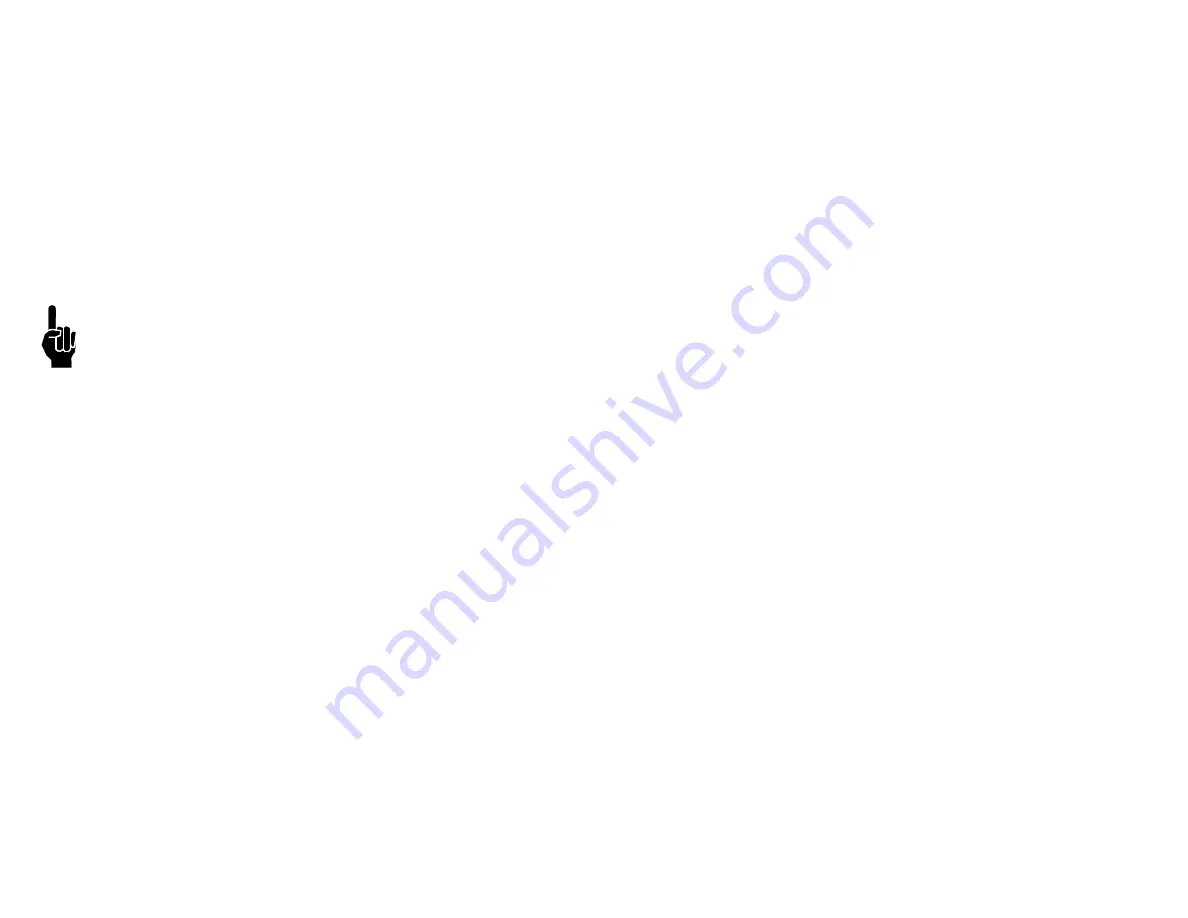
IJ4000 Impulse Jet
Appendix B: Theory of Operation
5765-018 Operations Manual Rev J
Page 56
Print Head Daisy Chain
Print heads attach to the IJ4000 in a daisy chain configuration. The first print head plugs into a Print Head Interface Board (P1), and the second
print head plugs into the first print head. The maximum number of print heads for a 384E daisy chain is two. An IJ4000-HMI Controller can have
one or two daisy chains (one for each Print Head Interface Board).
Electrically, a print head daisy chain is a shift register. A shift register moves bits of information along a line one bit at a time in step with a clock-
ing signal. It works like this: A bit is placed at the entrance to the line of bits and waits for the clock (step) signal. When the clock signal is given,
the bit steps into the first spot on the line. The bit that occupied the first spot in line steps to the second, the second steps to the third, the third to
the fourth, and so on until the last bit in line steps off the end of the line and is lost. Repeat the process enough times and all of the information in
the shift register is replaced. Repeat the process for all dots in the column. A latch (print) signal sent after the dots have been shifted prints the
column.
All daisy chain signals - DATA, CLOCK and LATCH - are generated and controlled by circuitry in the FPGA (Field Programmable Gate Array,
used as a print head driver chip) on the Print Head Interface Board.
Please note that power is applied to the print heads even when the IJ4000 is "turned off." The only way to remove power from the print heads is
to pull the plug.
Print Trigger Photosensor
The photosensor detects when a product is about to pass by the print heads and signals the IJ4000-HMI Controller to start a print cycle. The pho-
tosensor signal is active low, and it must remain low for at least one encoder pulse. Once a print cycle starts, it continues to completion regard-
less of what the photosensor signal does.
The IJ4000 is compatible with through-beam, retro-reflective, and diffused photosensors that work at 24VDC and have a current sinking (or open
collector) output. The photosensor plugs into the Print Head Interface Board (P2).
E
ncoder
The encoder determines the time period between the printing of individual columns, or the print speed. As a product's speed increases, the time
period between columns must decrease, that is, the print speed must increase, to maintain consistent column-to-column spacing. The IJ4000
has two encoder options, external and internal. Use the external encoder when the conveyor speed fluctuates. Use the internal encoder when
the conveyor speed is constant.
The
external encoder
is a 24VDC optical encoder. The encoder's wheel is sized such that the encoder outputs 300 pulses per inch of product
travel. The external encoder plugs into the Print Head Interface Board (J4), and its signal goes to the FPGA where it is used to time the sending
of column data to the print head.
The
internal encoder
signal is a constant frequency pulse stream generated on the Print Head Interface Board. A programmable counter circuit
in the FPGA divides the board's 32 MHz clock by a value calculated from a line speed entered during system setup. When the user selects the
internal encoder, a switch in the FPGA disconnects the external encoder signal from the print timing circuits and connects the output from the
counter circuit.