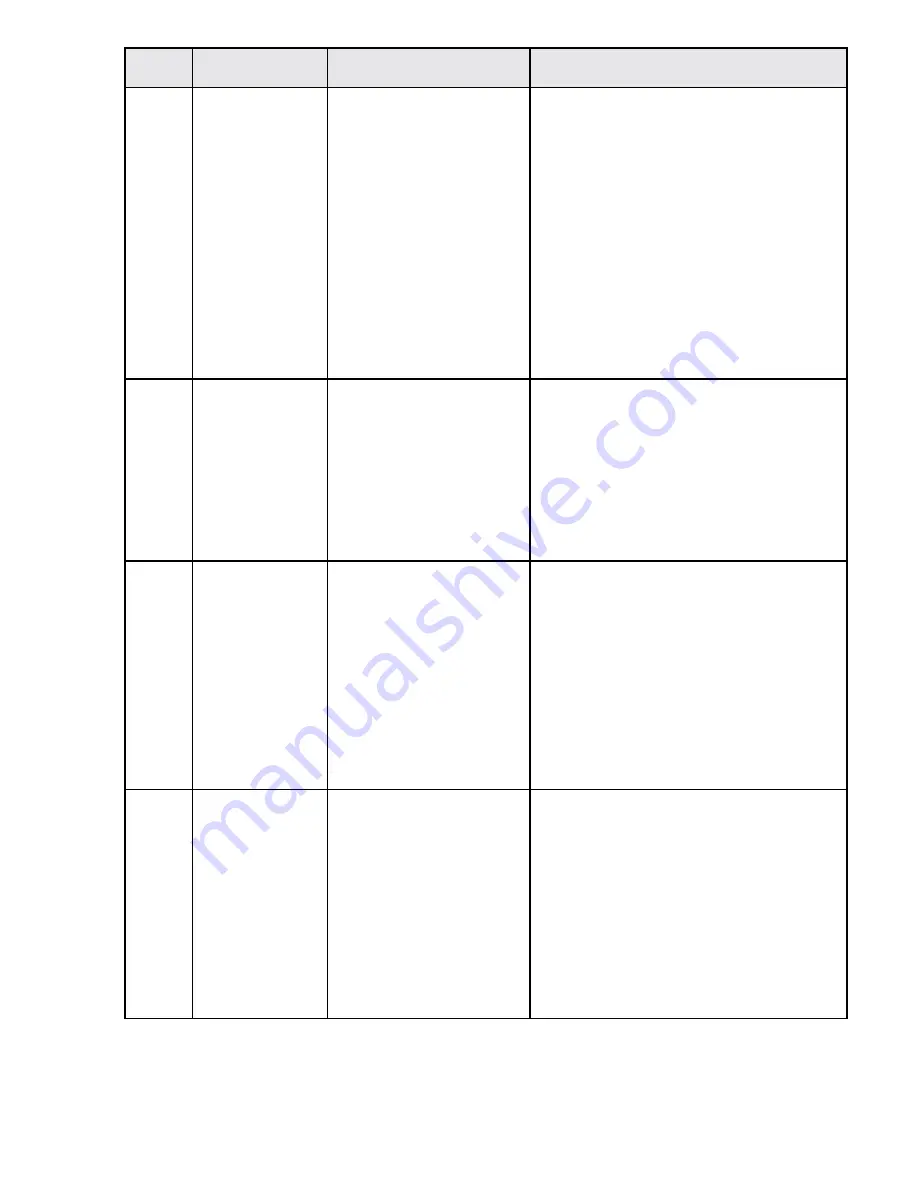
– 75 –
Fault
Code
Description
Trigger Condition
Action
23
Critical Door
Lock Failure
Cycle canceled due to
inability to reach desired
door lock state.
• Verify the door is closed properly, if
door does not close freely, lift the door
until it closes freely.
• Replace door lock and door lock
harness then run below actions.
• Check the door lock using service
mode spin test 14 to ensure door lock
operation.
• Verify that the door lock is not blocked
by any external debris.
• Check door switch continuity at J513 on
the control.
• Check continuity of door lock position.
Opened or Closed.
• Check for proper operation of door lock.
120 VAC while activating.
• Check door lock wiring harness from
the control to lock assembly.
24
Door Logic
Failure
Door lock failure. This
fault is set if the system
perceives the door to be
both OPEN and LOCKED
for 5 consecutive
seconds.
• Replace door lock and door lock
harness, then run below actions.
• Check the door lock using Service
Mode spin test 14 to ensure door lock
operation.
• Check harness and connections from
the control to the door lock assembly
for damage and continuity.
• Run a spin cycle. Pull up on the door
during spin for more than 5 seconds
and see if this fault occurs.
25, 65
Pressure
Sensor Dropout,
Pressure Sensor
Continuous
Gallons Monitor
This fault is set when the
pressure is above 6-in.,
then later drops to less
than 1-in. for 5 seconds
without draining.
• Check to make sure house water
supply valves are turned on.
• Check water valve operation.
• Check for proper drain pipe and stand
pipe height.
• Check pressure tube for pinches where
it goes through control board.
• Use pressure sensor test 10 to ensure
correct pressure sensor operation.
• Check pressure tube for trapped water.
• Ensure pressure chamber port is free
from obstruction using drill bit size 1/16-
in. by hand so as not to drill through the
inner wall.
26
Out of Balance
(OOB) Ended
Final Spin
Washer detected an out
of balance load and was
unable to reach final
target spin speed.
• Run Drain & Spin cycle to ensure
basket reaches final spin speed and
the Spin LED does not blink (a blinking
Spin LED indicates that an out of
balance was detected during final spin).
• Check for any basket loose or damage
or abnormal noise.
• Check to make sure unit is firmly
seated on all four legs, doesn't rock,
and is leveled.
• If washer spins properly, educate
consumer on how to properly load and
distribute their clothes in the washer
basket to prevent an OOB.
(
Continued next page
)