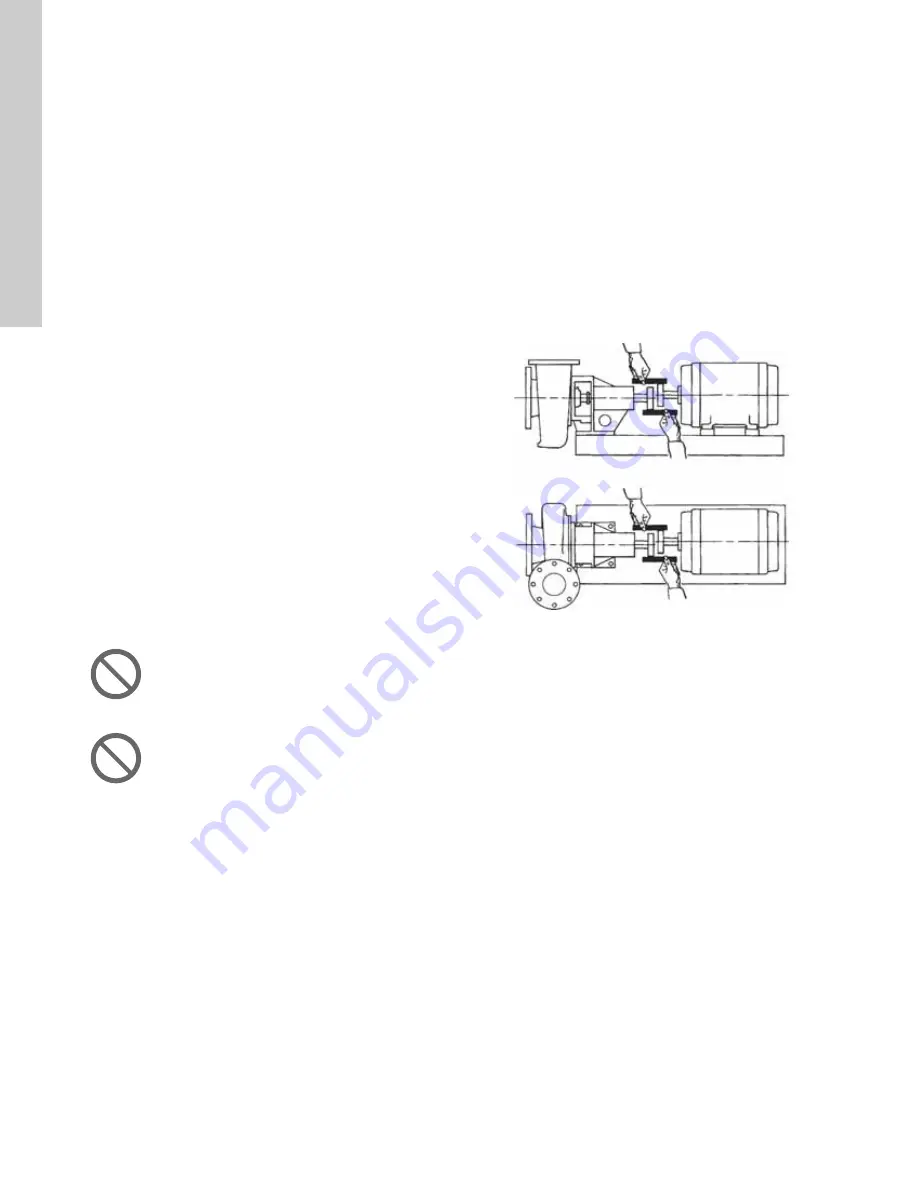
Eng
lish (US)
8
4.4.3 Outlet pipe
• A short outlet pipe can be the same diameter as the pump
outlet port. A long outlet pipe must be one or two sizes larger
than the outlet port, depending on the length.
• An even gradient is best for long horizontal outlet pipes.
• Install a gate valve near the outlet port to be able to isolate the
pump during shutdown and maintenance, and to facilitate
pump removal.
• Any high points in the outlet pipe may entrap air or gas and
thus retard pump operation.
• If water hammer occurs (i.e. if check valves are used), close
the outlet gate valve before pump shutdown.
Shaft seals
The pumps are available with stuffing boxes with packing rings or
mechanical shaft seals.
Stuffing boxes
The stuffing boxes are normally packed before shipment.
If the pump is installed within 60 days after shipment, the packing
material will be in good condition for operation with a sufficient
supply of lubricating liquid.
If the pump is stored for more than 60 days, it may be necessary
to repack the stuffing boxes.
The stuffing box must be supplied at all times with a source of
clean, clear liquid to flush and lubricate the packing rings.
Packing gland adjustment
With the pump running, adjust the packing gland to permit 40 to
60 drops per minute for shaft lubrication. After initial start up,
additional packing and adjustment may be required.
Mechanical shaft seals
Mechanical shaft seals require no maintenance or adjustment.
End suction pumps equipped with mechanical shaft seals are
matched to the operating conditions for which the pump was sold.
Observe the following precautions to avoid shaft seal damage
and obtain maximum shaft seal life.
Clean and purge the inlet pipe in new installations before
installing and operating pump. Pipe scale, welding slag and other
abrasives can cause rapid shaft seal failure.
4.4.4 Coupling alignment of LCSE pumps
No alignment of the pump and motor is required.
4.4.5 Coupling alignment of LFE pumps
The pump and motor were accurately aligned from factory, but
handling during shipment could alter this pre-alignment.
1. If the pump and motor were shipped mounted on a common
base frame as an assembly, remove the coupling guard.
2.
Checking parallel alignment
Place a straight edge across both coupling rims at the top, the
bottom, and both sides. See fig.
4
. After each adjustment,
recheck all features of alignment. Parallel alignment is correct
when the measurements show that all points of the coupling
faces are within ± 0.005 in. (0.127 mm) of each other. If
misalignment is detected, loosen the motor and shift or shim
as necessary to re-align. Then re-tighten the bolts. Always
align the motor to the pump as pipe strain will occur if the
pump is shifted. Never reposition the pump on the base frame.
Fig. 4
Checking parallel alignment
Do not run the pump dry or against a closed valve!
Dry running will cause seal failure within minutes.
Do not exceed the temperature or pressure
limitations for the mechanical shaft seal used.
TM
05
47
94
26
13