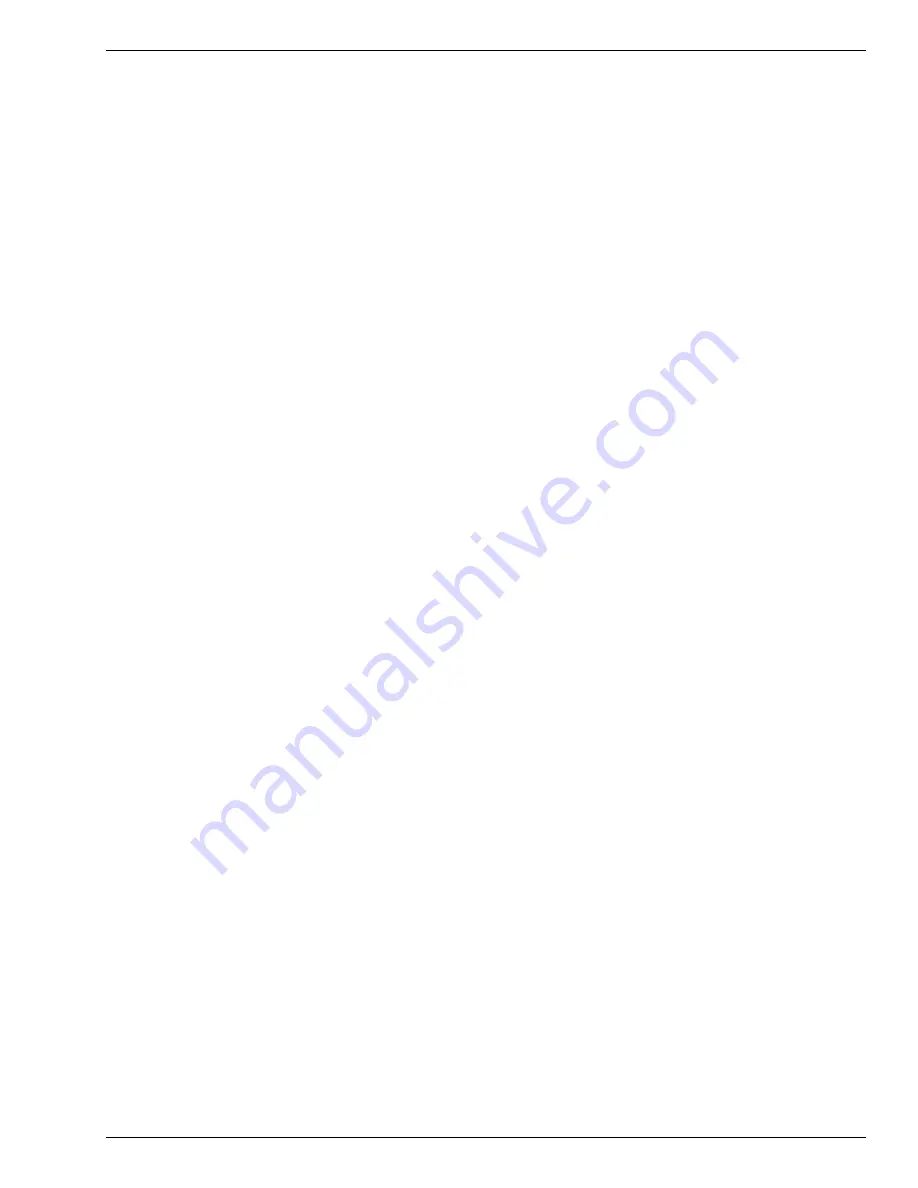
Kollmorgen 4/13/2012
System
Startup
S200 Position Node Installation Guide
52
10.0 SYSTEM STARTUP
The companion S200 Position Node User’s guide has information pertaining to installation and use of the User
Interface Program (GUI) called S200 OC Tools. The following startup recommendations assume that the user has
the GUI installed on the computer for test and setup and that it is appropriately connected via RS232
communications.
10.1 W
IRING
C
HECKS
Before applying any power please double check all wiring for accuracy and quality. Wiring should be done to local
and national wiring standards. In addition please ensure the following:
Earth ground must be connected to all PE terminals and the Screw block on the front of the S200 Position Node.
Signal wires (low voltage) must be separated from power wires (high voltage).
All terminals should be torqued to appropriate specifications
No wire strands should protrude from any connection.
10.2 S
WITCH
S
ETTINGS
The S200 Position Node has several user-settable switches. The function of these switches are defined in the
S200 Position Node User’s Guide. Default settings of these switches will support the installation and startup
procedures in this document. These switches affect CANbus baud rate, Modbus and CANbus address
assignment, and encoder equivalent output resolution. If the user finds any of these to be adjusted as part of a
comprehensive startup procedure then the S200 Position Node User’s Guide should be referenced at this time.
10.3 A
PPLY CONTROL
P
OWER
Apply control power only to the S200 Position Node. Note the following:
1.) The green status LED to the left of J5 should flash at 2 Hertz (500ms on / 500mS off).
2.) The 7 Segment display should flash a sequence indicating the drive model number. For example, an
S20360 drive will flash ‘b’-‘S’-‘2’-‘0’-‘3’-‘6’.
3.) That flash should be followed by a steady ‘d’ in the display indicating that the drive is disabled.
A display of anything other than described above is probably a recognized fault condition. See the S200 Position
Node User Guide for further information pertaining to fault and corrective actions.
If an AKM motor with SFD feedback is used nothing more need be done at this time. If an encoder based motor is
intended to use the commutation encoder for feedback then the startup process must continue with the following
encoder checks:
1.) The importance of the position feedback counting up for motor shaft CW (Looking at the load-end of the
motor) is extremely important. Do not proceed if this is not the case.
2.) Under the S200 OC Tools GUI select the Motor and Mechanical \ Feedback form. Select the Feedback
type as COMCODER. Enter the encoder line count. Go back to the status screen and note the Position
Feedback number. Rotate the encoder (motor) one revolution CW. The new Position feedback number
should be approximately equal to the previous feedback position plus 4 times the encoder line count.
3.) Since the AKM with SFD feedback device automatically loads all the motor parameters but is not present
on these systems, all motor data sheet parameters must be manually entered using the S200 OC Tools
GUI. Under the Motor and Mechanical Setup \ Motor tab: Search the Motor selection box to see if your
motor is located in the GUI database. Select it if it is and the correct settings will be loaded. If the motor
does not exist than it must be manual entered using the Utilities\Motor Database Editor menu. Select ‘
New Motor, enter the data, then Add. Exit the database and return to the Motor and Mechanical Setup \
Motor form and select the newly added motor.