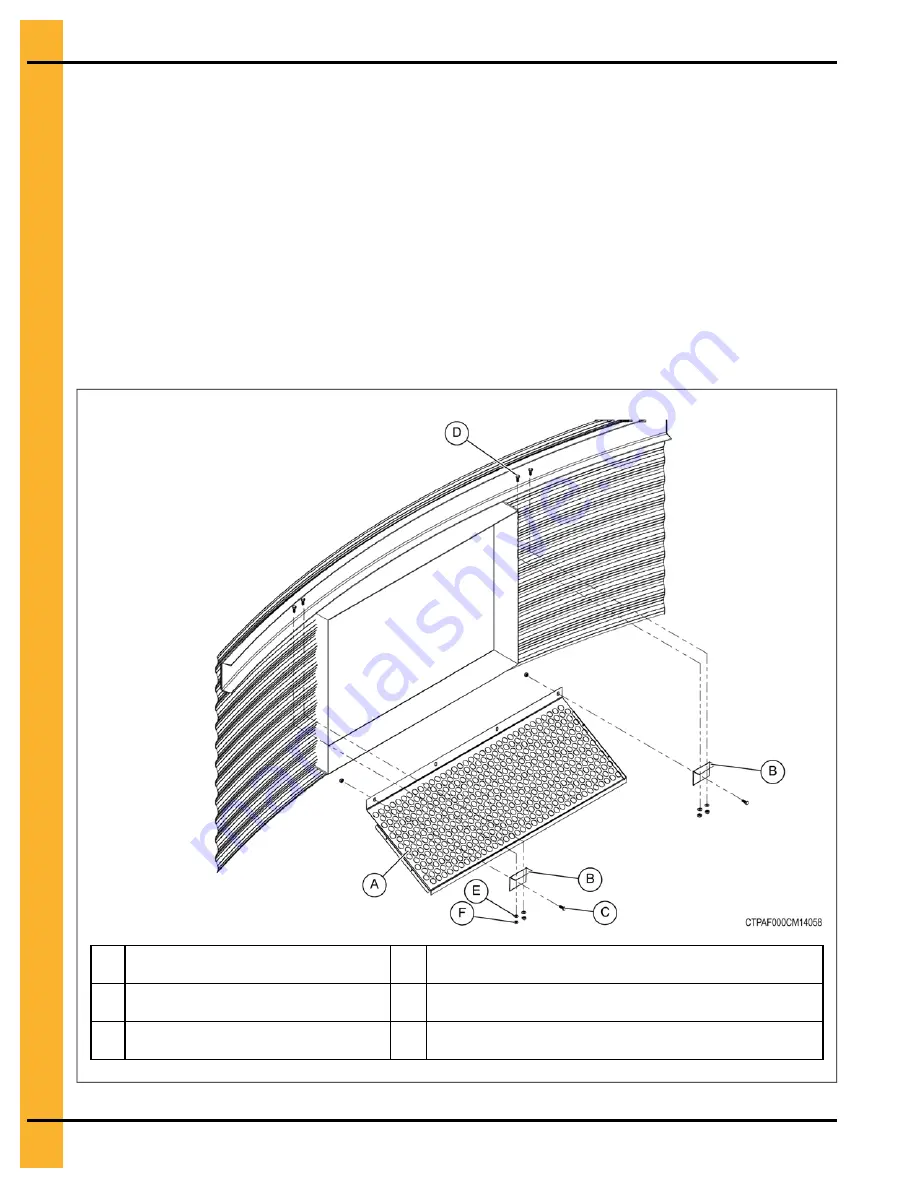
Installing the Fan Diffuser
The diffusers are used to effectively distribute airflow evenly throughout the plenum.
1. Install the diffuser hangers (B) to the end slots of the top plate (A) with the 1/4 x 1 in. self-drilling
screws (C).
2. Center the top plate (A) under the C-channel in front of the fan opening.
3. Mark and drill four 3/8 in. diameter holes into the bottom flange of the C-channel using the diffuser
hangers as a guide.
4. Install the top plate (A) and diffuser hangers (B) to the C-channel using 5/16 x 1 in. flange bolts (D),
5/16 in. flat washer (E) and 5/16 in. hex nuts (F).
Figure 10-1
Installing the top plate
A
Top plate (TD-100665)
D
5/16 x 1 in. flange bolt with sealing washer (S-10260)
B
Diffuser hanger (TD-100750)
E
5/16 in. flat washer (S-845)
C
1/4 x 1 in. self-drilling screw (S-7229)
F
5/16 in. hex nut (S-396)
116
PNEG-4936
36 Ft. TopDry Autoflow
Содержание TopDry Autoflow
Страница 6: ...NOTES 6 PNEG 4936 36 Ft TopDry Autoflow...
Страница 26: ...NOTES 26 PNEG 4936 36 Ft TopDry Autoflow...
Страница 46: ...NOTES 46 PNEG 4936 36 Ft TopDry Autoflow...
Страница 106: ...NOTES 106 PNEG 4936 36 Ft TopDry Autoflow...
Страница 128: ...NOTES 128 PNEG 4936 36 Ft TopDry Autoflow...
Страница 140: ...NOTES 140 PNEG 4936 36 Ft TopDry Autoflow...