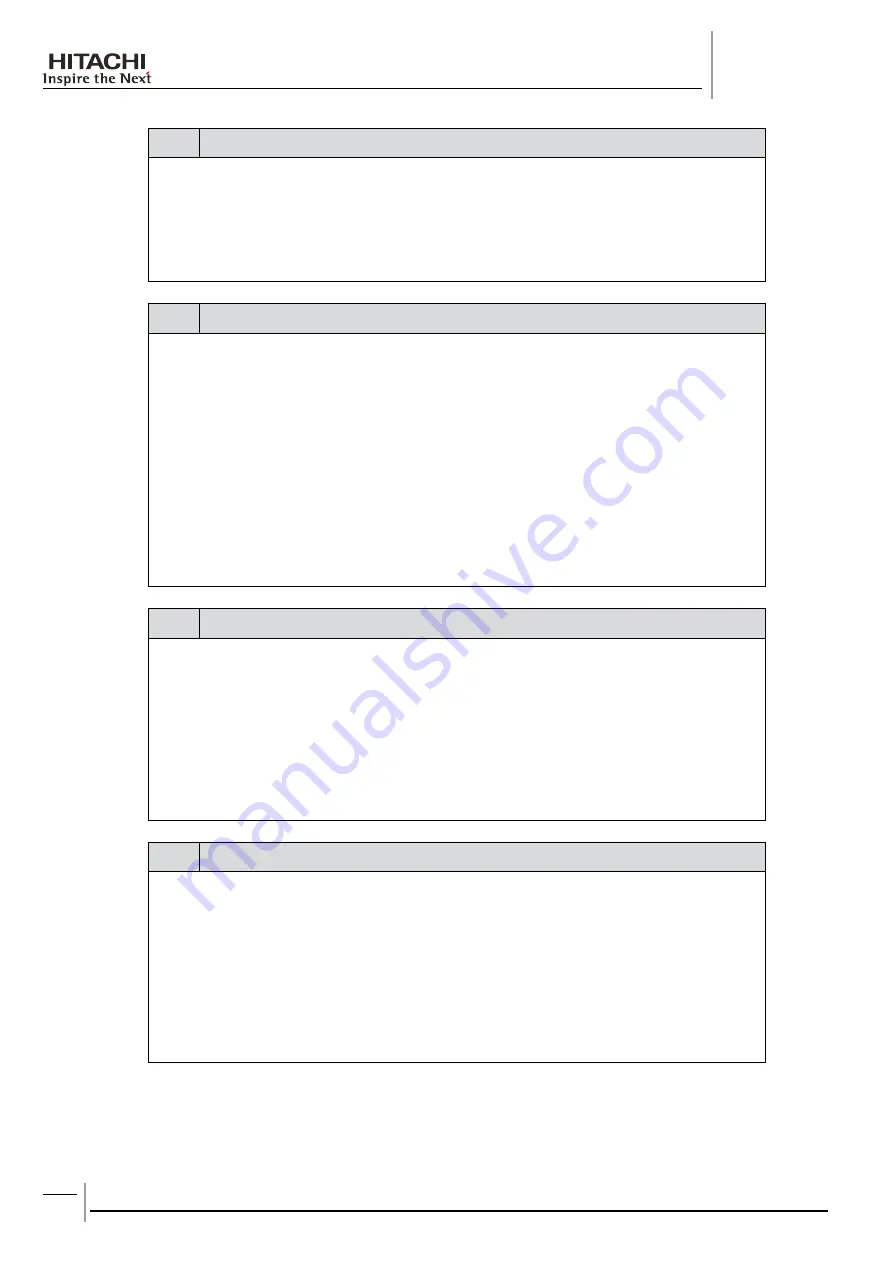
Unit installation
Service Manual
16
Contents
SMGB0066 rev.0 - 12/2009
danger
Electrical hazard. Risk of death.
-
Before gaining access to terminals or performing any maintenance operation, turn OFF all power switches
-
and disconnect all supply circuits.
Check that the LED201 (red) located on the DIP-IPM is OFF.
-
Do not touch the electrical components when LED201 (Red) is ON in order to avoid an electrical shock.
-
Do not touch the electrical components of the PCB directly.
-
warning
Damage by water. Electrical hazard.
-
Install the unit indoors to prevent water contact. The water proof class is IPX0.
-
Install the unit where no high level of oil mist, salty air or sulphurous atmosphere exists.
-
Attach a water proof cover in order to prevent water getting into the unit when installing.
-
Risk of explosion. A fire may occur. Use of inflammable agent may cause explosion or fire. For cleaning
-
operation, use non-inflammable and nontoxic cleaning liquid.
Oxygen deficiency. Toxic gases may be produced. Work with sufficient ventilation. Working in an enclosed
-
space is dangerous. Toxic gas may be produced when cleaning agent is heated to high temperature by, e.g.,
being exposed to fire.
Electric shock. Electrical hazard. In order to avoid electric shock or fire, pay attention not to clamp cables when
-
attaching the service cover.
Electrical hazard. Electrical discharge. This unit contains condensers that might remain charged once the unit
-
is switched off. Wait at least five minutes after the stop of the unit before to start any cleaning or maintenance
operation, allowing the discharge of the condensers.
caution
Malfunction. Unit failure. When installing more than one unit together, keep clearance of more than 500 mm
-
between units and avoid obstacles that could hamper air intake.
Malfunction. Short circuit. Keep cleareance of more than 3000 mm between the wall (without vent holes) and air
-
inlet/outlet.
Electromagnetic contamination. Equipment failures. Install the unit as far as possible (being at least 3 meters)
-
from electromagnetic wave radiator, such as medical equipment.
Overheat of the unit. Malfunction. Install the unit in the shade or not exposed to direct sunshine or direct
-
radiation from high temperature heat source.
Sharp fins. Risk of injury. Aluminium fins have very sharp edges. Pay attention to the fins in order to avoid injury.
-
Use gloves.
note
This appliance is not intended to be used by people (including children) with reduced physical, sensory or
-
mental capabilities, or lack of experience and knowledge, unless they have been given supervision and
instruction concerning the use of the appliance by a person responsible for their safety.
For easy operation and maintenance, install the unit with sufficient clearance around it as shown in the next
-
pages.
Transport the package as close as possible to the intallation location before unpacking.
-
Make sure that the foundation is flat, levelled and strong enough.
-
Install the unit in a place where no seasonal wind might directly blow into the outdoor fan.
-
Install the unit in a restricted area not accessible by the general public.
-
Cleaning liquid shall be collected after cleaning operation.
-
Содержание RHUE-3AVHN
Страница 1: ...Air to water Heat pump RHUE 3AVHN RHUE 4AVHN RHUE 5A V HN RHUE 6A V HN YUTAKI SERIES RHUE A V HN ...
Страница 2: ......
Страница 4: ......
Страница 6: ......
Страница 16: ......
Страница 34: ......
Страница 70: ......
Страница 166: ......
Страница 236: ...Spare parts Service Manual 234 Spare parts of Yutaki SMGB0066 rev 0 12 2009 8 2 2 DHWT Domestic Hot Water Tank ...
Страница 238: ......
Страница 260: ......
Страница 261: ......
Страница 262: ...SMGB0066 rev 0 12 2009 Printed in Spain ...