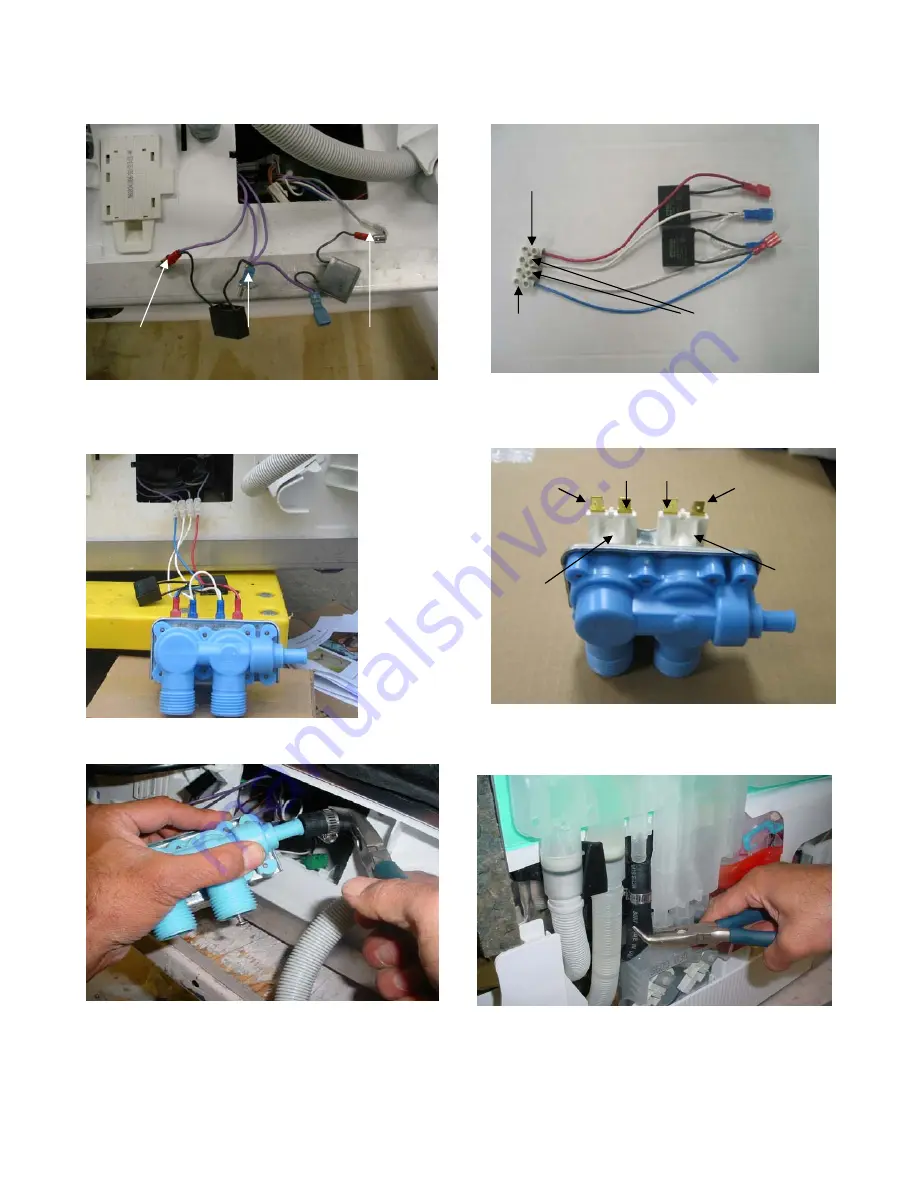
32
Installing New Hot/Cold Inlet Valve
Wiring connections old valve block
New hot/cold valve block wiring harness
Cut purple and gray wires from old valve block New valve block terminals
wiring harness and connect to new harness.
Connect black hose to valve block
Connect black hose to sidebag
Cold water 1
purple wire
Neutral 2
purple wires
Hot water 1
gray wire
Cold water
connection
Hot water
connection
Neutral
connection
Hot
Valve
Red
Wire
Hot
Neutral Wire White
Blue
Wire
Cold
Cold
Valve
Содержание L110W
Страница 1: ...Hydrim L110W Training Manual Training Manual ...
Страница 4: ...4 ...