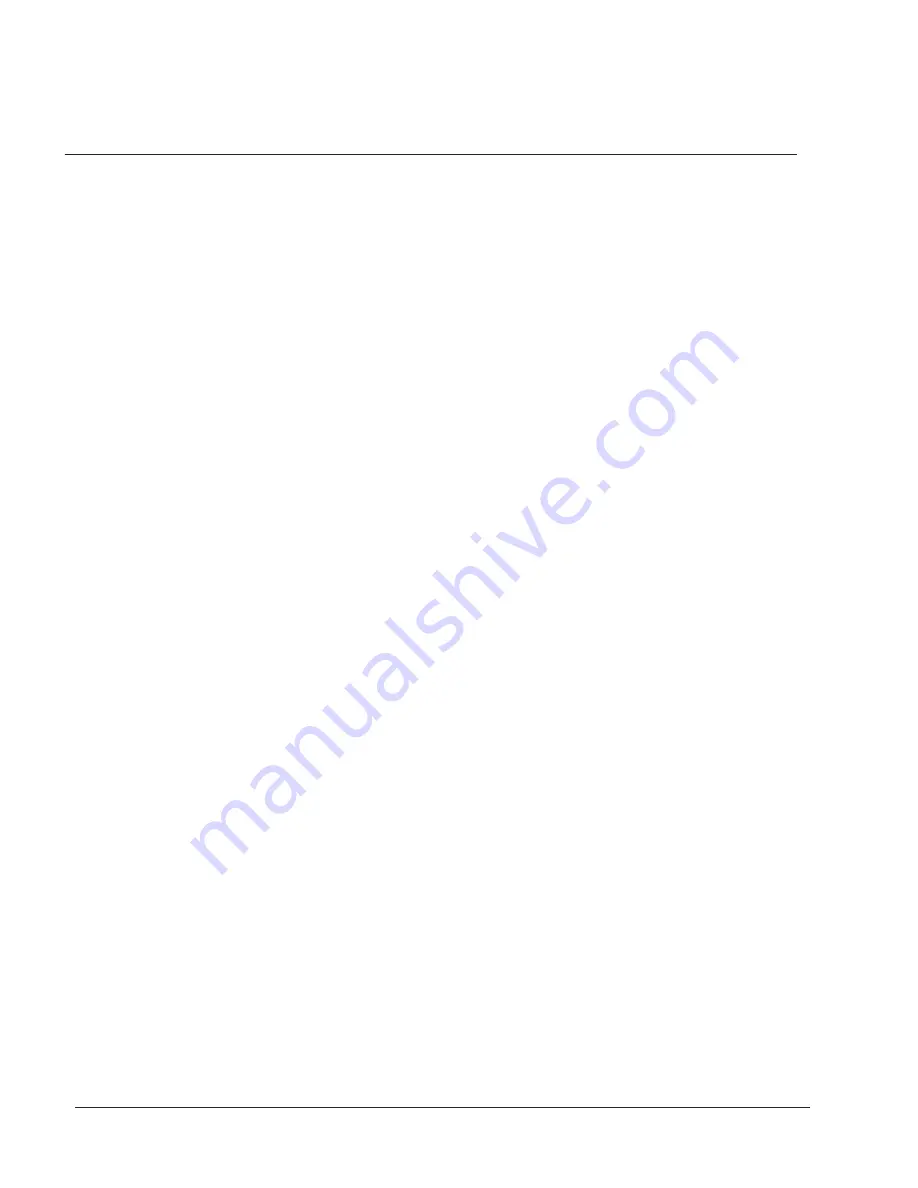
%
YORK, A Johnson Controls Company
$$&G %
YORK Solution AirMod and Solution XTO VFD Start-Up Checklist
A. Reference Material
1.
AYK550 Installation and Operation Manual,
YORK Form 100.41.03 ....................................................................
2.
Wiring schematic located inside panel door. ....................................
B. Pre-Installation Checks
1.
Verify drive model number and nameplate data to what was
ordered. ............................................................................................
2.
Verify voltage being applied is the same for:
a.
Drive Package ............................................................................
b.
Power Line .................................................................................
c.
Motor being operated by the drive .............................................
3.
Record Motor Data to use in Group 99
a.
Voltage: 208, 230, 380, 460 ......................................................
b.
Frequency: 50 Hz, 60 Hz ...........................................................
c.
Motor full-load current:
_____ FLA ......................................
d.
Motor full-load speed:
_____ RPM ....................................
e.
Motor power (HP x .746) _____ kW or HP .............................
4.
Verify the drive output current FLA is equal to or greater than the
motor(s) being driven by it. ................................................................
5.
Check Motor Wiring.
a.
A disconnect (if supplied by others) between the drive and
motor should be interlocked to the drives safety interlock to
prevent nuisance tripping. .........................................................
b.
Do not apply power factor correction capacitors between the
drive output and the motor. ........................................................
c.
Two-speed motor must be wired permanently for full speed. ......
d.
Y-Delta motors must be wired permanently for RUN. ...............
e.
Part winding motors must be wired permanently for RUN. .......
f.
Verify all motor lead connections are tight and wire insulation is
not nicked or cut. Loose connections or cut wire insulation can
cause overcurrent or ground fault trips in the drive. ..................
C. Installation Checks
1.
Branch circuit protection must be provided for the drive. Drive
package with bypasses that come with an integral main fused
disconnect are sized to protect the drive package on circuits
suitable of not more than 100,000 amps rms at 480VAC max. ........
2.
Environmental Concerns
a.
Clean: Keep construction debris out of drive and/or cabinet.
b.
Dry: maximum 95% relative humidity noncondensing ................
c.
Cool: 32
°
F - 104
°
F Ambient temperature. (Solution XTO drives
are N3R outdoor weatherproof and have factory cooling
provisions from the AHU). Confirm air flow into cabinet. ...........
d.
Elevation: 3300 feet above sea level w/o derate ......................
e.
Warm: If the AirMod is to operate below 32
°
F, install an
enclosure ambient space heater. ..............................................
3.
Mounting
a. N1 AirMods are wall-mounted or AHU mounted, vertical
with 4" space required on sides and top for cooling. .......................
b. N3R Solution XTOs are AHU factory-mounted for outdoor
applications. ..................................................................................
c. Solution styles are AHU factory mounted. ...................................
4.
Wiring
a.
Separate grounded metal conduits must be provided for
input power, output power, and control wiring. Failure to
provide separate conduits could result in disruption of
other electrical devices due to harmonics and RFI/EMI
generated by the drive. ...........................................................
b.
On Solution XTO and AirMod drives with bypasses, the
interlock and remote run commands are at 120VAC potential.
See wiring diagram in drive enclosure for connection detail. ....
c.
Use conduit knockouts provided. Avoid metal shavings in the
drive enclosure. ..........................................................................
d.
Protect signal wires from noise. Be sure to use shielded and
properly grounded signal wires. Noisy input signal wires can
cause erratic drive operation. ....................................................
e.
Ground each drive package individually. ...................................
f.
Double check input and output wiring for correct
termination. ...............................................................................
g.
Double check all electrical connections. Loose wiring can
cause nuisance tripping, over current trips, single phase
trips, and component failure. .....................................................
h.
Safeties and remote run command must be wired as indicated
on wiring diagrams. ....................................................................
i.
On drive only applications, all connections must be dry
contact connections on the drive logic board. ...........................
j.
A 0-10VDC or 4-20mA remote speed signal must be
wired onto AI1 and AGND on drive logic board. ..................
k.
Configure speed signal using dip switches on logic board. ......
5.
Programming
Apply power to drive. .........................................................................
a.
Drives are preprogrammed for YORK defaults and the HVAC
Hand-Auto Macro. Only minimal field programming is required. .
b.
Using the soft keys of the Keypad, verify or change as required
the following parameters on page 17. .......................................
6.
Operational Test
(Before proceeding, confirm system is safe to run at full speed.)
a.
Toggle VFD-OFF-Bypass to VFD. Press HAND Key on
AYK550 panel, use the up/down keys to increase speed.
Verify rotation of fan/motor. If fan/motor is running backwards,
power down drive by opening disconnect and change U
2
and V
2
at drive output motor leads .........................................................
b.
Check fan/motor rotation in bypass mode by “bumping” motor
using VFD-OFF-Bypass Switch. If fan/motor is running
backwards in bypass mode, remove power from AirMod by
opening disconnect and change L
1
and L
2
at incoming
disconnect switch. ......................................................................
c.
Once rotation has been verified in both VFD mode and
Bypass mode, place the AirMod in VFD mode and verify
operation in “HAND AND AUTO” mode using the AYK
keypad. The drive will follow an external speed reference
when placed in Auto mode and will follow speed commands
from the keypad up/down arrows while in Hand mode. Use
the Hand mode to ramp up the fan/motor to full speed.
During ramp up, check for system vibration or resonant
points. See Group 25 to program critical skip frequency. ......
d.
At full speed and load, measure drive input voltage and
output voltage between phases, a voltage balance of less
than 5V per phase is desired. Measure drive input and
output current between phases, a current balance of less
than 5% per phase is desired. ..................................................
e.
After the above steps are performed, the drive can be placed
in AUTO mode for normal remote operation. ..........................
❏
❏
❏
❏
❏
❏
❏
❏
❏
❏
❏
❏
❏
❏
❏
❏
❏
❏
❏
❏
❏
❏
❏
❏
❏
❏
❏
❏
❏
❏
❏
❏
❏
❏
❏
❏
❏
❏
❏
❏
❏
❏
❏
❏
Содержание York AYK550
Страница 254: ...G YORK A Johnson Controls Company Bypass Package Components Note Solution AHU Does Not have VFD Input Service Switch...
Страница 259: ...YORK A Johnson Controls Company G 8 Fig 1 7 8 94 4 7...
Страница 260: ...G YORK A Johnson Controls Company Fig 2 7 8 8 94 7...
Страница 261: ...YORK A Johnson Controls Company G 7 8 6 8 94 7 Fig 3...
Страница 262: ...G YORK A Johnson Controls Company Fig 4 7 8 8 94 2 7...
Страница 263: ...YORK A Johnson Controls Company G Fig 5 7 8 6 8 94 7...
Страница 264: ...G YORK A Johnson Controls Company Fig 6 7 8 8 8 94 7...
Страница 265: ...YORK A Johnson Controls Company G Fig 7 7 8 8 94 7...
Страница 266: ...2 G YORK A Johnson Controls Company Fig 8 7 8 H 8 94 4 7...
Страница 267: ...3 YORK A Johnson Controls Company G Fig 9 7 8 6 H 8 94 7...
Страница 268: ...G YORK A Johnson Controls Company 7 8 8 8 94 7 Fig 10...
Страница 269: ...YORK A Johnson Controls Company G Fig 11 J 8 8 94 7...