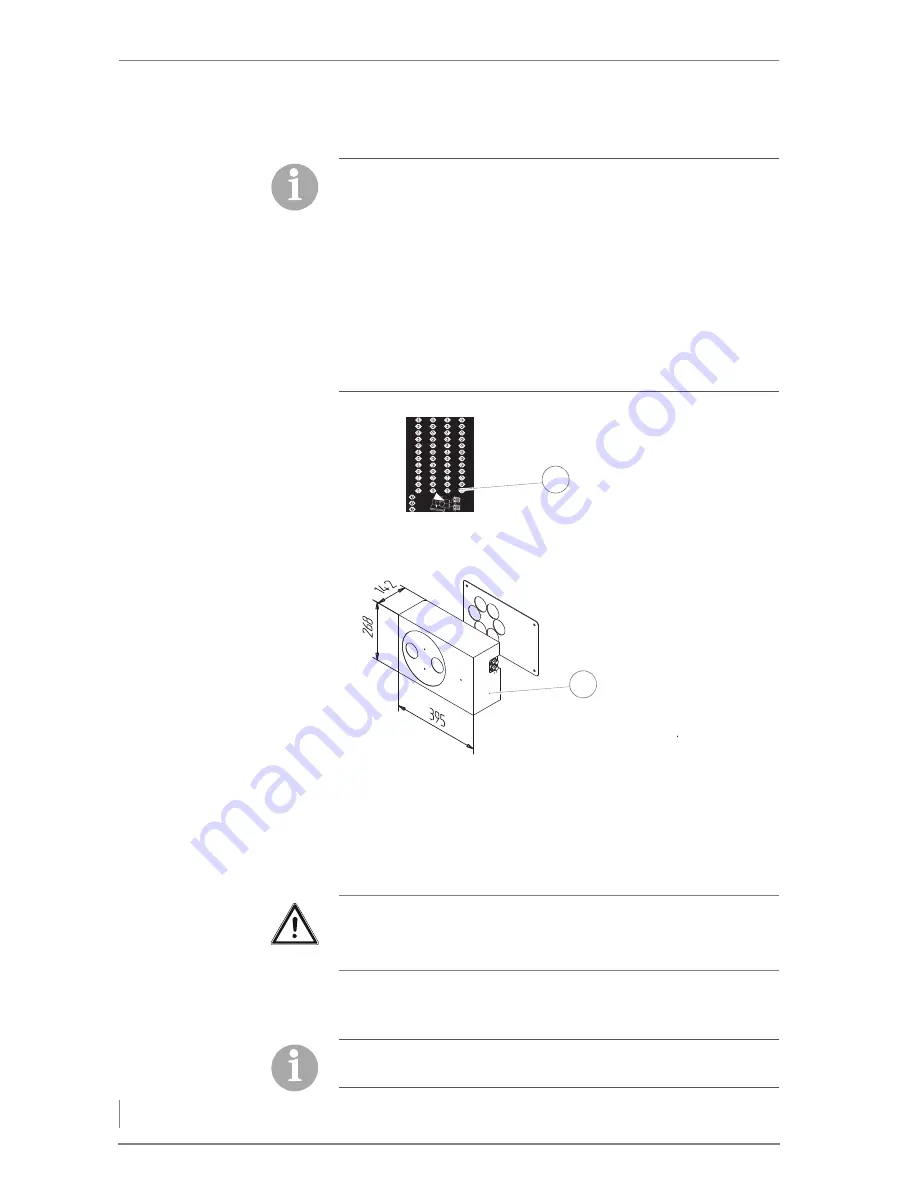
4 Planning and installation – Delivery system
56
HDG
HOSE
JUNCTION
S
COPE
OF
DELIVERY
1 Hose junction incl. cover plate
2 Label for inscription
G
ENERAL
INFORMATION
The HDG hose junction can be installed on a wall or free-standing
with the stand.
Using the stand, the hose junction can be installed free-standing in
the room.
L
ABEL
In order to combine several HDG PSS or FRA-PSS pellet delivery sys-
tems on an HDG pellet vacuum container, the HDG hose junction
can be used. It is positioned between the transfer stations of the PSS
augers and pellet vacuum container.
Accordingly, installation of the hose junction is performed after ins-
tallation of the vacuum and return hose on the transfer station of
the PSS auger.
✎
See the operating manual for the HDG pellet delivery system PSS
or FRA-PSS and the HDG pellet vacuum system, chapter 4 "Plan-
ning and Installation", section 4.5 "HDG pellet vacuum system",
paragraph "Installing the vacuum and return hose".
Figure 4/26 - Accessories for delivery system with suction sensors
05/2010
007057/01
1
2
Important!
The hose junction must be installed using the supplied metal do-
wels in such a way as to ensure problem-free access from outside.
The vacuum hoses are labelled A1, A2 or A3, and the return hoses
B1, B2 or B3, depending on the number of pellet augers.
Содержание Compact 100
Страница 1: ...hdg bavaria com HDG Compact 99 200 Operation Manual ...
Страница 2: ......
Страница 162: ...12 Index 162 HDG Compact 100 105 150 200 Version 1 de HDG Bavaria GmbH Juli 2005 NOTICE ...
Страница 163: ......