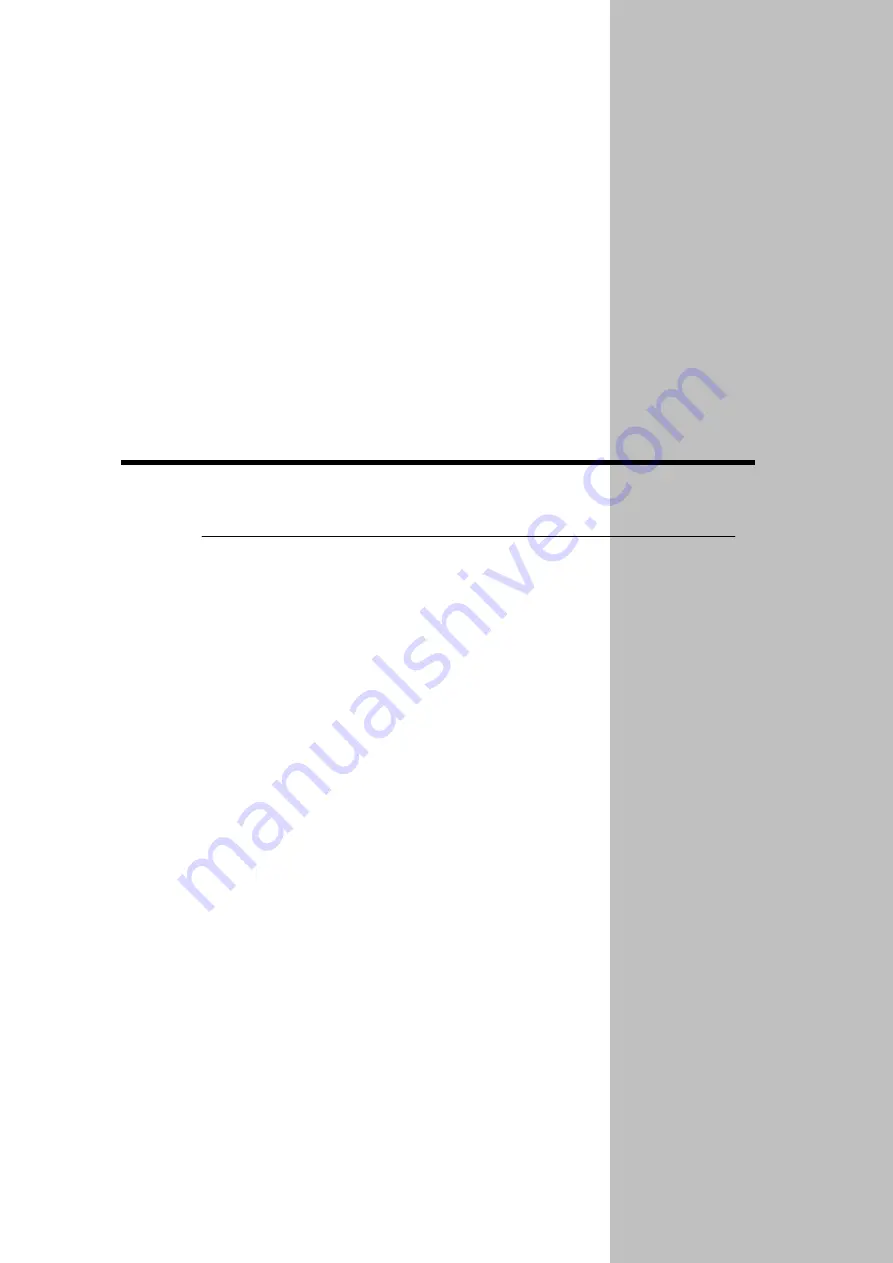
1-13
Chapter 9
Test mode
Details of how to check the system operation by auto-tuning via jogging, monitoring of
I/O signals and simulated operation of output signals are explained in this chapter.
Test mode ········································································ 9-1
Details of test mode ··························································· 9-2
Содержание H A - 800A
Страница 60: ...2 6 Wiring the host device 2 21 4 2 2 1 9 8 7 6 9 8 Installation wiring...
Страница 86: ...3 6 Normal operation 3 25 4 3 3 1 9 8 7 6 9 8 Startup...
Страница 152: ...5 8 Connection example in control mode 5 35 1 2 3 4 5 6 7 8 9 10 11 Appe I O signals...
Страница 166: ...6 1 Operating display panel 6 13 11 10 9 4 7 6 5 4 3 2 1 Panel display and operation...
Страница 188: ...7 6 Details of tune mode 7 21 1 2 3 4 5 6 7 8 9 10 11 Appe Status display mode alarm mode tune mode...
Страница 206: ...8 2 Function extension parameter 8 17 1 2 3 4 5 6 7 8 9 10 11 Appe System parameter mode...
Страница 222: ...9 2 Details of test mode 9 15 1 2 3 4 5 6 7 8 9 Test mode...
Страница 270: ...11 2 Warnings and remedial actions 11 17 1 2 3 4 5 6 7 8 9 10 11 Appe Troubleshooting...
Страница 271: ...1 16 Chapter 12 Option Options you can purchase as necessary are explained 12 1 Option 12 1...
Страница 276: ...12 1 Option 12 5 1 2 3 4 5 6 7 8 12 Option...
Страница 310: ...A 6 Control block diagram A 33 Appendix Apx...