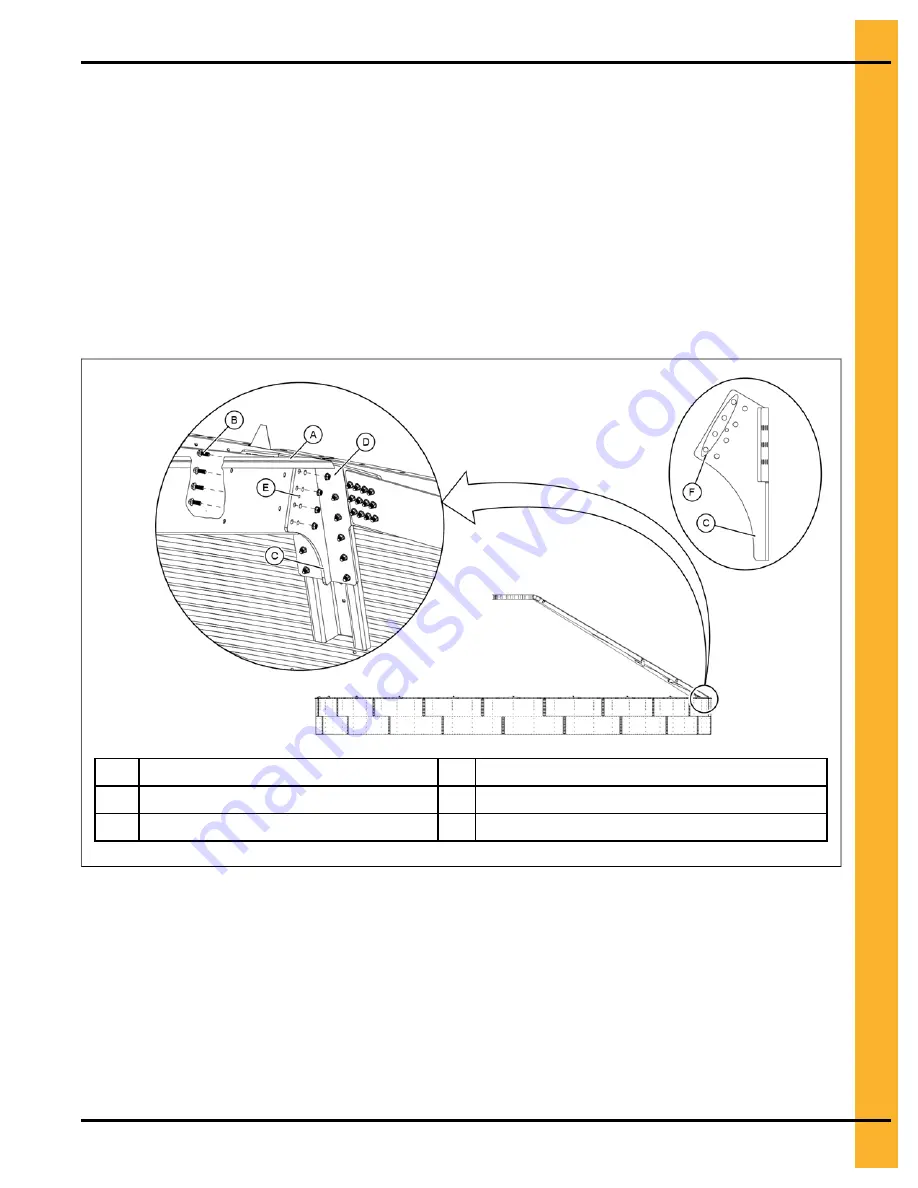
Attaching the A-Frame to the Eave Bracket
The bottom end of the A-frame rafters must be installed to the eave brackets.
1. Lower the A-frame rafter assembly (A) along the side of the eave bracket (C), and align with the
holes nearest to the center collar.
NOTE:
Use the alignment hole (E) in the rafter to help align the holes with a punch tool.
2. Install flange bolts (B) and flange nuts (D), securing one side on the A-frame assembly to the eave
bracket (C).
3. Repeat this procedure for the other side of the A-frame.
4. Tighten to the recommended torque specifications. See
Bolt Torque Specifications, page 28
.
Figure 8-20
Attaching the rafter to the eave bracket
A
A-frame rafter assembly
D
1/2 in. flange nut (S-10253)
B
1/2 x 1-3/4 in. flange bolt (S-10252)
E
Hole for alignment tool
C
Eave bracket (CTR-0429)
After You Finish
Continue to the next A-frame installation until all of the A-frame rafter assemblies are installed. See
Temperature Cable Brackets and A-Frame Assemblies, page 96
.
PNEG-4472
72 Ft Diameter Z-Tek Bins
117
Содержание 40-SERIES
Страница 6: ...NOTES 6 PNEG 4472 72 Ft Diameter Z Tek Bins ...
Страница 18: ...NOTES 18 PNEG 4472 72 Ft Diameter Z Tek Bins ...
Страница 26: ...NOTES 26 PNEG 4472 72 Ft Diameter Z Tek Bins ...
Страница 34: ...NOTES 34 PNEG 4472 72 Ft Diameter Z Tek Bins ...
Страница 72: ...NOTES 72 PNEG 4472 72 Ft Diameter Z Tek Bins ...
Страница 168: ...NOTES 168 PNEG 4472 72 Ft Diameter Z Tek Bins ...