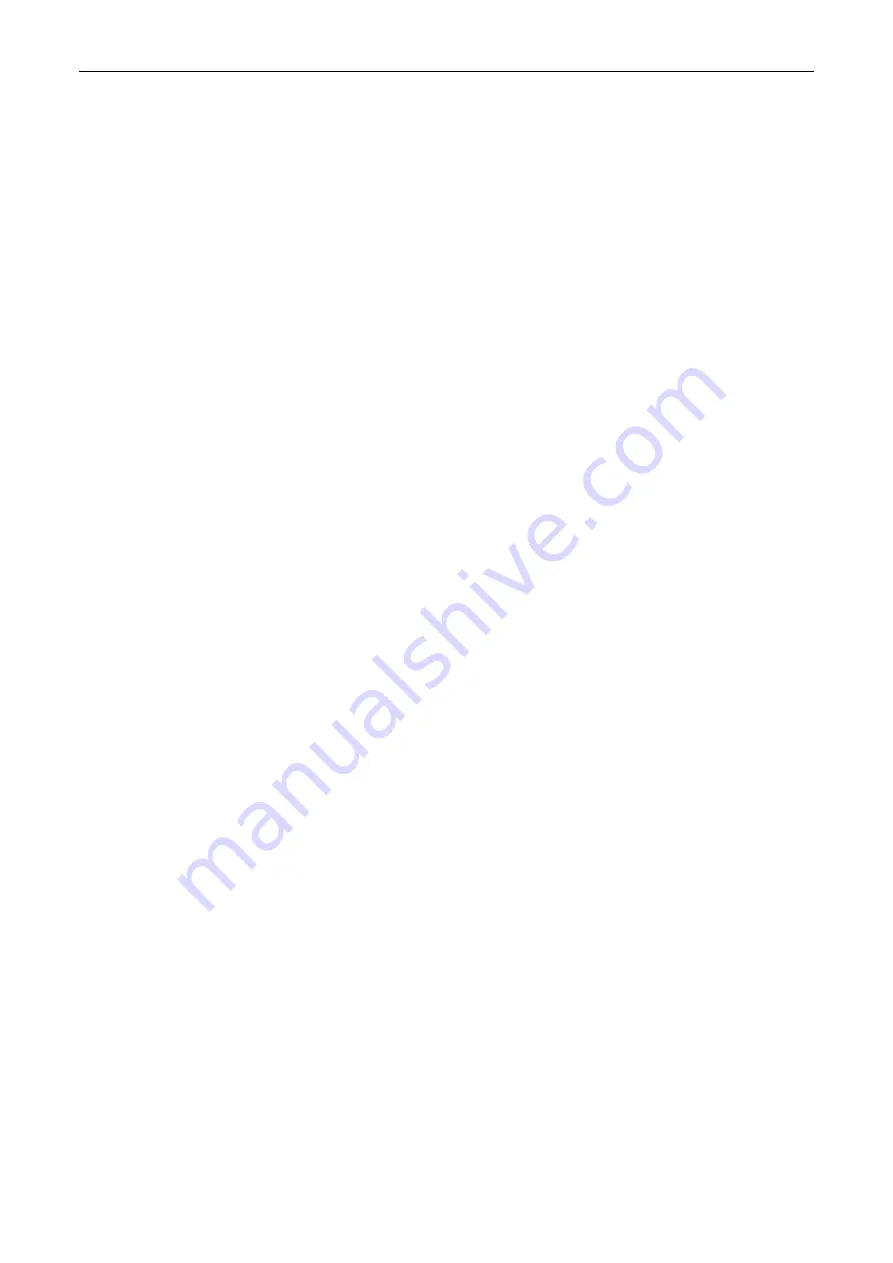
Ultra Heat GMV VRF Technical Service Manual_Heat Recovery Serial INSTALLATION
51
welding joint and the bending part should be less than 100 mm(3.94inch).
1.2.4 Pipe expanding
Pipe expanding is used to provide a welding point for pipe connection. Requirements on pipe
expanding are as follows:
(1) All burrs and sundries inside the pipe must be cleared after cut-off.
(2) Before pipe expanding, apply appropriate amount of lubricant on the surface of the pipe. (The
lubricant must meet the refrigerant system‘s requirements.)
(3) Pipe expanding length must be in accordance with the insertion depth of the caliber.
(4) To avoid leakage due to straight lines at the expanding point, turn round the copper pipe and
then make corrections.
(5) Apply appropriate force during pipe expanding to avoid crack.
1.2.5 Flaring
Another mode of pipe connection is flare opening connection, which requires pipe flaring before
connection. Before pipe flaring, apply appropriate amount of lubricant on the surface of the opening to
ensure smooth pass of flaring nuts and avoid pipe distortion. (The lubricant must meet the refrigerant
system‘s requirements.) The concentricity must be ensured after pipe flaring. The sealing face must be
intact without any burr, crack, or wrinkle.
Requirements on pipe flaring are as follows:
(1) End faces of the copper pipe are smooth.
(2) Burrs and turn ups inside the pipe opening must be cleared.
(3) Install flaring nuts in the pipe before pipe flaring.
(4) The flared opening must be concentric with the main pipe. No eccentricity is allowed.
(5) Put the pipe into the root of the pipe expander.
(6) Longitudinal cracks cannot be generated.
1.3 Installation of Refrigerant Pipes
1.3.1 Operation sequence
The sequence for installing the refrigerant pipe is as follows:
Preparing and installing the support, hanger, and bracket
– Piping according to the drawing –
Cleaning the pipe→Processing the pipe→Adding an insulation sleeve→Connecting the pipe→Fixing the
pipe→Blowing contaminants in the pipe system→Performing a air-tightness test→Performing insulation.
1.3.2 Construction of built-in metal fittings
(1) Construction of supports, hangers, and brackets for pipes
These parts must be fixed securely in reasonable type and style without any tilt. The surface is clean
without any dirt. The parts embedded into the wall or floor cannot be painted or coated and must be free
from grease stains.
(2) Construction of fixing bolts for devices
Ensure sufficient rigidity for the devices. Take anticorrosive measures for exposed part of built-in
fittings. If the foundation must be waterproof, takes waterproof measures.
Содержание Ultra Heat GMV-VQ72W/A-F
Страница 1: ...Ultra Heat GMV Multi VRF TECHNICAL SERVICE MANUAL R410A Heat Recovery Series ...
Страница 26: ...Ultra Heat GMV VRF Technical Service Manual_Heat Recovery Serial INSTALLATION 22 CHAPTER 2 INSTALLATION ...
Страница 30: ...Ultra Heat GMV VRF Technical Service Manual_Heat Recovery Serial INSTALLATION 26 ...
Страница 73: ...Ultra Heat GMV VRF Technical Service Manual_Heat Recovery Serial INSTALLATION 69 ...
Страница 120: ...Ultra Heat GMV VRF Technical Service Manual_Heat Recovery Serial MAINTENANCE 116 CHAPTER 4 MAINTENANCE ...
Страница 135: ...Ultra Heat GMV VRF Technical Service Manual_Heat Recovery Serial MAINTENANCE 131 ...
Страница 136: ...Ultra Heat GMV VRF Technical Service Manual_Heat Recovery Serial MAINTENANCE 132 2 System high pressure protection E1 ...
Страница 137: ...Ultra Heat GMV VRF Technical Service Manual_Heat Recovery Serial MAINTENANCE 133 3 System low pressure protection E3 ...
Страница 167: ...Ultra Heat GMV VRF Technical Service Manual_Heat Recovery Serial MAINTENANCE 163 PFC board Drive board ...
Страница 203: ...Ultra Heat GMV VRF Technical Service Manual_Heat Recovery Serial MAINTENANCE 199 5 4 NCHS4B U ...
Страница 205: ...Ultra Heat GMV VRF Technical Service Manual_Heat Recovery Serial MAINTENANCE 201 5 5 NCHS8B U ...
Страница 207: ...Jf00303410 ...