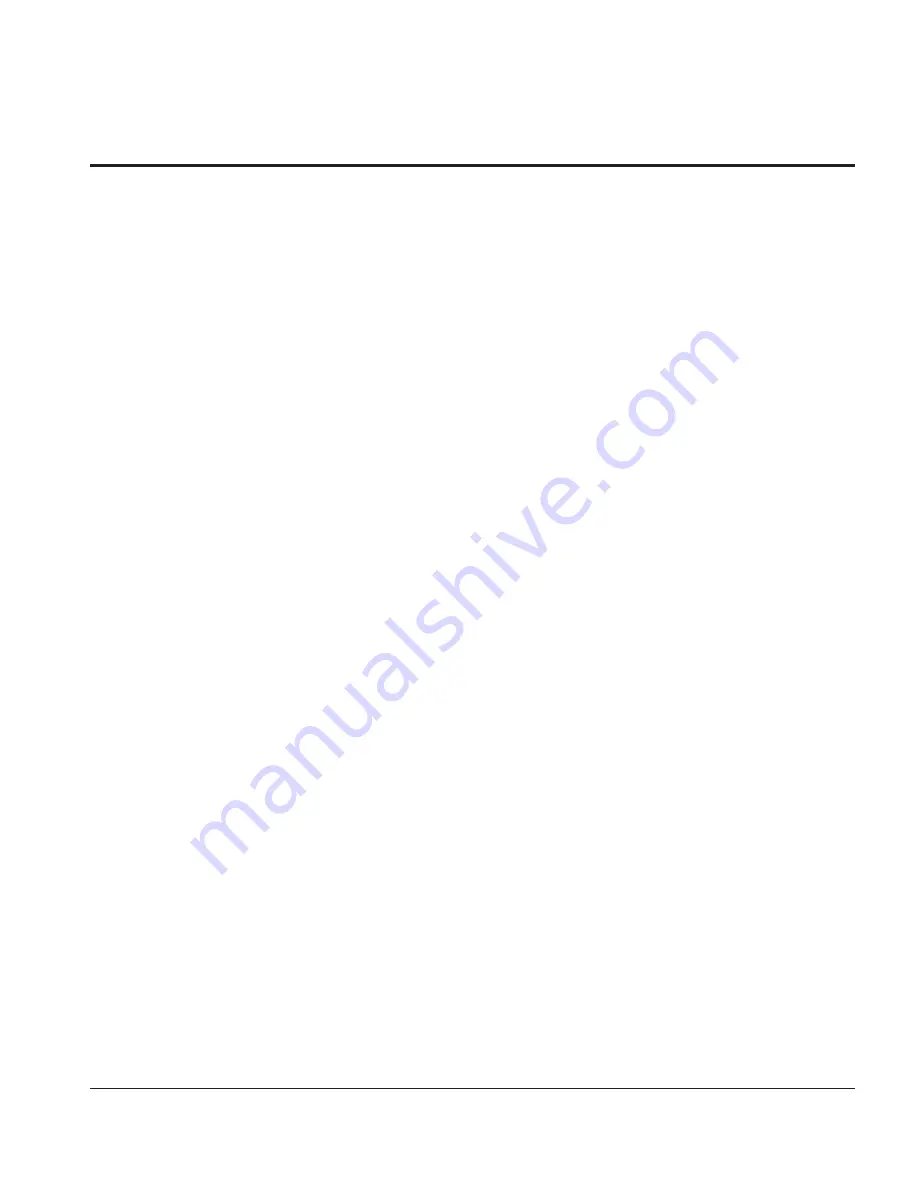
English
Hypertherm Safety and Compliance
PS-1
Introduction
Hypertherm maintains a global Regulatory Management System
to ensure that products comply with regulatory and environmental
requirements.
National and local safety regulations
National and Local safety regulations shall take precedence over any
instructions provided with the product. The product shall be imported,
installed, operated and disposed of in accordance with national and
local regulations applicable to the installed site.
Certification test marks
Certified products are identified by one or more certification test marks
from accredited testing laboratories. The certification test marks are
located on or near the data plate.
Each certification test mark means that the product and its safety-
critical components conform to the relevant national safety standards
as reviewed and determined by that testing laboratory. Hypertherm
places a certification test mark on its products only after that product
is manufactured with safety-critical components that have been
authorized by the accredited testing laboratory.
Once the product has left the Hypertherm factory, the certification test
marks are invalidated if any of the following occurs:
• The product is modified in a manner that creates a hazard or non-
conformance with the applicable standards.
• Safety-critical components are replaced with unauthorized spare
parts.
• Any unauthorized assembly, or accessory that uses or generates a
hazardous voltage is added.
• There is any tampering with a safety circuit or other feature that is
designed into the product as part of the certification, or otherwise.
CE marking constitutes a manufacturer’s declaration of conformity to
applicable European directives and standards. Only those versions of
Hypertherm products with a CE Marking located on or near the data
plate have been tested for compliance with the European Low Voltage
Directive and the European EMC Directive. EMC filters needed to
comply with the European EMC Directive are incorporated within
versions of the power supply with a CE Marking.
Certificates of compliance for Hypertherm products are available from
the Downloads Library on the Hypertherm web site at
https://www.hypertherm.com.
Differences in national standards
Nations may apply different performance, safety or other standards.
National differences in standards include, but are not limited to:
• Voltages
• Plug and cord ratings
• Language requirements
• Electromagnetic compatibility requirements
These differences in national or other standards may make it
impossible or impractical for all certification test marks to be placed
on the same version of a product. For example, the CSA versions
of Hypertherm’s products do not comply with European EMC
requirements, and therefore do not have a CE marking on the data
plate.
Countries that require CE marking or have compulsory EMC
regulations must use CE versions of Hypertherm products with the CE
marking on the data plate. These include, but are not limited to:
• Australia
• New Zealand
• Countries in the European Union
• Russia
It is important that the product and its certification test mark be
suitable for the end-use installation site. When Hypertherm products
are shipped to one country for export to another country; the product
must be configured and certified properly for the end-use site.
Safe installation and use of shape
cutting equipment
IEC 60974-9, titled Arc Welding Equipment – Installation and
use, provides guidance in the safe installation and use of shape
cutting equipment and the safe performance of cutting operations.
The requirements of national and local regulations shall be taken
into consideration during installation, including, but not limited
to, grounding or protective earth connections, fuses, supply
disconnecting device, and type of supply circuit. Read these
instructions before installing the equipment. The first and most
important step is the safety assessment of the installation.
The safety assessment must be performed by an expert, and
determines what steps are necessary to create a safe environment,
and what precautions should be adopted during the actual installation
and operation.
Procedures for periodic inspection and
testing
Where required by local national regulations, IEC 60974-4
specifies test procedures for periodic inspection and after repair or
maintenance, to ensure electrical safety for plasma cutting power
sources built in conformity with IEC 60974-1. Hypertherm performs
the continuity of the protective circuit and insulation resistance tests
in the factory as non-operating tests. The tests are performed with the
power and ground connections removed.
Hypertherm also removes some protective devices that would cause
false test results. Where required by local national regulations, a label
shall be attached to the equipment to indicate that it has passed the
tests prescribed by IEC60974-4. The repair report shall indicate the
results of all tests unless an indication is made that a particular test
has not been performed.
PRoDUCt SteWARDSHIP
Содержание ArcGlide Torch Height Control
Страница 1: ...Instruction Manual 806450 Revision 3 November 2010 ArcGlide THC...
Страница 2: ......
Страница 16: ...English Hypertherm Safety and Compliance S 8...
Страница 34: ...1 14 ArcGlide THC Instruction Manual Specifications...
Страница 48: ...2 12 ArcGlide THC Instruction Manual INSTALLATION...
Страница 100: ...2 64 ArcGlide THC Instruction Manual INSTALLATION...
Страница 202: ...6 4 ArcGlide THC Instruction Manual Wiring Diagrams...
Страница 207: ......
Страница 208: ......